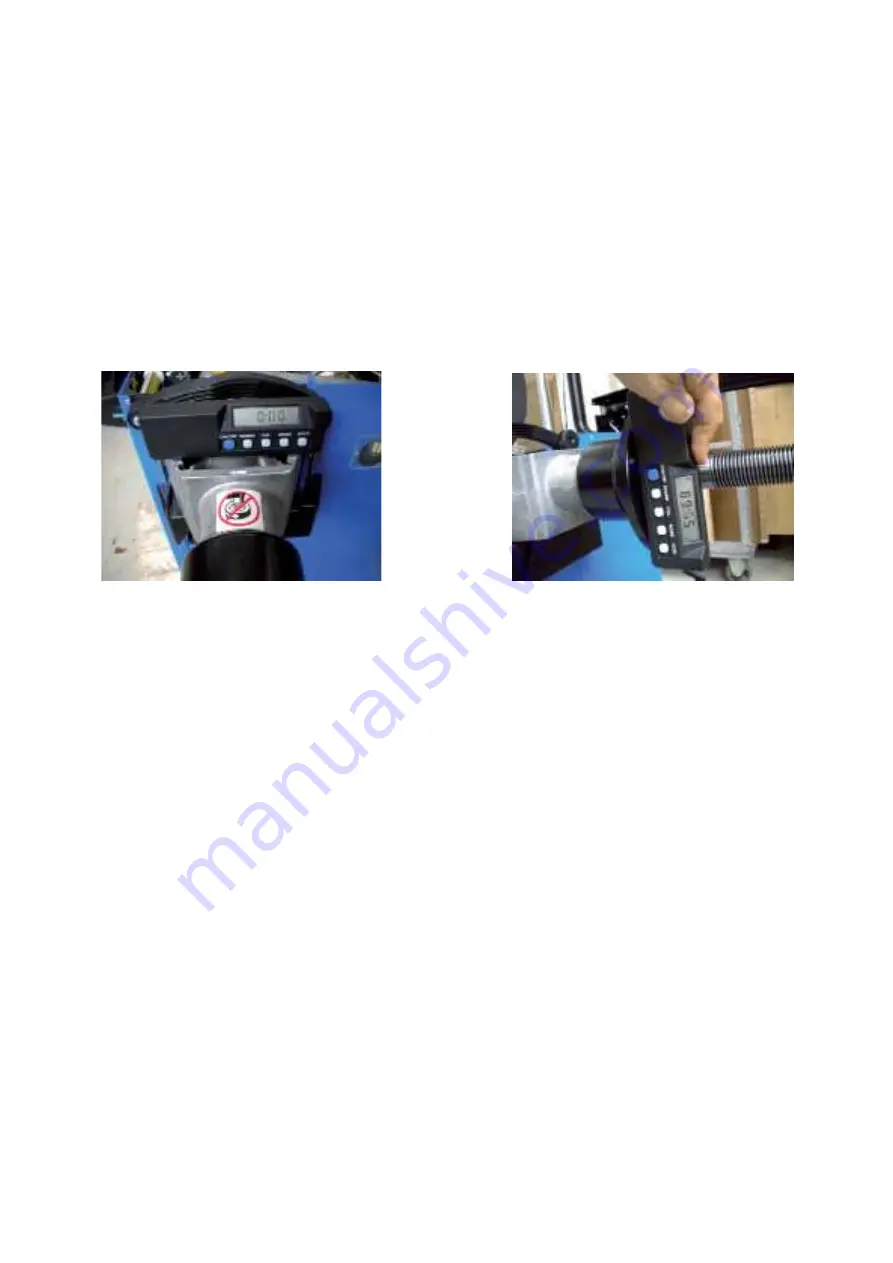
11
wave each time a mark moves past an optocoupler. One additional mark offset from the encoders’ metallic strip, inter-
rupts a third optocoupler on the board, creating a zero-signal reset or home position.
The encoder detects 512 angular positions during each turn of the shaft, plus the home or reset position.
The frequency of the DC square wave generated by the encoder allows the balancer to compute shaft speed, wheel
acceleration and weight location. The encoder and transducer signals are multiplexed by the Processor section of the
IBP box, to give weight amount and location readings.
The Processor section gathers the information generated from the encoder and transducer via a ribbon cable. This
board is powered with 5VDC received from the Power Supply section of the IBP box.
Calculated imbalance values are then shown on the screen after a spin cycle.
2.6 INSTALLATION PRECAUTIONS (Floor Level)
All models of Wheel Balancers have to be placed on a well levelled fl oor (± 1º tolerance). If you have already verifi ed
the fl oor levelling, skip this section, otherwise proceed as explained below.
Remove the weights tray and check the levelling by mean of a spirit level or electronic inclinometer.
1. Put the level on the vibratory system (Fig.1). The value must be 0° ±1º.
2. Put the level vertically on the fl ange (Fig.2). The value must be in the range 90º± 1 °.
Fig.1
Fig.2
SM HOF GEODYNA 7600 Rel.D
Summary of Contents for geodyna 7600
Page 1: ...geodyna 7600 Service Manual ...
Page 118: ...118 SM HOF GEODYNA 7600 Rel D ...