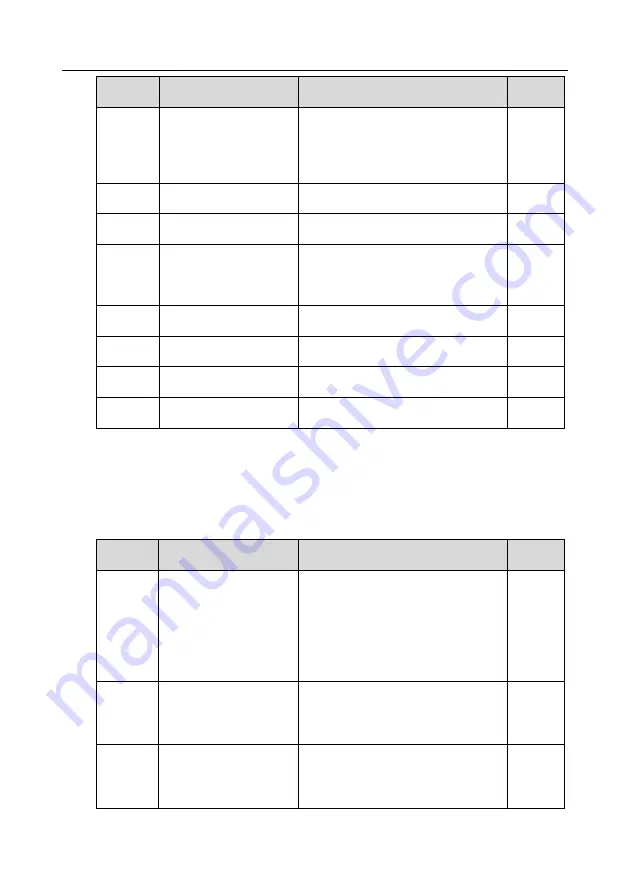
HD2 IP55 High-ingress Protection Series
Basic Operation Instructions
-103-
Function
code
Name
Description
Default
value
11: Set via high speed pulse HDIB
12: Set via pulse string AB
13: Set via EtherCAT/PROFINET
communication
14: Set via PLC card
P00.11
Acceleration time 1
0.0–3600.0s
Depend
on model
P00.12
Deceleration time 1
0.0–3600.0s
Depend
on model
P05.01–
P05.06
Digital input function
selection
26: Wobbling frequency pause (stop at
current frequency)
27: Wobbling frequency reset (revert to
center frequency)
/
P08.15
Amplitude of wobbling
frequency
0.0–100.0% (relative to set frequency)
0.0%
P08.16
Amplitude of jump
frequency
0.0–50.0% (relative to amplitude of
wobbling frequency)
0.0%
P08.17
Wobbling frequency rise
time
0.1–3600.0s
5.0s
P08.18
Wobbling frequency fall
time
0.1–3600.0s
5.0s
5.5.17
Local encoder input
The HD2 IP55 series inverter supports pulse count function by inputting the count pulse from
HDI high-speed pulse port. When the actual count value is no less than the set value, digital
output terminal will output count-value-reached pulse signal, and the corresponding count value
will be zeroed out.
Function
code
Name
Description
Default
value
P05.00
HDI input type
0x00–0x11
Ones: HDIA input type
0: HDIA is high-speed pulse input
1: HDIA is digital input
Tens: HDIB input type
0: HDIB is high-speed pulse input
1: HDIB is digital input
0x00
P05.38
HDIA high-speed pulse
input function
0: Set input via frequency
1: Reserved
2: Input via encoder, used in combination
with HDIB
0
P05.44
HDIB high-speed pulse
input function selection
0: Set input via frequency
1: Reserved
2: Input via encoder, used in combination
with HDIA
0
Summary of Contents for HD2 IP Series
Page 1: ......
Page 16: ......
Page 40: ......
Page 107: ......
Page 176: ...HD2 IP55 High ingress Protection Series Inverter 162 Function parameter list...
Page 213: ......
Page 271: ...HD2 IP55 High ingress Protection Series Troubleshooting 251 7 6 8 Overcurrent...
Page 294: ...HD2 IP55 High ingress Protection Series Inverter 274...
Page 360: ...HD2 IP55 High ingress Protection Series Inverter 340...
Page 361: ......