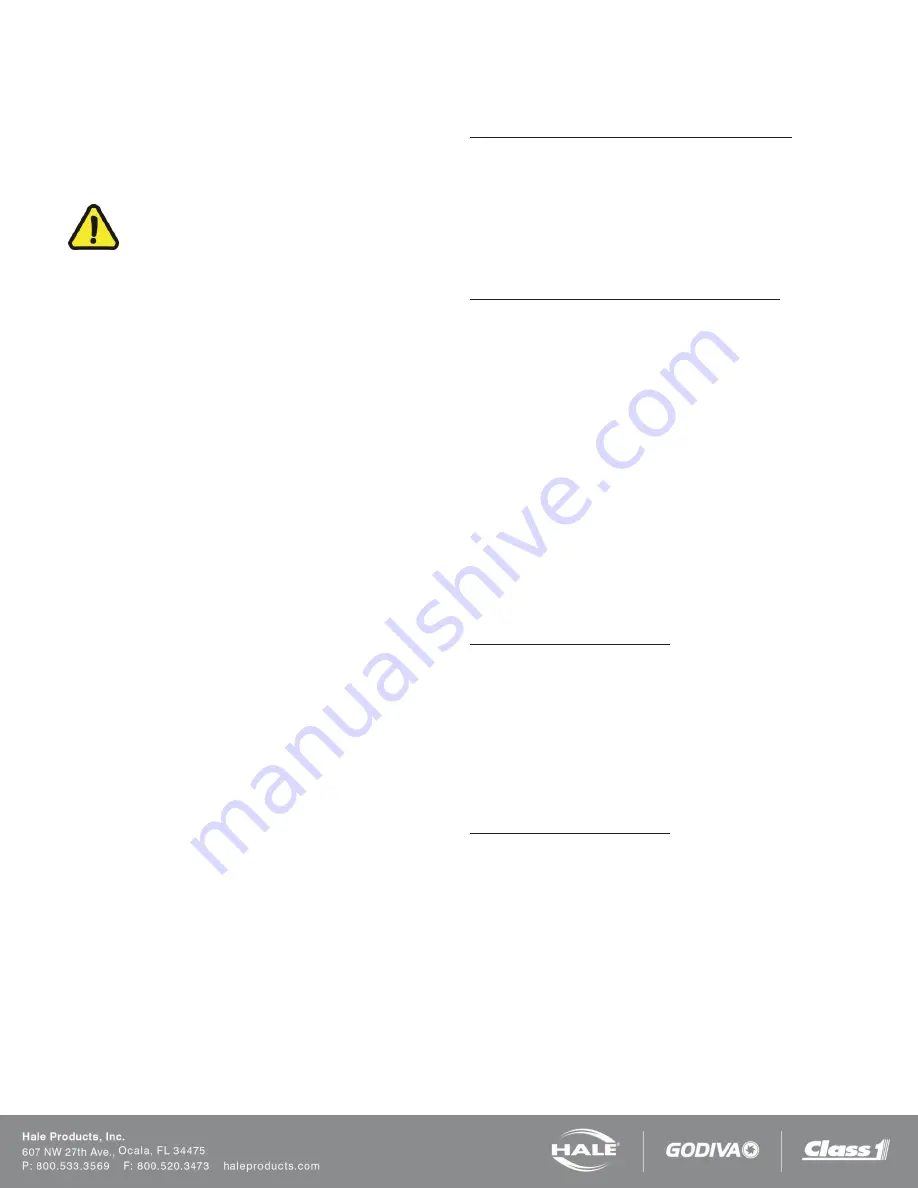
Page
31
SmartFOAM
If panel mounted FS series strainers are installed, mount
the strainer in the foam concentrate hose that supplies
concentrate to the ADT, MDT II or MST. The FS series
strainer may also be mounted in the outlet hose of the
MDT II or MST.
IMPORTANT!
WHEN DETERMINING THE STRAINER LOCATION
KEEP IN MIND THE REQUIREMENT FOR GRAVITY
FEED OF FOAM CONCENTRATE TO THE FOAM PUMP
THROUGH THE STRAINER AND AVOID AIR TRAPS IN
THE HOSES. ALSO, CLEARANCE MUST BE
PROVIDED TO ALLOW REMOVAL OF THE BOWL
ASSEMBLY TO CLEAN THE STAINLESS STEEL
MESH, TO MAKE HOSE CONNECTIONS TO THE
STRAINER AND FOR OPERATION OF THE SERVICE
VALVE.
The installer must provide a strainer service isolation valve
in the foam concentrate hose to prevent spillage during
service. An MST or MDT II can serve this purpose.
CONTROL UNIT AND INSTRUCTION /
SYSTEM DIAGRAM PLACARD
Determine a location on the operator panel of the
apparatus for the control unit and instruction/ system
diagram placard, if provided. These components must be
located at the main pump operator position in close
proximity to each other. Consideration must be given for
routing the control cable from the control unit to the motor
controller on the foam pump and motor assembly. If
necessary, order longer or shorter cable assemblies to suit
the location demands.
INSTALLER SUPPLIED COMPONENTS
Due to the many differences in apparatus configurations
and design requirements the Hale SmartFOAM system
installer must supply components such as:
❑
Mounting brackets
❑
Piping
❑
Hoses
❑
Fittings
❑
Electrical wiring
❑
Foam tank(s)
The following guidelines are recommendations for
selection of additional components for a complete system
installation. These recommendations reflect materials and
components that are tested extensively with Hale
SmartFOAM systems and provide proven reliable
performance.
FOAM CONCENTRATE SUCTION HOSE
SmartFOAM 2.1A and 1.7 AHP Foam systems
These systems are provided with
15’ (4.6 meters) of 1/2”
(13mm) ID reinforced PVC foam concentrate suction hose.
The system installer may need to supply additional fittings
and hose from the foam tank to the inlet of the foam pump.
All components selected transfer foam concentrate;
therefore they must be compatible with the foam
concentrates being used in the system.
SmartFOAM 3.3, 5.0, and 6.5 Foam systems
Hoses for Class “A” foam concentrates have minimum 3/4”
(19mm) inside diameter.
Hoses for Class “B” foam
concentrates must have a minimum 1” (25.4mm) inside
diameter due to higher viscosity of the concentrate.
Note
: Certain types of Class “B” AFFF-ARC or ATC
concentrates require a 1-
1/4” or 1-1/2” (32mm or 38mm) ID
foam concentrate supply line.
Hoses for the foam concentrate suction that are not subject
to high pressure, i.e. flushing water or foam concentrate
dis
charge, must have a rating of 23” (584.2mm) Hg vacuum
and 50 PSI (3.5 BAR) pressure or greater.
Note:
NFPA requires that foam concentrate suction hose be
clear to observe foam concentrate flow during foam pump
operation.
Recommended components
Hose:
PVC, Kuriyama Kuri-Tec K3130 or K7130 series.
Fittings:
Hose Barb Type; Brass, Stainless Steel or Nylon.
Foam concentrate suction hose subjected to flushing water
pressure must be rated for 23 in (584.2mm) Hg vacuum and
the maximum discharge pressure of the fire pump (500 PSI
[34 BAR] minimum). These hoses include the hose from the
outlet of the MDT II or MST to the foam pump inlet.
Recommended components
Hose:
Aeroquip 2580 series or Equivalent Reinforced
Hydraulic Hose.
Fittings:
Brass or Stainless Steel Hose End Crimp or
Reusable Type (Aeroquip 412 series or
Equivalent).
A foam tank shut-off valve and drain valve should be
provided in the foam tank suction hose to allow strainer
service, tank drainage and easier priming.
These components are subject to the same material
characteristics and pressure ratings as stated above. When
the In-line strainer/valve assembly option is installed the
shut-off valve is included. A separate valve is not required.
Summary of Contents for SmartFOAM 1.7AHP
Page 3: ...Page 2 SmartFOAM NOTES...
Page 14: ...Page 13 SmartFOAM Figure 2 3 3 and 5 0 Foam Pump Installation Envelope Dimensions...
Page 15: ...Page 14 SmartFOAM SYSTEM DIAGRAM Figure 3 Typical Hale SmartFOAM 2 1A and 1 7AHP System...
Page 16: ...Page 15 SmartFOAM Figure 4 SmartFOAM 3 3 5 0 6 5 Single Tank System with In line Strainer...
Page 17: ...Page 16 SmartFOAM Figure 5 SmartFOAM 3 3 5 0 6 5 Single Tank withMSTandIn lineStrainer...
Page 18: ...Page 17 SmartFOAM Figure 6 SmartFOAM 3 3 5 0 6 5 Single Tank withMSTandFSSeriesStrainer...
Page 19: ...Page 18 SmartFOAM Figure 7 SmartFOAM 3 3 5 0 6 5 Dual Tank withMDTIIandIn lineStrainer...
Page 20: ...Page 19 SmartFOAM Figure 8 SmartFOAM 3 3 5 0 6 5 Dual Tank withMDTIIandFSSeriesStrainer...
Page 21: ...Page 20 SmartFOAM Figure 9 SmartFOAM 3 3 5 0 6 5 Dual Tank with ADTandIn lineStrainer...
Page 22: ...Page 21 SmartFOAM Figure 10 SmartFOAM 3 3 5 0 6 5 Dual Tank with ADTandFSSeriesStrainer...
Page 40: ...Page 39 SmartFOAM Figure 18 Typical 4 Inch Check Valve Installation Midship Pump...
Page 51: ...Page 50 SmartFOAM Figure 33 ADT Option Air Hose Connections Part 2...
Page 68: ...Page 67 SmartFOAM NOTES...
Page 80: ...79 Page 79 SmartFOAM NOTES...