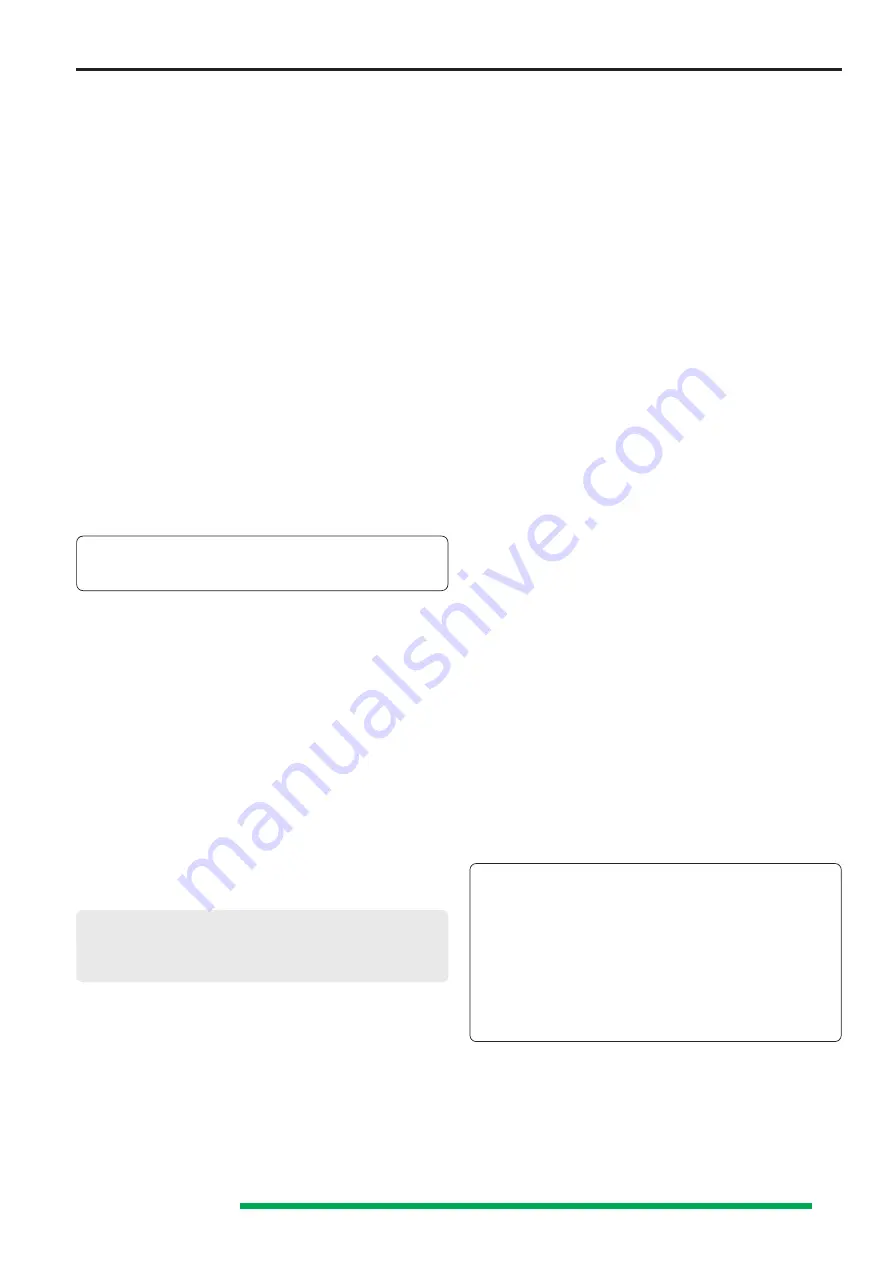
39
Subject to change without notice
Adjustments
As advised in the Operating, Test and Service Instructions,
small corrections and adjustments are easily carried out with
the aid of the “Service Manual”. However, a complete
recalibration of the scope should not be attempted by an
inexperienced operator, but only someone with sufficient
expertise. Several precision measuring instruments with cables
and adapters are required, and only then should the pots and
trimmers be readjusted, provided that the result of each
adjustment can be exactly determined. Thus for each operating
mode and switch position, a signal with the appropriate sine or
square waveform, frequency, amplitude, risetime and duty
cycle is required.
As described in the “Menu” section, the instrument`s software
contains the submenu “CALIBRATE”. The following items can
be used by operators not equipped with precision instruments.
After the required warm-up time of 20 minutes, press and hold
the
MENU
pushbutton until the
MAIN MENU
becomes
visible. Then the submenu
”CALIBRATE”
must be called.
In the
“CALIBRATE”
submenu three items can be chosen:
1: Y AMP (amplifier channel I and II)
2: TRIGGER AMP (trigger amplifier channel I and II)
3: STORE AMP (digital section)
Attention!
During the automatic adjustment procedure no signal
may be applied on any input.
Each item is called by pressing and holding the SAVE pushbutton.
Then the instrument automatically adjusts and stores the
adjustment values. In case of the Y amplifiers these are the field
effect transistor‘s operating points, the invert and the variable
gain balance. For the trigger amplifier it is regarding the DC
operating points and the trigger threshold. In storage mode the
adaptation of the storage display to the analog display.
The new adjustment values are always present after the
instrument is switched on. Therefore it is not required to
overwrite the factory adjustments by calling the
OVERWRITE
FACTORY DEFAULT
function in the
FACTORY
submenu.
Note! The automatic adjustment should only be made if the
instrument‘s warm up time has passed and no faults such as
incorrect operating voltages are present. During some automatic
adjustment procedures the readout indicates “Working”.
RS232 Interface - Remote Control
Safety
Caution:
All terminals of the RS232 interface are galvanically
connected with the oscilloscope and subsequently with
protective (safety) earth potential.
Measurement on a high level reference potential is not
permitted and endangers operator, oscilloscope, interface and
peripheral devices.
In case of disregard of the safety warnings contained in this
manual,
HAMEG
refuses any liability regarding personal injury
and/or damage of equipment.
Operation
The oscilloscope is supplied with a serial interface for control
purposes. The interface connector (9 pole D- SUB female) is
located on the rear of the instrument. Via this bi-directional
port, the instrument parameter settings and (in storage mode)
signal data, can be transmitted to, or received from a PC.
RS-232 Cable
The maximum connecting cable length must not exceed 3
meters and must contain 9 lines connected 1:1. The oscilloscope
RS232 connection (9 pole D-SUB female) is determined as
follows:
Pin
2
Tx data (data from oscilloscope to external device)
3
Rx data (data from external device to oscilloscope)
7
CTS (clear to send)
8
RTS (request to send)
5
Ground (reference potential - connected via the
oscilloscope’s power cord with protective earth)
9
+5V supply voltage for external devices (max. 400mA)
The maximum voltage swing at pin 2, 3, 7 and 8 is ± 12
Volt.
RS-232 protocol
N-8-2 (no parity bit, 8 data bits, 2 stop bits, RTS/CTS hardware
protocol).
Baud-Rate Setting
After the first
POWER UP
(switching on of the oscilloscope )
and the first command
SPACE CR
(20hex, 0Dhex) sent from
the PC, the baud rate is recognized and set automatically
between 110 baud and 19200 baud. The oscilloscope is then
switched over to REMOTE control mode. The oscilloscope
then transmits the RETURNCODE: 0 CR LF to the PC. In this
status all settings (with the exception of those functions
mentioned under “Controls and readout”) can be controlled
via the interface only.
The only ways to quit this status are:
• Switching the oscilloscope off, transmitting the command
• RM= 0 from the PC to the oscilloscope, or
• depressing the AUTO SET ( LOCAL ) pushbutton,
if in unlocked condition (command LK=1... was not sent)
After the remote state has been switched off the
RM -LED (3)
is dark.
Please note:
A minimum time must elapse between the commands
RM=1... (remote on) and RM=0... (remote off) and vice
versa. The time can be calculated with the formula:
t
min
= 2/baud rate + 60µs.
If at the beginning no SPACE CR command is recog-
nizable, the oscilloscope pulls the TxD line low for approx.
0.2ms and causes a break on the PC.
Data Communication
After successfully being set to remote control mode, the
oscilloscope is prepared for command reception.
A disk with programming examples and a list of the instrument
commands is supplied with the oscilloscope.
RS232 Interface - Remote Control