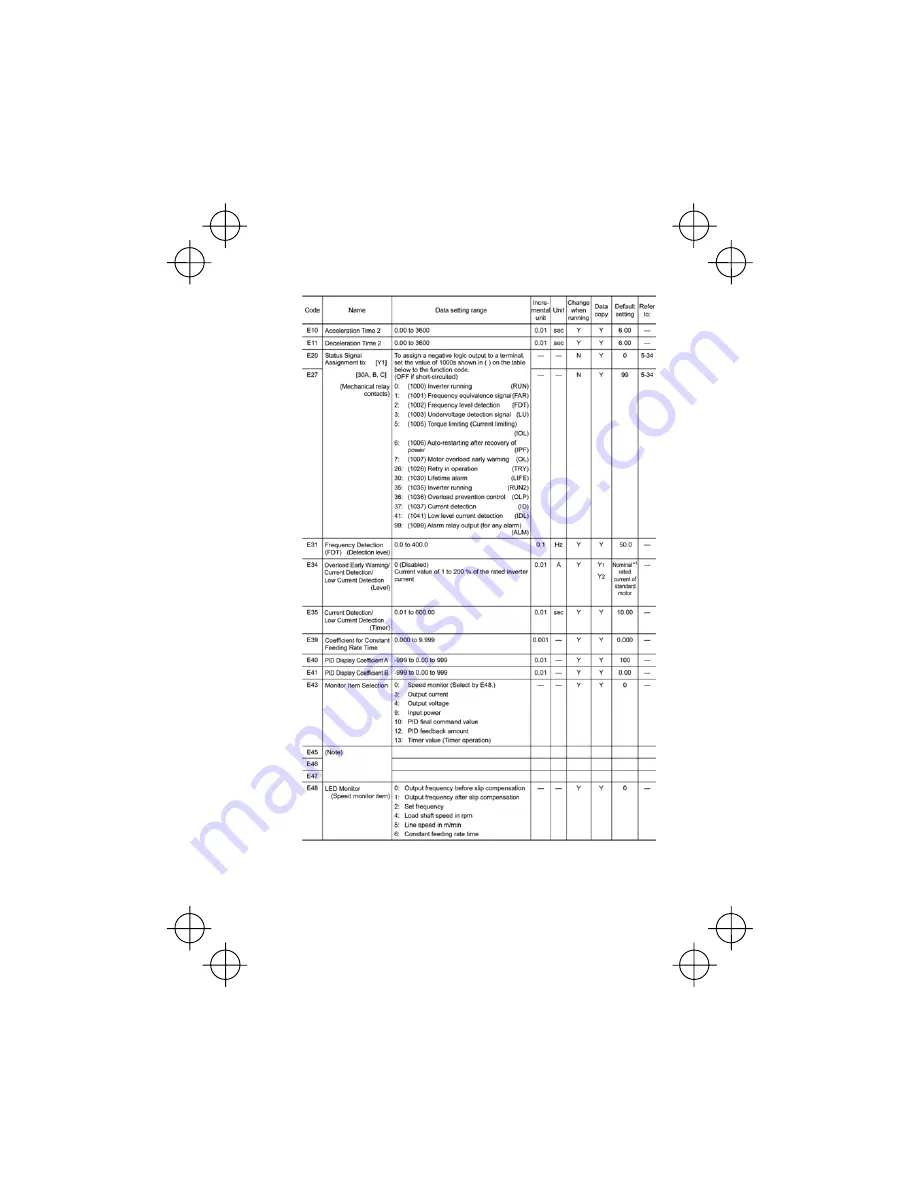
5-6
(Note) Function codes E45 to E47 appear on the LED monitor; however, the Jaguar CUB series of inverters does not recognize
these codes.
*1 “Standard torque boost," "Nominal rated current of standard motor," and "Nominal rated capacity of standard motor"
differ depending upon the rated input voltage and rated capacity. Refer to Table 5.1 "Standard Motor Parameters" on
page 5-12.
Summary of Contents for Jaguar CUB
Page 47: ...3 5 Figure 3 2 Alarm Mode Status Transition...
Page 77: ...5 4...
Page 78: ...5 5 E codes Extension Terminal Functions...
Page 80: ...5 7...
Page 81: ...5 8 C codes Control Functions of Frequency...
Page 84: ...5 11 y codes Link Functions...
Page 149: ...8 5 8 3 Common Specifications...
Page 150: ...8 6...
Page 153: ...8 9 8 5 External Dimensions 8 5 1 Standard Models...
Page 154: ...8 10...
Page 155: ...8 11 8 5 2 Models Available on Order EMC Filter Built in Type...
Page 156: ...8 12...