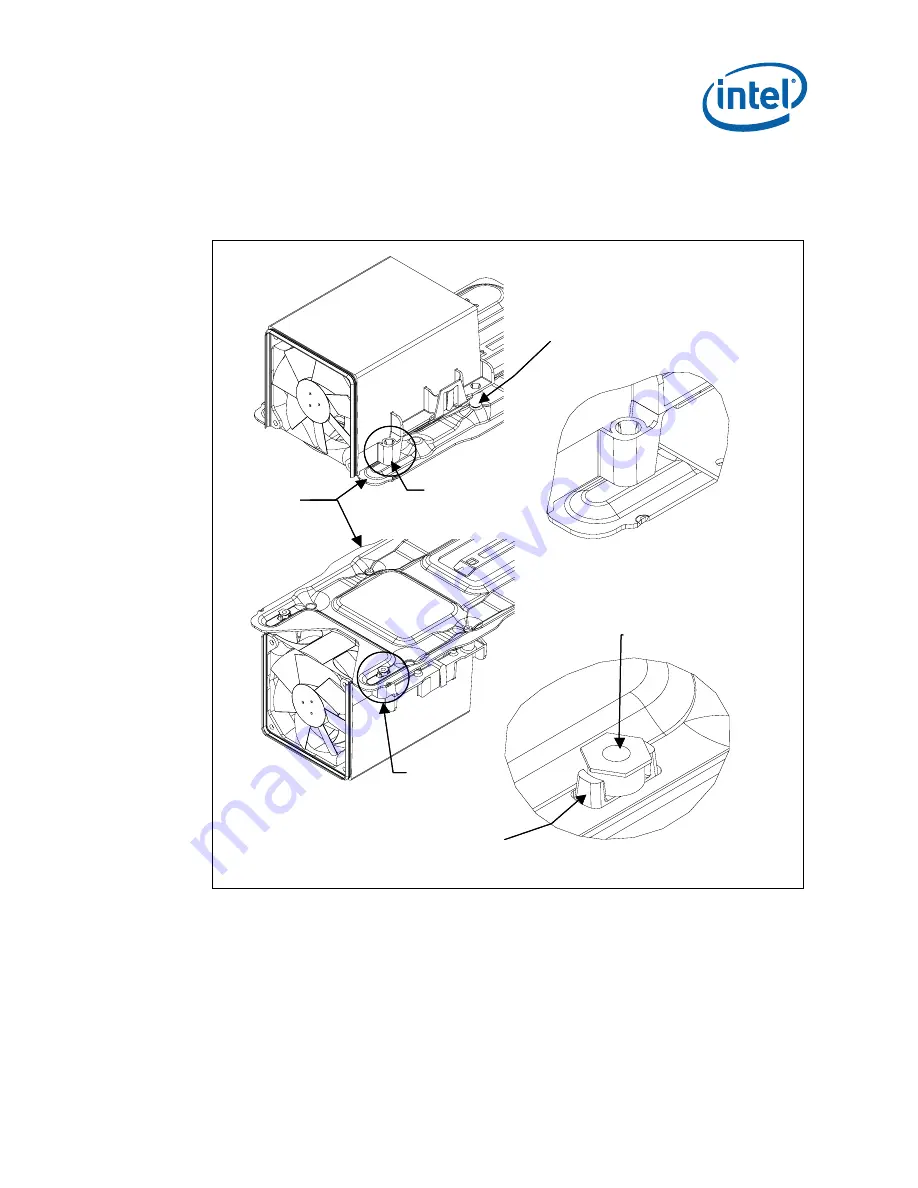
Balanced Technology Extended (BTX) Thermal/Mechanical Design Information
Thermal and Mechanical Design Guidelines
53
mounting hole position for TMA attach, the required preload is approximately 10-15N
greater than the values stipulated in Figure
5-6; however, Intel has not conducted any
validation testing with this TMA mounting scheme.
Figure
5-7. Thermal Module Attach Pointes and Duct-to-SRM Interface Features
SRM
Front attach point
use 6x32 screw
See detail A
Detail A
See detail B
Detail B
Rear attach point
use 6x32 screw
Chassis PEM nut
Duct front interface
feature see note 2
SRM
Front attach point
use 6x32 screw
See detail A
Detail A
See detail B
Detail B
Rear attach point
use 6x32 screw
Chassis PEM nut
Duct front interface
feature see note 2
NOTES:
1.
For clarity the motherboard is not shown in this figure. In an actual assembly, the
captive 6x32 screws in the thermal module pass through the rear holes in the
motherboard designated in the socket keep-in Figure
Appendix H and screw into the SRM and chassis PEM features.
2.
This front duct ramp feature has both outer and inner lead-in that allows the feature to
slide easily into the SRM slot and around the chassis PEM nut. Note that the front PEM
nut is part of the chassis not the SRM.
§
Summary of Contents for Celeron Dual-Core E1000 Series
Page 10: ...10 Thermal and Mechanical Design Guidelines...
Page 26: ...Processor Thermal Mechanical Information 26 Thermal and Mechanical Design Guidelines...
Page 68: ...ATX Thermal Mechanical Design Information 68 Thermal and Mechanical Design Guidelines...
Page 86: ...Heatsink Clip Load Metrology 86 Thermal and Mechanical Design Guidelines...
Page 88: ...Thermal Interface Management 88 Thermal and Mechanical Design Guidelines...
Page 120: ...Legacy Fan Speed Control 120 Thermal and Mechanical Design Guidelines...
Page 126: ...Fan Performance for Reference Design 126 Thermal and Mechanical Design Guidelines...
Page 127: ...Fan Performance for Reference Design Thermal and Mechanical Design Guidelines 127...