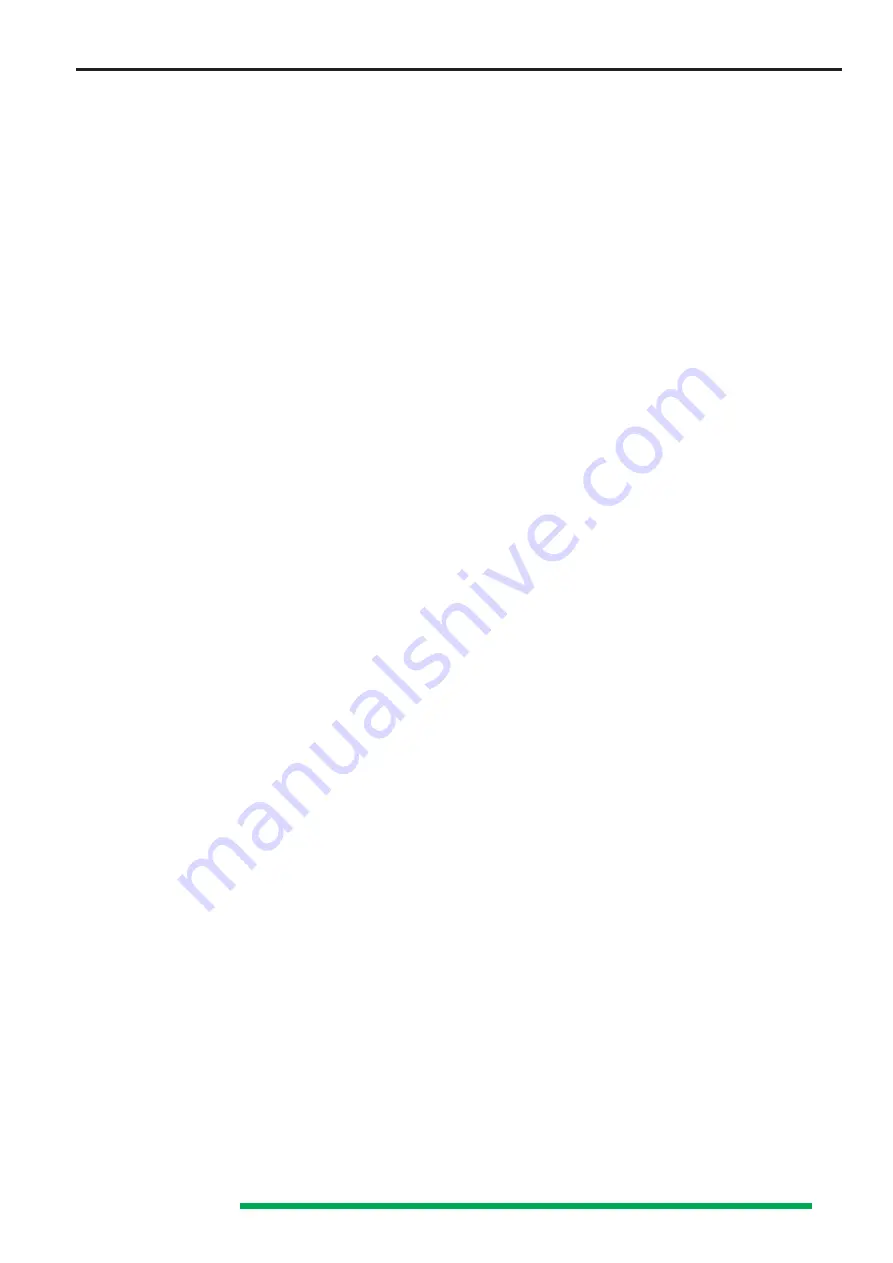
37
Subject to change without notice
The checks should show the same trigger threshold with the
same frequency. On changing the trigger slope, the start of
the sweep changes from the positive-going to the negative-
going edge of the trigger signal.
As described in the Operating Instructions, the trigger frequency
range is dependent on the trigger coupling selected. For lower
frequencies the LF coupling mode can be selected. In this
mode, triggering up to at least 1.5kHz (sine-wave) is possible.
Internally the instrument should trigger perfectly at a display
height of approx. 0.5div, when the appropriate trigger coupling
mode is set.
For external triggering, the external trigger input connector
requires a signal voltage of at least 0.3Vpp, which is in
synchronism with the Y input signal. The voltage value is
dependent on the frequency and the trigger coupling mode
(
AC-DC-HF-LF
).
Checking of the TV triggering is possible with a video signal of
any given polarity.
Use the
TV-L
or
TV-F
setting for video sync pulse separation.
The correct slope of the sync pulse (front edge) must be
selected and a suitable time coefficient setting must be
chosen. The slope is then valid for both sync frequencies.
Perfect TV triggering is achieved, when in both display modes
the amplitude of the complete TV signal (from white level to
the top of the line sync pulse) is limited between 0.8 and 6div
and sync pulses of more then 0.5 div height. The display should
not shift horizontally during a change of the trigger coupling
from AC to DC when displaying a sine-wave signal without DC
offset.
If both vertical inputs are
AC
coupled to the same signal and
both traces are brought to coincide exactly on the screen,
when working in the alternate dual channel mode, then no
change in display should be noticeable, when switching from
TRIG CH I
to
TRIG CH II
or when the trigger coupling is
changed from AC to DC.
Checking of the line/mains frequency triggering (50 - 60Hz) is
possible, when the input signal is time-related (multiple or
submultiple) to the power line frequency (
~ LED
lights). There
is no trigger threshold visible in this trigger mode. Even very
small input signals are triggered stably (e.g. ripple voltage). For
this check, use an input of approx. 1V. The displayed signal
height can then be varied by turning the respective input
attenuator switch and its variable control.
Time base
Before checking the time base it should be ascertained that
the trace length is approx. 10div in all time ranges. The
X-
MAG. x10 LED
should not light. This condition should be
maintained until the variation ranges of these controls are
checked. Check that the sweep runs from the left to the right
side of the screen (
TIME/DIV.
setting to 100ms/div). This
check is only necessary after changing the cathode-ray tube.
If a precise marker signal is not available for checking the Time
base time coefficients, then an accurate sine-wave generator
may be used. Its frequency tolerance should not be greater
than ±0.1%. The time base accuracy of the instrument is given
as ±3%, but it is considerably better than this. For the
simultaneous checking of time base linearity and accuracy at
least 10 oscillations, i.e. 1 cycle every div, should always be
displayed. For precise determination, set the peak of the first
marker or cycle peak exactly behind the first vertical graticule
line using the
X-POS.
control. Deviation tendencies can be
noted after some of the marker or cycle peaks. If a precise
Time Mark Generator is used for checking, Normal Triggering
and
LEVEL
control adjustment is recommended.
The signal frequency required for each time coefficient setting
can be determined easily by the aid of the readout. In time
measurement condition the distance of the vertical cursor
lines must be set to exactly 1 div. Then both readout information
regarding the time deflection coefficient and the time difference
show exactly the same value. After switching over from time
to frequency measurement, the readout displays the required
signal frequency in each time base setting.
Hold Off time (analog mode only)
The variation of the hold off time setting can not be measured
without opening the instrument. However, a visual check can
be made if the instrument is operated in undelayed time base
mode. Without an input signal, set time base to 50ns/div, use
automatic peak (value) triggering. With minimum hold off time
the trace should be bright. It should noticeably darken if the
hold off time is increased to the maximum.
Component Tester
After selecting component tester mode, a horizontal straight
line should appear immediately, when the test leads are not
connected (open circuit). The length of this trace should be
approx. 8div. With the test leads shorted together, a vertical
straight line with approx. 6div height should be displayed. The
above stated measurements have some tolerances.
Trace Alignment
The CRT has an admissible angular deviation ±5° between the
X deflection plane D1-D2 and the horizontal center line of the
internal graticule. This deviation, due to tube production
tolerances (and only important after changing the CRT), and
also the influence of the earth’s magnetic field, which is
dependent on the instruments North orientation, are corrected
by means of the TR potentiometer. In general, the trace
rotation range is asymmetric. It should be checked, whether
the baseline can be adjusted somewhat sloping to both sides
round about the horizontal center line of the graticule. With the
instrument in its closed case, an angle of rotation ±0.57°
(0.1div difference in elevation per 10div graticule length) is
sufficient for the compensation of the earth’s magnetic field.
Service Instructions
General
The following instructions are intended as an aid for the
electronic technician, who is carrying out readjustments on
the instrument, if the nominal values do not meet the
specifications. These instructions primarily refer to those
faults, which were found after using the Test Instructions.
However, this work should only be carried out by properly
qualified personnel.
For any further technical information
call or write to HAMEG
. Addresses are provided at the back
of the manual. It is recommended to use only the original
packing material, should the instrument be shipped to for
service or repair (see also Warranty).
Instrument Case Removal
The rear cover can be taken off after unplugging the power
cords triple-contact connector and after two nuts have been
removed. If a cross recessed pan head screw is present on the
bottom of the instrument, it must be removed too. While the
instrument case is firmly held, the entire chassis with its front
Service Instructions