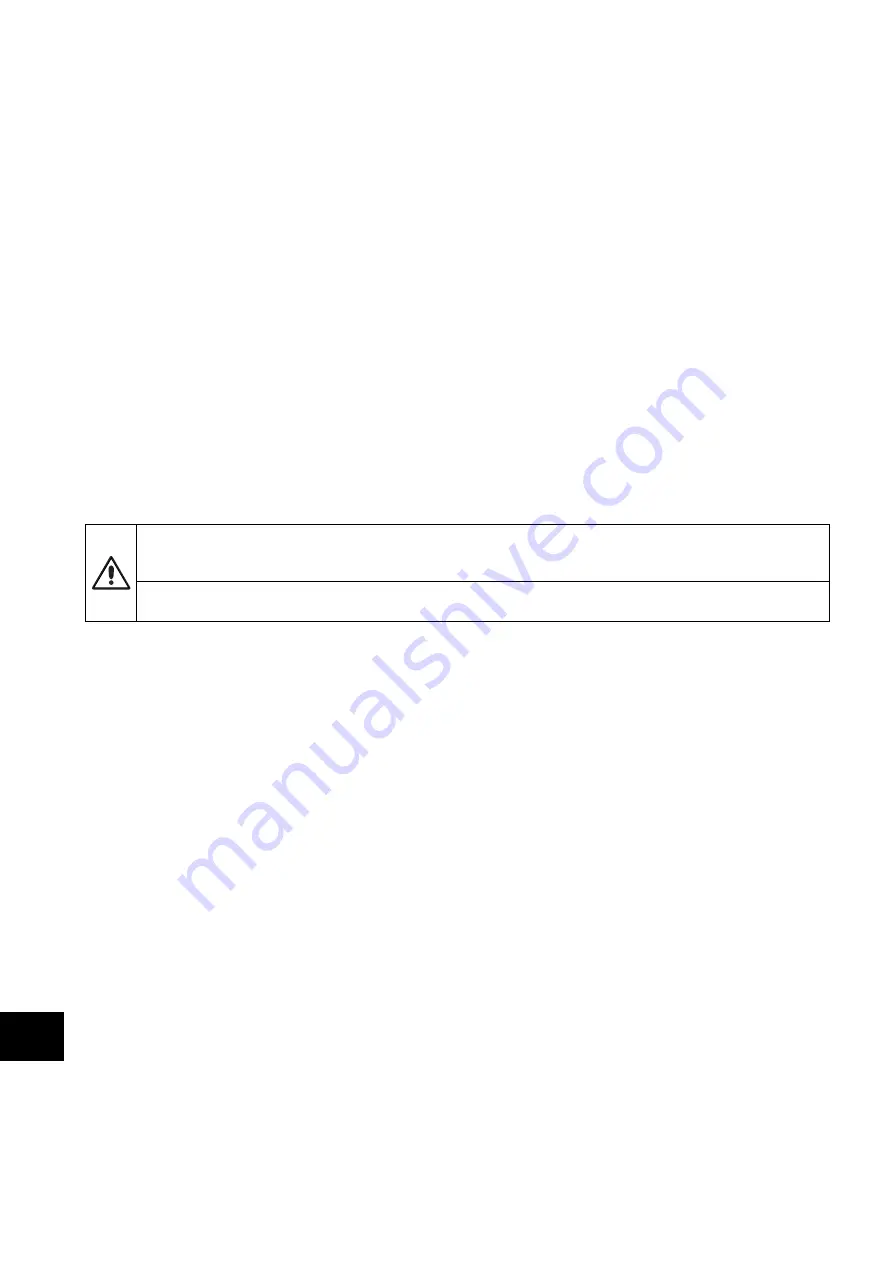
52
| Optidrive ODP-2 Solar Pump User Guide |
Version 2.04
www.invertekdrives.com
9.3.3. IM Motors
IM Motor Control Methods
IM Motors may be operated in the following modes:
Eco Vector Speed Control (CT) (Default Mode)
o This mode provides the simplest control, and is suitable for a wide range of applications with constant torque.
Eco Vector Speed Control (VT)
o This mode provides the simplest control, and is suitable for a wide range of applications with variable torque.
Operating in Eco Vector Speed Control Mode
The P2 Solar Pump drive can be programmed by the user to operate in Sensorless Vector mode, which provides enhanced low speed
torque, optimum motor speed regulation regardless of load and accurate control of the motor torque. In most applications, the default
settings will provide adequate performance, however it is advisable to use the following procedure.
Ensure advanced parameter access is enabled by setting P1-14 = 101.
Enter the motor nameplate details into the relevant parameters as follows:
o P1-07 Motor Rated Voltage
o P1-08 Motor Rated Current
o P1-09 Motor Rated Frequency
o (Optional) P1-10 Motor Rated Speed (Rpm).
Select the required mode VT/CT mode by setting P4-01 = 0 or 1.
Ensure that the motor is correctly connected to the drive.
Carry out a motor data Autotune by setting P4-02 = 1.
The Autotune will begin immediately when P4-02 is set regardless of the status of the drive enable signal. Whilst the autotune
procedure does not drive or spin the motor, the motor shaft may still turn slightly. It is not normally necessary to uncouple the
load from the motor; however the user should ensure that no risk arises from the possible movement of the motor shaft.
It is essential that the correct motor data is entered into the relevant drive parameters. Incorrect parameter settings can
result in poor or even dangerous performance.
9.3.4. PM AC Permanent Magnet AC Motors
The P2 Solar Pump drive can be used to control Permanent Magnet AC motors without a feedback encoder or resolver. These motors
operate synchronously, and a vector control strategy is used to maintain correct operation. In general, the motor can be operated
between 10% - 100% of rated speed with a correctly selected and configured drive. In order to operate a PM motor, the following
parameter settings are necessary.
Ensure advanced parameter access is enabled by setting P1-14 = 101.
Enter the motor details into the relevant parameters as follows:
o P1-07 Back EMF at Rated Frequency / Speed (kE).
This is the voltage imposed by the magnets at the drive output terminals when the motor operates at rated frequency or speed.
Some motors may provide a value for volts per thousand RPM, and it may be necessary to calculate the correct value for P1-07.
o P1-08 Motor Rated Current
o P1-09 Motor Rated Frequency
o (Optional) P1-10 Motor Rated Speed (Rpm).
Select PM Motor Speed control mode by setting P4-01 = 3.
Ensure that the motor is correctly connected to the drive.
Carry out a motor data Autotune by setting P4-02 = 1.
The autotune measures the electrical data required from the motor to ensure good control. Following the steps above, it should be
possible to operate the motor. Further parameter settings are possible to further enhance the performance is required, please refer to
your Invertek Drives Sales Partner for more information.
9.3.5. BLDC Brushless DC Motors
The P2 Solar Pump drive can operate with Brushless DC motors without a feedback encoder or resolver. These motors operate
synchronously, and a vector control strategy is used to maintain correct operation. In general, the motor can be operated between
10% - 100% of rated speed with a correctly selected and configured drive.
Parameter setting and configuration steps for BLDC motor operation are the same as with an AC PM motor, as shown above, with the
exception that P4-01 should be set to 4 for this motor type.
9
Extended P
arameters