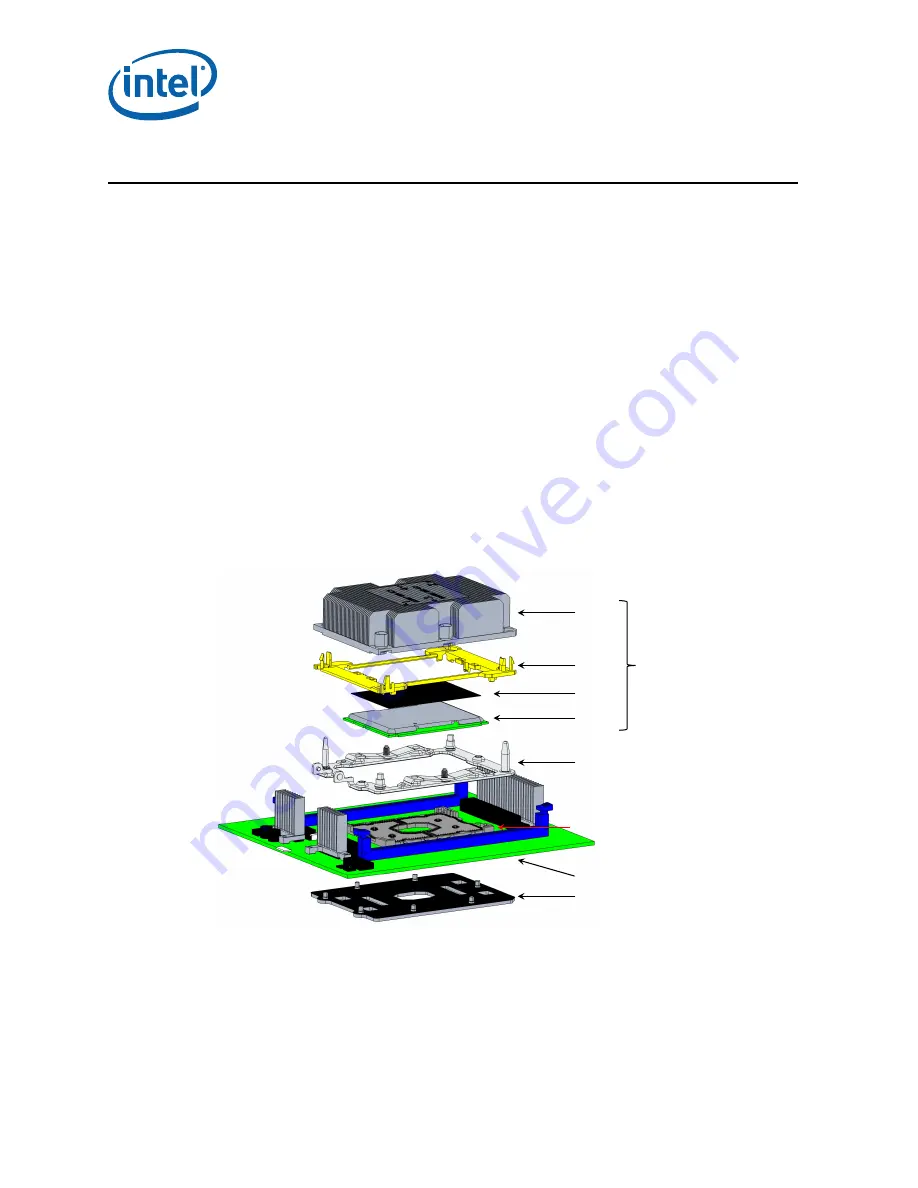
Introduction
Intel
®
Xeon
®
Phi™ Processor x200 Product Family TMSDG
Order Number: 334785-002
8
1
Introduction
1.1
Objective
This document provides processor thermal/mechanical specifications and design
guidelines for development of thermal and mechanical solutions for the Intel
®
Xeon
Phi™ Processor x200 Product Family. This second generation Intel
Xeon Phi product
family now offers a line of socketed processors in addition to a line of PCIe* card-based
coprocessors; but the coprocessor offerings are not discussed in this document.
Throughout this document, unless specified otherwise, the term “processor” represents
any member of the Intel Xeon Phi Processor x200 Product Family; where distinction is
necessary, the term “processor with fabric” will represent the Intel Xeon Phi™
processor with integrated Intel
®
Omni-Path Fabric (Intel
®
OP Fabric).
1.2
Scope
provides a conceptual illustration of the processor mechanical assembly.
Explicit hardware design and assembly details are provided in
of this document.
Figure 1-1. Processor Mechanical Assembly
Heatsink
Assembly
Package
Carrier
TIM
(PCM45F)
Processor
Bolster Plate
Assembly
Socket-P1
Main Board
Back Plate
Assembly
Processor
Heatsink
Loading
Module
(PHLM)
The components and information described in this document include:
• Processor package mechanical design specifications and integration guidelines.
• Processor socket mechanical design specifications and integration guidelines.
• Processor and heatsink mechanical retention assembly design specifications and
system design and integration guidelines.
— Back and bolster plate assembly design details, including loading targets.