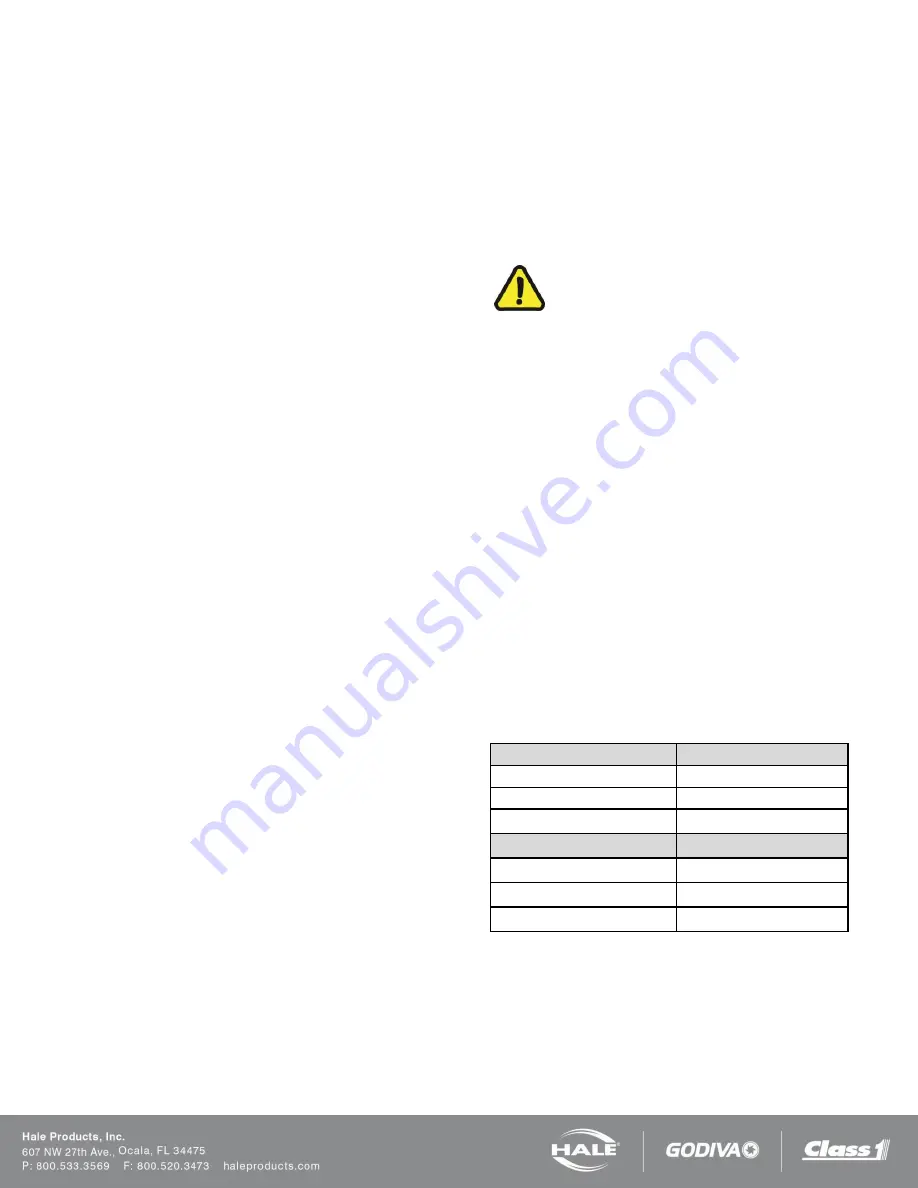
Page
33
SmartFOAM
To be NFPA compliant, when flushing is required, the
system installer must provide proper:
❑
Hoses
❑
Shut-off valves
❑
Check valves
❑
Reducer/regulator
❑
Connections for flushing water for the system
FOAM DISCHARGE DRAINS
Drains must be provided from foam capable discharge
piping components to prevent freezing in cold weather.
When designing the drain system care must be taken to
prevent contamination of the water system with foam and
the foam concentrate with water. Some multiple drain
systems that allow individual drain lines to communicate
also allow foam to bypass the installed check valves
causing contamination of fire pump and the water or foam
concentrate storage tanks.
Hale offers an optional manual or air-operated 6-port drain
valve, Class1 Model MMD6 (p/n: 104961). The valve
provides individual drains with a single control and is use
for applications where a single point for multiple drains is
required. If a Hale MMD6 drain valve is not used,
individual drain lines and valves for foam capable
discharge piping is recommended.
APPARATUS DESIGN/BUILD FOR COLD
WEATHER (BELOW FREEZING) DUTY
If the end-user will use the fire apparatus in sub- freezing
temperatures, the onus is on the fire truck builder to build
into the apparatus design an appropriate ambient
temperature operating environment for the envelope
where the SmartFOAM system will be located. This
routinely takes on the form and function of mounting the
SmartFOAM system in a limited ventilation area that is
served by an appropriate pump house auxiliary heater.
Simply, the fire truck builder must keep ambient air
temperature above 32°F (0°C) in the envelope around the
SmartFOAM hardware, including the base foam pump
unit, foam strainer, foam concentrate injection line, etc.
There are several best practices in the fire industry that
can be employed to meet this criteria and the fire truck
builder/designer can choose the best choice for their
specific installation. Note that there must be ventilation
available to cool the area around the unit also, to prevent
electric motor overheating when the unit is operating in
high temperature ambient environments.
ELECTRICAL REQUIREMENTS
The system installer must provide the primary power wire
and a ground strap for the Hale SmartFOAM system.
Primary power must be supplied from the main apparatus
battery to the motor controller box on the foam pump and
motor assembly. The Hale SmartFOAM 2.1A and 1.7AHP
systems require a minimum of a 40 AMP electrical service.
The Hale SmartFOAM 3.3 and 5.0 systems require a
minimum of a 60 AMP electrical service. The Hale
SmartFOAM 6.5 system requires a minimum of a 80 AMP
electrical service
Primary electrical power must be supplied directly from the
battery, the battery master disconnect switch, or solenoids to
the Hale SmartFOAM system.
IMPORTANT!
OTHER ELECTRICAL COMPONENTS MUST NOT BE
SUPPLIED FROM THIS WIRE. DO NOT CONNECT THE
PRIMER AND HALE SMARTFOAM TO THE SAME
POWER WIRE.
The primary power connection must be made so that power
is supplied to the Hale SmartFOAM when the main
apparatus electrical system is energized and the pump is in
gear. Use of a solenoid with a 150 AMP peak, 85 AMP
continuous rating is recommended. Figure 11
Recommended Relay Wiring Schematic
recommended wiring for this relay.
Note:
This ensures immediate operation when the operator
places the apparatus in PUMP mode, and to prevent battery
power drain when the apparatus is not running.
Make certain that the recommended wire gage is selected
for the primary power connection based on the run length
(see Table 5
: Recommended Primary Power Cable
). Use solder lugs on cable ends with a
5/16” (8mm)
diameter hole.
Models 1.7 and 2.1
Maximum length
8 AWG (8.4mm
2
)
6 ft (1.8M) or less
4 AWG (21.2mm
2
)
6 ft (1.8M) to 15 ft (4.6M)
0 AWG (53.5mm
2
)
15 ft (4.8M) or Longer
Models 3.3, 5.0, 6.5
Maximum length
4 AWG (21.2mm
2
)
6 ft (1.8M) or less
0 AWG (53.5mm
2
)
6 ft (1.8M) to 15 ft (4.6M)
00 AWG (67.5mm
2
)
15 ft (4.8M) or Longer
Table 5
: Recommended Primary Power Cable Sizes
Summary of Contents for SmartFOAM 1.7AHP
Page 3: ...Page 2 SmartFOAM NOTES...
Page 14: ...Page 13 SmartFOAM Figure 2 3 3 and 5 0 Foam Pump Installation Envelope Dimensions...
Page 15: ...Page 14 SmartFOAM SYSTEM DIAGRAM Figure 3 Typical Hale SmartFOAM 2 1A and 1 7AHP System...
Page 16: ...Page 15 SmartFOAM Figure 4 SmartFOAM 3 3 5 0 6 5 Single Tank System with In line Strainer...
Page 17: ...Page 16 SmartFOAM Figure 5 SmartFOAM 3 3 5 0 6 5 Single Tank withMSTandIn lineStrainer...
Page 18: ...Page 17 SmartFOAM Figure 6 SmartFOAM 3 3 5 0 6 5 Single Tank withMSTandFSSeriesStrainer...
Page 19: ...Page 18 SmartFOAM Figure 7 SmartFOAM 3 3 5 0 6 5 Dual Tank withMDTIIandIn lineStrainer...
Page 20: ...Page 19 SmartFOAM Figure 8 SmartFOAM 3 3 5 0 6 5 Dual Tank withMDTIIandFSSeriesStrainer...
Page 21: ...Page 20 SmartFOAM Figure 9 SmartFOAM 3 3 5 0 6 5 Dual Tank with ADTandIn lineStrainer...
Page 22: ...Page 21 SmartFOAM Figure 10 SmartFOAM 3 3 5 0 6 5 Dual Tank with ADTandFSSeriesStrainer...
Page 40: ...Page 39 SmartFOAM Figure 18 Typical 4 Inch Check Valve Installation Midship Pump...
Page 51: ...Page 50 SmartFOAM Figure 33 ADT Option Air Hose Connections Part 2...
Page 68: ...Page 67 SmartFOAM NOTES...
Page 80: ...79 Page 79 SmartFOAM NOTES...