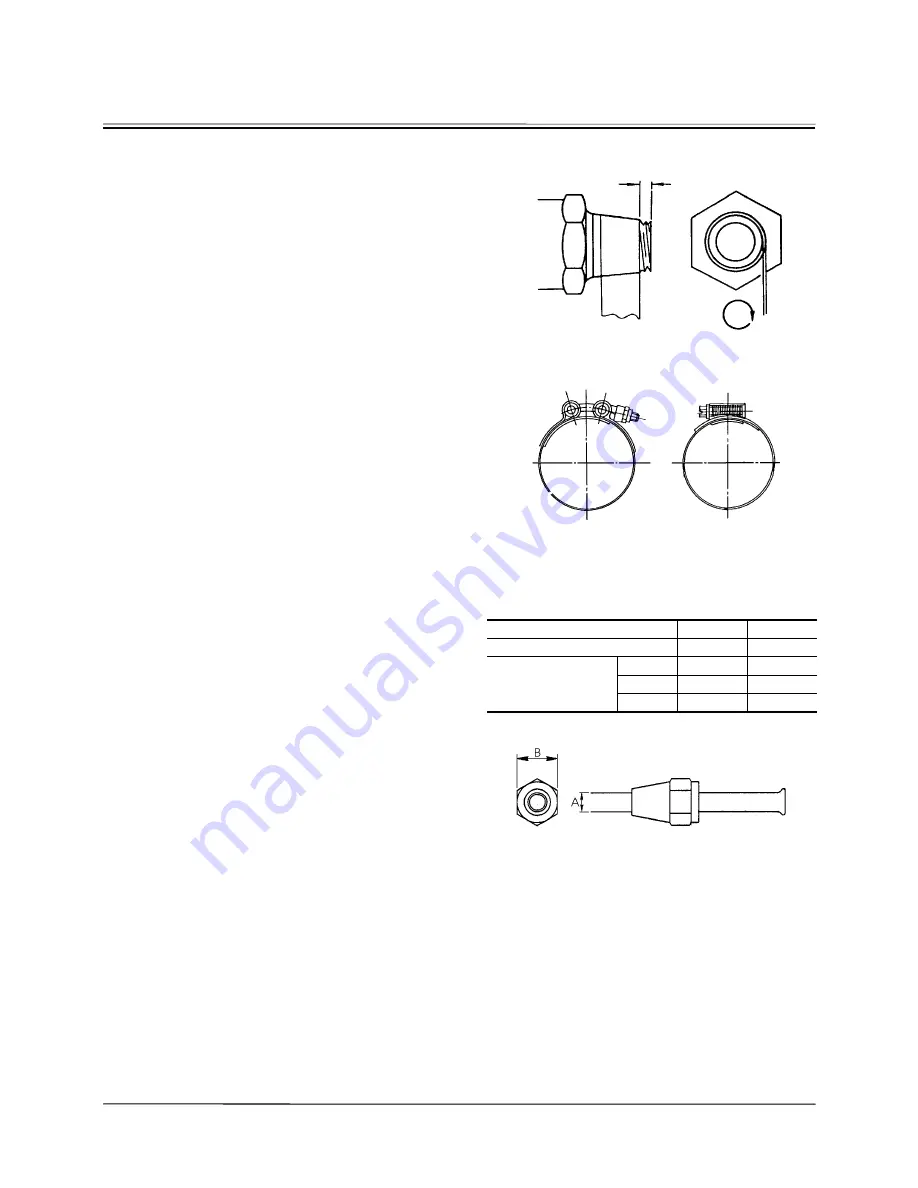
MAINTENANCE
7-53
4. When connecting hydraulic hoses and pipes, take
special care to keep seal surfaces free from dirt and
to avoid damaging them. Keep these precautions in
mind:
4.1 Wash hoses, pipes, and the tank interior with a
washing liquid and thoroughly wipe it out before re-
connecting them.
4.2 Only use O-rings that are free of damage or defects.
Be careful not to damage them during reassembly.
4.3 Do not allow high pressure hoses to twist when
connecting them. The life of twisted hoses will be
shortened considerably.
4.4 Carefully tighten low pressure hose clamps to fol-
lowing torque specifications. Do not overtighten.
T Bolt Clamp: 4.4 N
x
m (0.45 kgf
x
m, 3.3 lbf
x
ft)
Jubilee Clamp: 5.9 to 6.9 N
x
m
(0.6 to 0.7 kgf
x
m, 4.3 to 5.1 lbf
x
ft)
4.5 When connecting screw type joints, apply seal tape
to the threads of male screw. Be sure to leave a
couple of threads at the male screw top unwrapped,
as shown. Do not overwrap. Apply seal tape around
threads as shown, so that the tape does not loosen
when the female screw is tightened.
4.6 Carefully tighten nut for bandy pipe to following
torque specifications on the right side. Do not over-
tighten.
5. When adding hydraulic oil, always use the same
brand of oil; do not mix brands of oil. As the machine
is filled with Super EX 46HN when it is shipped from
the factory, use it as a general rule. When selecting
to use another brand of oil listed in the table “Brand
names of recommended hydraulic oil”, be sure to
completely replace the oil in the system.
6. Do not use hydraulic oils other than those listed in the
table “Brand names of recommended hydraulic oil”.
7. Only 50 to 60% of the total hydraulic circuit oil on a
large size excavator can be replaced at a time. Ac-
cordingly, conduct minimum flushing twice.
8. In case the machine is used for dredging operations,
replace the hydraulic oil at a 2000 hour interval re-
gardless of the oil brand used.
9. If any other hydraulic oil (having a different replace-
ment interval) is unavoidably used, replace the oil in
accordance with the individual replacement interval
standard.
10. Never run the engine without oil in the hydraulic oil
tank.
M114-07-041
M114-07-042 M114-07-043
Bandy Pipe
Pipe Dia. (A)
Φ
8
Φ
10
Width Across Flat (B) (mm)
17
19
N
⋅
m 34 49
(kgf
⋅
m) (3.5)
(5)
Fastening Torque
(lbf
⋅
ft) (25.5) (36)
M117-07-149
Direction of
Tape Winding
A couple of threads left unwrapped
Jubilee Clamp
T Bolt Clamp
Summary of Contents for EX 3600-6
Page 38: ...SAFETY SIGNS S 29 SS3091469 M146 07 080 ...
Page 40: ...SAFETY SIGNS S 31 SS 410 SS 2835 SS3108517 M18G 01 011 ...
Page 41: ...SAFETY SIGNS S 32 SS 413 M146 01 024 M146 01 025 SS4193223 M146 01 025 ...
Page 42: ...SAFETY SIGNS S 33 SS 449 M146 01 027 SS 710 SS 2836 SS 3091472 SS 2837 ...
Page 43: ...SAFETY SIGNS S 34 MEMO ...
Page 89: ...OPERATOR S STATION 1 46 MEMO ...
Page 107: ...OPERATING THE ENGINE 3 16 MEMO ...
Page 119: ...DRIVING THE MACHINE 4 12 MEMO ...
Page 139: ...OPERATING THE MACHINE 5 20 MEMO ...
Page 166: ...MAINTENANCE 7 27 4 Grouped Grease Fittings 4 Arm Ñ Lubrication Points M146 07 085 4 ...
Page 169: ...MAINTENANCE 7 30 4 Grouped Grease Fittings 4 Arm Ñ Lubrication points M18M 07 036 4 ...
Page 283: ...MAINTENANCE 7 144 MEMO ...
Page 285: ...MAINTENANCE UNDER SPECIAL ENVIRONMENTAL CONDITIONS 9 2 MEMO ...
Page 303: ...SPECIFICATIONS 12 4 MEMO ...