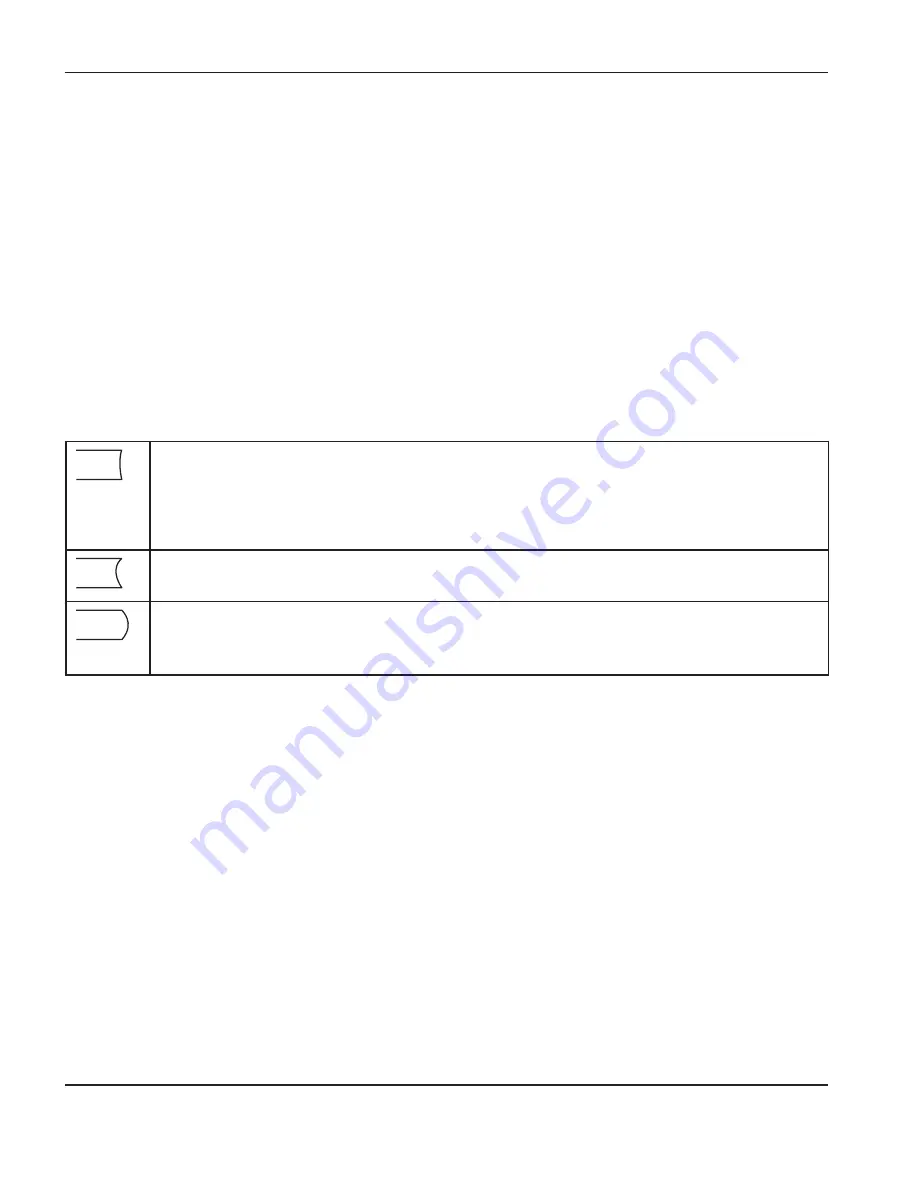
OPeRATION
4-26
powermax
65/85
Operator Manual
High-speed dross forms when the cutting speed is too fast and the arc angles behind. It forms
as a thin, linear bead of solid metal attached very close to the cut. It is more firmly attached to the
bottom of the cut than at low speed and is difficult to remove. To reduce high-speed dross:
• Decrease the cutting speed.
• Decrease the torch-to-work distance.
ote:
N
Dross is more likely to form on warm or hot metal than on cool metal. For example,
the first cut in a series of cuts usually produces the least dross. As the workpiece
heats up, more dross can accumulate on subsequent cuts.
Worn or damaged consumables may produce excess dross.
Straightness of the cut surface
A typical plasma cut surface is slightly concave.
The cut surface may become more concave, or convex. Correct torch height is
required to keep the cut surface acceptably close to straight. Worn consumables also
affect the straightness of the cut.
A strongly concave cut surface occurs when the torch-to-work distance is too low.
Increase the torch-to-work distance to straighten the cut surface.
A convex cut surface occurs when the torch-to-work distance is too great or the
cutting current is too high. First, try lowering the torch, then reduce the cutting
current.
Summary of Contents for Powermax 65
Page 1: ...Plasma arc cutting systems Operator Manual 806650 Revision 0 85 ...
Page 10: ...Table of Contents vi powermax65 85 Operator Manual WARRANTY vi Hypertherm ...
Page 30: ...Specifications 1 16 powermax65 85 Operator Manual ...
Page 140: ...Maintenance and Repair 5 12 powermax65 85 Operator Manual ...