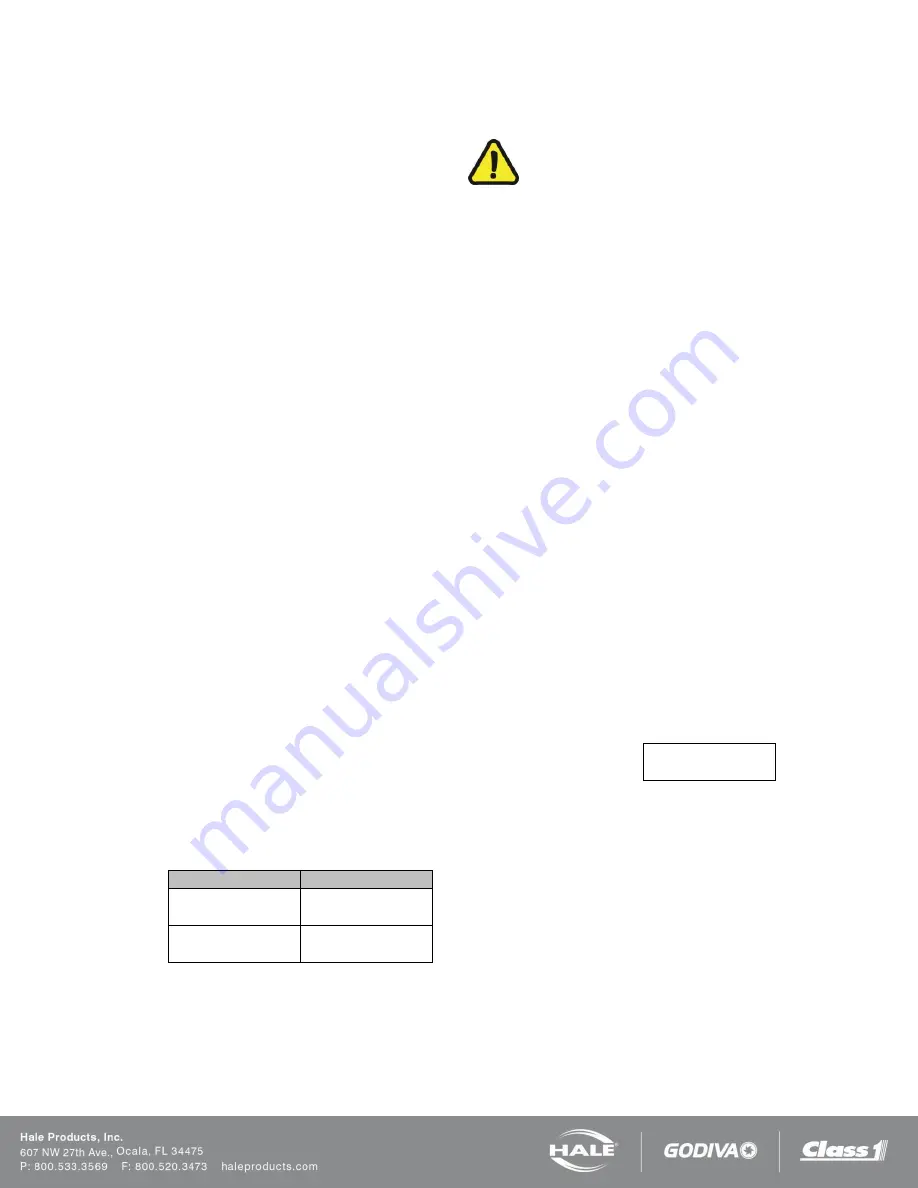
69
Page
69
SmartFOAM
Enter the password “6679”. The controller will show the
water flow calibration screen.
Water flow calibration requires setting two calibration
points: one at a high rate of flow and the second at a
lower rate of flow. These flow points are arbitrary and
can be selected at any two points within the operation
range of the discharge.
1. Determine the desired high rate water flow
normally expected from the discharge outlet and
establish flow.
a. Make sure the water flow established is
within the range of the flow sensor
monitoring the discharge.
For example, establish a flow rate of 150
GPM (568 LPM) of water through a
nozzle and Pitot system. Compare the
calculated flow value to the value shown
on the control unit display.
2. Press the INCR/DECR buttons to set the
displayed high flow value to match the actual
flow through the discharge.
3. Press the SET button to associate the water flow
sensor’s (paddlewheel) pulse rate with the high
flow value.
4. Determine the desired low rate water flow
normally expected from the discharge outlet and
establish flow.
5. Press the INCR/DECR buttons to set the
displayed low flow value to match the actual flow
through the discharge.
6. Press the SET button to associate the water flow
sensor’s (paddlewheel) pulse rate with the low
flow value.
7. Press the SAVE button to save the flow values
into non-volatile memory.
Record the calibrated values in the section below.
These values can be entered manually if the controller
unit ever needs to be replaced.
Flow Rate
Flow Pulses
High rate cal
Low rate cal
FOAM FLOW CALIBRATION
IMPORTANT!
FOAM PUMP FEEDBACK IS CALIBRATED AFTER
INSTALLATION TO VERIFY VALUES WITH THE ACTUAL
FOAM CONCENTRATE BEING USED. ONLY CALIBRATE
USING ACTUAL FOAM CONCENTRATES.
DO NOT USE WATER, TRAINING OR TEST FOAMS FOR
FEEDBACK CALIBRATION VERIFICATION.
Enter the pas
sword “1560”. The controller will show the foam
flow calibration screen.
1.
Set the bypass valve’s handle to
BYPASS
.
2. Place a graduated measure container at the outlet of the
bypass hose capable of containing the expected volume
of foam concentrate: 5 gallons (19 liters) minimum.
3. Start the Hale SmartFOAM foam pump by pressing the
ON/OFF button.
4. Watch the level of foam in the graduated measure
container and stop the foam pump when at the desired
level by pressing the ON/OFF button again.
5. Adjust the reading on the display to match the actual
volume by using the INCR and DECR arrow buttons.
6. Press the SAVE button.
7. Repeat the procedure to verify that the setting is correct.
a. Press the SAVE button again if the value was
modified.
8.
Set the bypass valve’s handle back to
INJECT
.
Record the calibrated values in the section below.
Foam factor
Summary of Contents for SmartFOAM 1.7AHP
Page 3: ...Page 2 SmartFOAM NOTES...
Page 14: ...Page 13 SmartFOAM Figure 2 3 3 and 5 0 Foam Pump Installation Envelope Dimensions...
Page 15: ...Page 14 SmartFOAM SYSTEM DIAGRAM Figure 3 Typical Hale SmartFOAM 2 1A and 1 7AHP System...
Page 16: ...Page 15 SmartFOAM Figure 4 SmartFOAM 3 3 5 0 6 5 Single Tank System with In line Strainer...
Page 17: ...Page 16 SmartFOAM Figure 5 SmartFOAM 3 3 5 0 6 5 Single Tank withMSTandIn lineStrainer...
Page 18: ...Page 17 SmartFOAM Figure 6 SmartFOAM 3 3 5 0 6 5 Single Tank withMSTandFSSeriesStrainer...
Page 19: ...Page 18 SmartFOAM Figure 7 SmartFOAM 3 3 5 0 6 5 Dual Tank withMDTIIandIn lineStrainer...
Page 20: ...Page 19 SmartFOAM Figure 8 SmartFOAM 3 3 5 0 6 5 Dual Tank withMDTIIandFSSeriesStrainer...
Page 21: ...Page 20 SmartFOAM Figure 9 SmartFOAM 3 3 5 0 6 5 Dual Tank with ADTandIn lineStrainer...
Page 22: ...Page 21 SmartFOAM Figure 10 SmartFOAM 3 3 5 0 6 5 Dual Tank with ADTandFSSeriesStrainer...
Page 40: ...Page 39 SmartFOAM Figure 18 Typical 4 Inch Check Valve Installation Midship Pump...
Page 51: ...Page 50 SmartFOAM Figure 33 ADT Option Air Hose Connections Part 2...
Page 68: ...Page 67 SmartFOAM NOTES...
Page 80: ...79 Page 79 SmartFOAM NOTES...