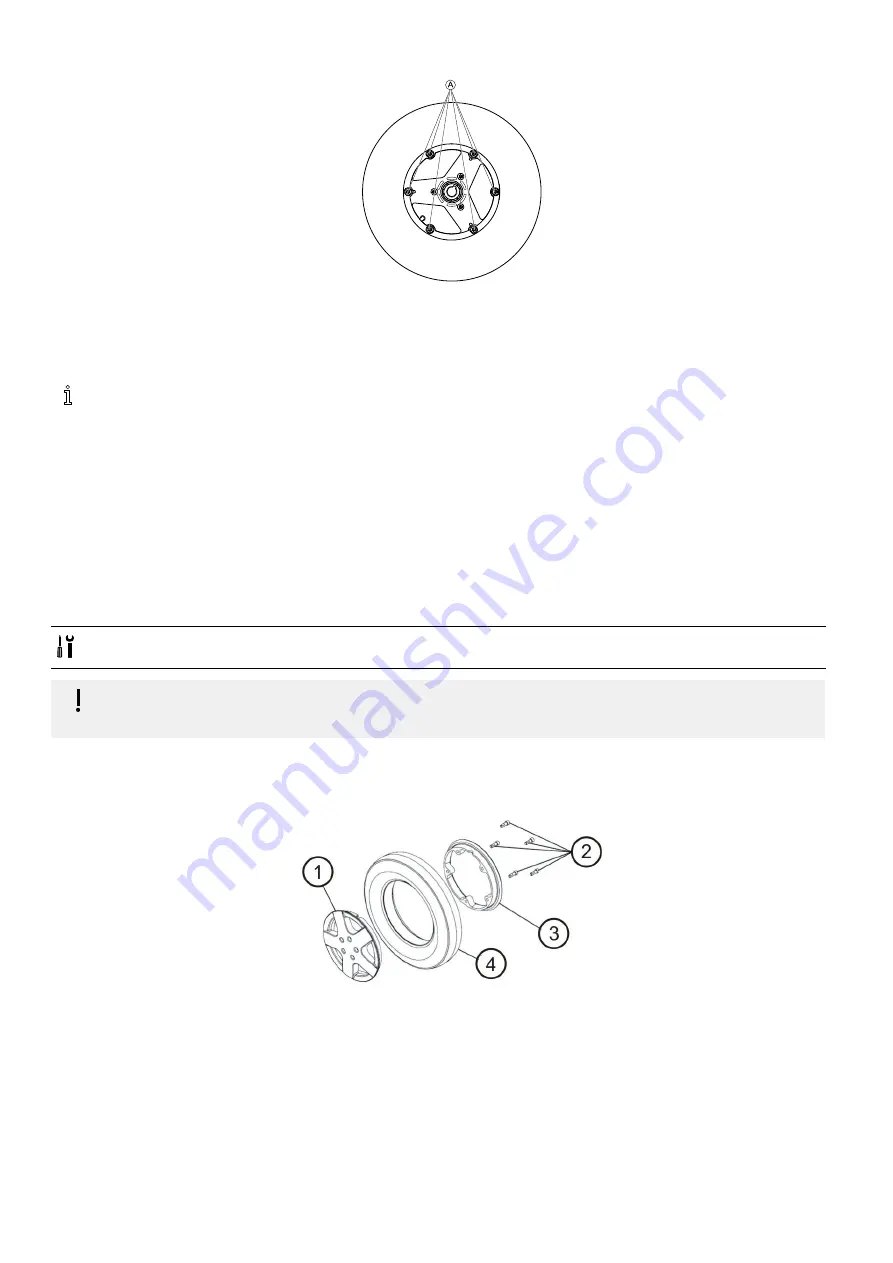
Invacare® Storm⁴ Series
4.
Fig. 6-42 This picture is an example.
Remove screws
A
on inside of wheel.
5.
Remove rim halves from wheel.
6.
Remove inner tube from tyre.
7.
Repair inner tube and re-fit it, or replace it with a new one.
If old inner tube has been repaired and is to be used again, and became wet during repair, it is easier to replace it
if it is lightly dusted with talcum powder beforehand.
8.
Install tyre in reverse order.
9.
Apply rim halves to wheel.
10. Inflate tyre a little.
11. Place screws in wheel rim and tighten screws with prescribed torque. Make sure that inner tube is not clamped
between wheel rim halves.
12. Make sure that tyre is contacting wheel rim directly.
13. Inflate tyre to prescribed pressure.
14. Make sure that tyre is still closely contacting wheel rim.
15. Screw valve cap on.
16. Install wheels according to instruction. See respective chapter.
Repairing Solid Tyre
•
6 mm Allen key
•
3 joiner's clamps with plastic caps
Risk of Damage to Rim Threads
Incorrectly tightened screws can cause damage to rim threads.
– Tighten rim screws with prescribed tightening torque.
1.
Remove wheel as described in respective chapter in this manual.
2.
Secure rim halves against unexpected discharge with three joiner's clamps. When doing so, make sure that you
do not scratch rims.
3.
Fig. 6-43
Loosen and remove screws (2) on inside of wheel.
4.
Loosen joiner's clamps carefully and alternately until you can remove rim halves without risk.
5.
Remove inner (3) and outer (1) half of rim from tyre (4).
6.
Replace any defective or worn parts.
7.
Install tyre in reverse order.
8.
When fitting rim halves together, make sure that drill holes and threads for screws are placed exactly on top of
each other.
9.
Place joiner's clamps in position.
10. Tighten joiner's clamps alternately in small stages until rim halves are precisely aligned.
11. Install and tighten screws.
52
1533060-N
Summary of Contents for Storm 4 Series
Page 4: ...Invacare Storm Series 7 Accessories 97 7 1 Accessories list 97 4 1533060 N...
Page 98: ...Notes...
Page 99: ...Notes...
Page 100: ...Notes...
Page 101: ...Notes...