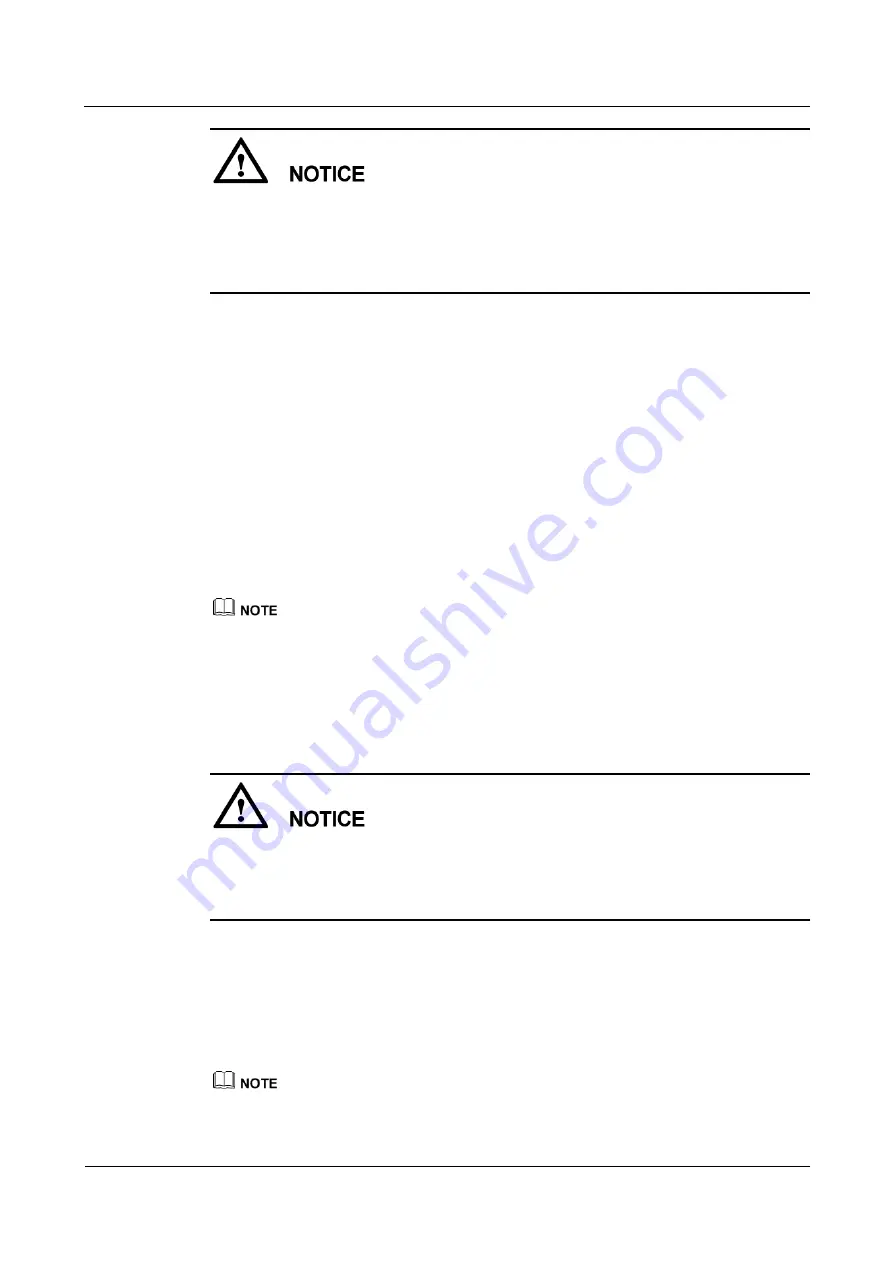
FusionModule1000B Water-Cooled IT Solution
Commissioning Guide
6 Power-On Commissioning
Issue 02 (2017-01-10)
Huawei Proprietary and Confidential
Copyright © Huawei Technologies Co., Ltd.
38
Before the lighting system is powered on, prepare a portable light or open some of the
container doors.
Circuit breakers of various specifications are reserved in the power supply system. If any
of these circuit breakers are used, conduct proper operations on them for the
commissioning.
Preparations
Tools: none
Document required: initial configuration parameter manual
Skill requirement: power distribution system engineer
Procedure
Step 1
Switch on the external input circuit breaker.
Step 2
Power on the FusionModule1000 level by level by referring to the general power-on
commissioning process and power supply and distribution system diagram.
Step 3
Switch on the power supply circuit breaker to power on the equipment.
For equipment with dual power inputs, circuit breakers of both power inputs must be switched on.
Step 4
Verify that the power-on process is normal by referring to
Step 5
(Optional) If initial configurations are involved, verify that the initial parameter values are
correct by referring to the initial configuration parameter manual.
Initial configurations must be verified before the first power-on or restart after a long
power-off period.
Equipment with initial configurations can be powered on only after the initial
configurations are verified.
----End
6.3 Normal Power-On Checking for Components
describes the checking items after components are normally powered-on.
For details about initial configuration parameters in the FusionModule1000, see the initial configuration
parameter manual for the solution in use.