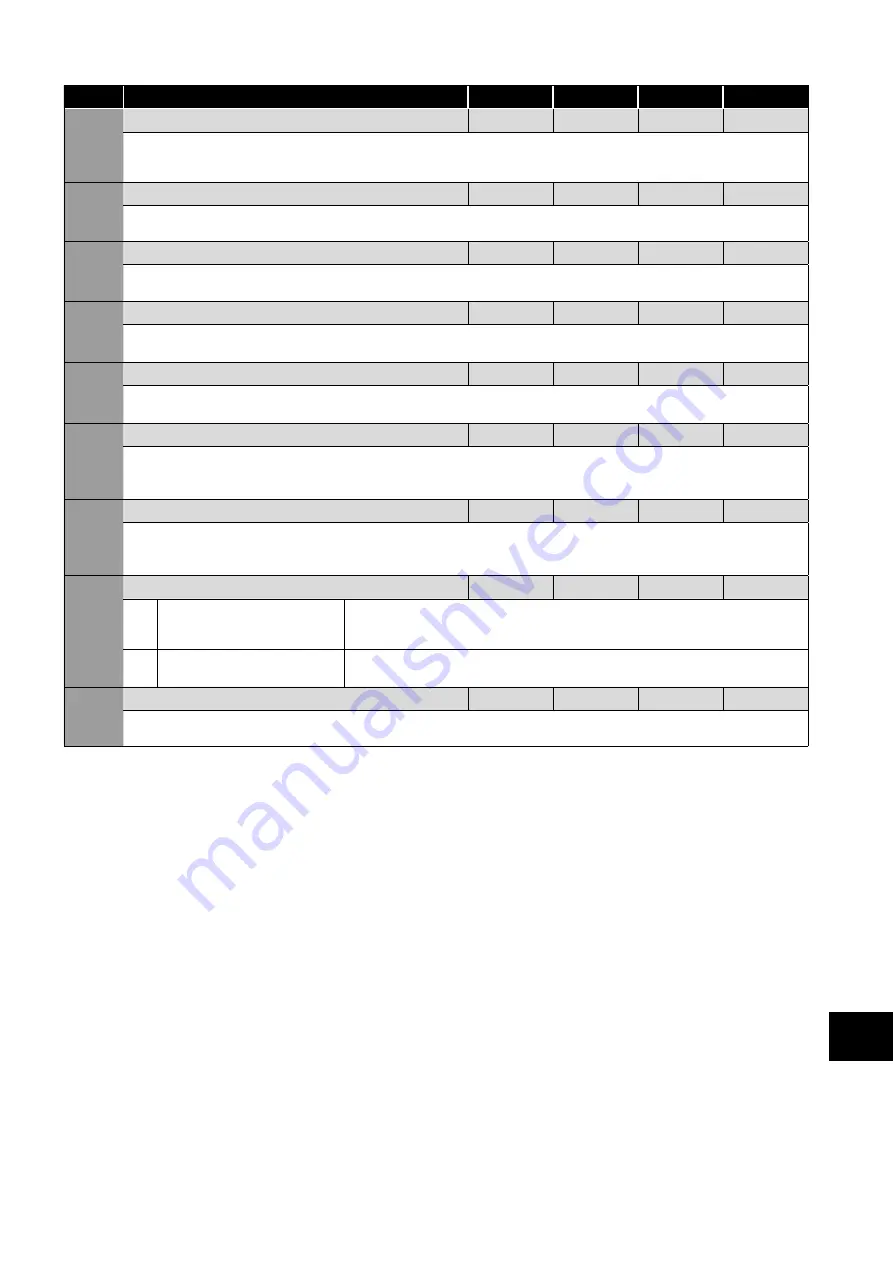
Version 2.04
| Optidrive ODP-2 Solar Pump User Guide |
51
www.invertekdrives.com
Par
Parameter Name
Minimum
Maximum
Default
Units
P3-11
Maximum PID Error to Enable Ramps
0.0
25.0
0.0
%
Defines a threshold PID error level, whereby if the difference between the setpoint and feedback values is less than the set threshold,
the internal ramp times of the drive are disabled. Where a greater PID error exists, the ramp times are enabled to limit the rate of
change of motor speed on large PID errors, and react quickly to small errors.
P3-12
PID Feedback Value Display Scaling Factor
0.000
50.000
0.000
-
Applies a scaling factor to the displayed PID feedback, allowing the user to display the actual signal level from a transducer, e.g. 0 –
10 Bar etc.
P3-13
PID Error Wake Up Level
0.0
100.0
5.0
%
Sets a programmable level whereby if the drive enters standby motor whilst operating under PID control, the selected feedback signal
must fall below this threshold before the drive will return to normal operation.
P3-14
Standby Speed Threshold
0.0
P1-01
0.0
Hz / Rpm
Determines the level at which the drive will enter into standby mode. P2-27 must be set with a value (time) for standby function to be
active. Drive enters standby mode if motor speed remains below the level set in P3-14 for the time period set in P2-27.
P3-15
PID Reference 2 Value
0.0
100.0
0.0
%
When P3-05 = 0, and the 2nd digital reference is selected (see section
8.1. Digital Input Configuration Parameter P1-13
) this
parameter sets the preset digital reference (set-point) used for the PID Controller.
P3-16
Pump Prime Time
0
2000
0
Seconds
A value other than zero in this parameter will automatically enable the burst pipe detection function. Each time the drive is enabled whilst
in PID control or is switched to PID control, the drive will monitor the PID feedback level for the time entered in P3-16. If the PID feedback
level does not exceed the threshold entered in P3-17 before the time in P3-16 expires then the drive will trip with “Pr-Lo” (pressure low) trip.
P3-17
Burst Pipe Threshold
0.0
100.0
0.0
%
PID feedback threshold for the burst pipe detection. In direct PID mode, PID feedback should be equal to or greater than this threshold
before the pump prime time (P3-16) expires. In inverse PID mode, PID feedback should be less than or equal to the threshold before
the pump prime time (P3-16) expires.
P3-18
PID Operation Control
0
1
1
-
0
Continuous PID Operation
In this operating mode, the PID controller operates continuously, regardless of whether the
drive is enabled or disabled. This can result in the output of the PID controller reaching the
maximum level prior to the drive enable signal being applied.
1
PID operation on Drive
Enable
In this operating mode, the PID controller only operates when the drive is enabled, and
hence will always start from zero when the drive is enabled.
P3-19
MPPT Iteration Cycle Time
1.0
10.0
10.0
s
This parameter defines the cycle time for each iteration of the MPPT controller. A lower value may allow the system to try to arrive at the
MPPT quicker from a starting point or after recovering from cloud cover but if the value is too short, it can reduce the stability of the system.
9.3. Parameter Group 4 – High Performance Motor Control
9.3.1. Overview
Parameters relating to the motor control are located together in Group 4. These parameters allow the user to
Select the motor type to match the connected motor
Carry out an autotune
Define the torque limits and setpoint source for control methods that support this (vector control methods only).
9.3.2. Working with different motor types
Optidrive P2 is compatible with the following motor types:
IM Induction Motors
PM Permanent Magnet AC Motors
Brushless DC Motors
Synchronous Reluctance Motors.
The parameter set is intended to allow operation with each motor type using the same basic parameter settings. The sections below
provide additional information for each motor type.
9
Extended P
arameters