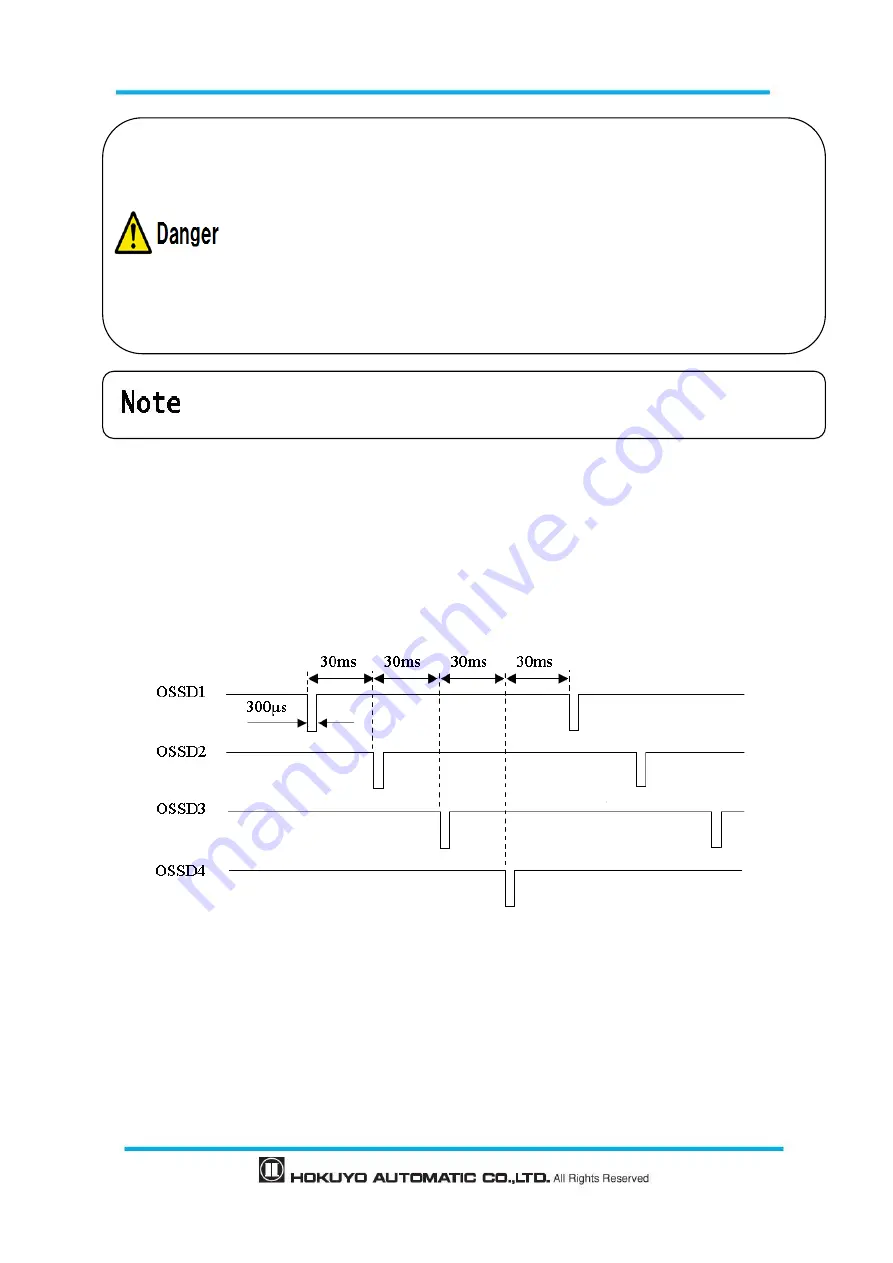
Document No: C-61-00003-3
3.7.1 Self-diagnostic function of OSSD
Self-diagnostic is a function to detect the malfunction in the output circuit by switching OFF the OSSD1
to OSSD4 for an interval of 300
μ
s. Therefore, safety-relay or power converter used must not response to this
diagnostic function. Figure 3-14 below shows the timing chart of the self diagnostic function of the OSSD
during dual protection mode.
Figure 3-14 Timing chart of the OSSD’s self-diagnostic function
In single protection mode, self-diagnostic function is done for OSSD1 and OSSD2 signals only.
3.7.2 Lockout state
When an error is detected by the self-diagnostic function and UAM cannot operate normally it will
switch to lockout state. During the lockout state, OSSD1/2, OSSD3/4, WARNING1, WARNING2 will
switch to OFF-state. After removing the error, UAM can be reset by restoring
the power to release from the
lockout state.
When OSSD is at ON state, the signal is
24V and the signal is 0V during OFF state.
OSSD is a safety related signal and should be connected directly to the relay or
device that switches the machine or vehicle under control.
Sufficient time for the machine or vehicle must be allocated to stop when configuring
the response time of OSSD.
Both the OSSD1 and OSSD2 outputs should be connected to the safety related
machines or control system. If OSSD3 and OSSD4 are used they must be connected
similarly.
User must verify the configuration before actual operation.
Summary of Contents for UAM-05LP
Page 1: ... Document No C 61 00003 3 ...
Page 104: ... Document No C 61 00003 3 Figure 7 33 b Function Figure7 33 c Area ...
Page 107: ... Document No C 61 00003 3 Figure 7 36 a Project report tab Figure 7 36 b Error report tab ...
Page 148: ... Document No C 61 00003 3 13 External dimension 13 1 UAM 05LP ...
Page 149: ... Document No C 61 00003 3 13 2 Base mounting bracket ...
Page 150: ... Document No C 61 00003 3 13 3 Rear mounting bracket ...
Page 151: ... Document No C 61 00003 3 13 4 Cover Protection Bracket ...
Page 152: ... Document No C 61 00003 3 14 EC Declaration of conformity ...
Page 153: ... Document No C 61 00003 3 ...