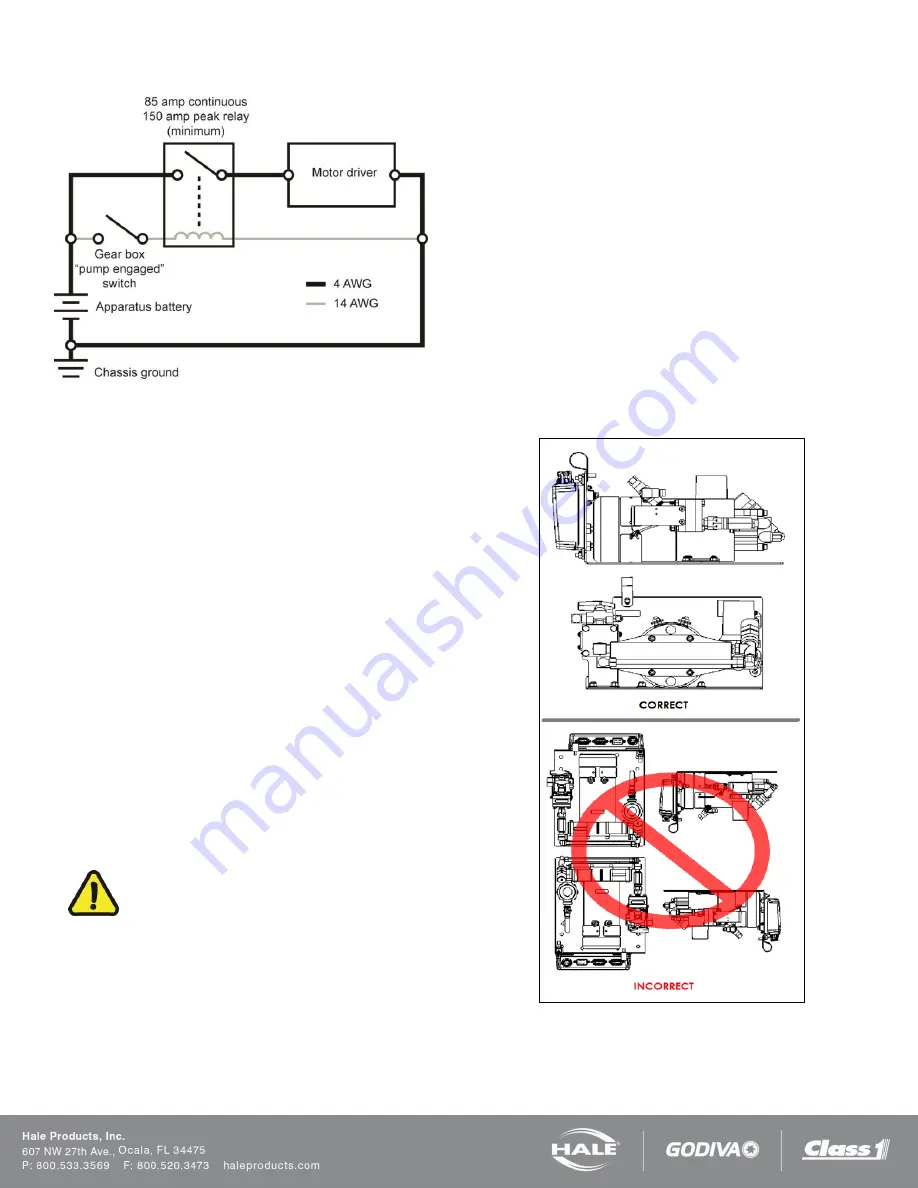
Page
34
SmartFOAM
Figure 11
: Recommended Relay Wiring Schematic
When planning cable runs make sure the primary wires
are routed by the shortest most direct route.
A braided flat ground strap connected to the apparatus
chassis is recommended for the ground connection.
This limits the RFI/EMI interference encountered with
radios, computers or other sensitive electronic equipment.
The ground strap should be a minimum of 1-
1/4” (32mm)
wide and no longer than 18” (457mm). It must have
soldered flat lug ends with 3/8” (10mm) diameter holes. If
the ground strap length exceeds 18” (457mm), a wider
ground strap should be used or use a double thickness of
1-
1/4” (32mm) wide ground strap. The ground strap must
be connected to the chassis. U
se minimum 5/16” (8 mm)
diameter bolt or mounting to secure the strap.
Power and ground must also be provided for the display
unit using the 2 pin Packard connector. The power must
be a minimum 5 amp dedicated and fused circuit. The
ground must be connected to the chassis ground stud and
protected from corrosion. Make sure the ground is
attached directly to the chassis frame and not to the
apparatus body work.
IMPORTANT!
BEFORE MAKING GROUND CONNECTIONS REMOVE
ALL PAINT, GREASE AND COATINGS FROM THE
CONNECTION AREA. AFTER MAKING CONNECTION,
SEAL AGAINST CORROSION. WHEN A FLAT GROUND
STRAP IS NOT AVAILABLE USE A BATTERY CABLE
ONE SIZE LARGER THAN THE POWER CABLE USED.
FOAM CONCENTRATE TANK
A foam concentrate tank must be supplied to suit the
capacity required for the apparatus application. The tank
must meet NFPA minimum standards for its design capacity,
including:
❑
Filler size
❑
Vapor pressure venting
❑
Baffling
❑
Drain facilities
FOAM PUMP MOUNTING
Position the foam pump and motor assembly in the desired
location on the apparatus. When installing the foam pump
and motor assembly, the assembly should be kept in a
HORIZONTAL position with the base plate on the bottom
(See Figure 12
: SmartFOAM Piston Pump Installation
Figure 12
: SmartFOAM Piston Pump Installation
Summary of Contents for SmartFOAM 1.7AHP
Page 3: ...Page 2 SmartFOAM NOTES...
Page 14: ...Page 13 SmartFOAM Figure 2 3 3 and 5 0 Foam Pump Installation Envelope Dimensions...
Page 15: ...Page 14 SmartFOAM SYSTEM DIAGRAM Figure 3 Typical Hale SmartFOAM 2 1A and 1 7AHP System...
Page 16: ...Page 15 SmartFOAM Figure 4 SmartFOAM 3 3 5 0 6 5 Single Tank System with In line Strainer...
Page 17: ...Page 16 SmartFOAM Figure 5 SmartFOAM 3 3 5 0 6 5 Single Tank withMSTandIn lineStrainer...
Page 18: ...Page 17 SmartFOAM Figure 6 SmartFOAM 3 3 5 0 6 5 Single Tank withMSTandFSSeriesStrainer...
Page 19: ...Page 18 SmartFOAM Figure 7 SmartFOAM 3 3 5 0 6 5 Dual Tank withMDTIIandIn lineStrainer...
Page 20: ...Page 19 SmartFOAM Figure 8 SmartFOAM 3 3 5 0 6 5 Dual Tank withMDTIIandFSSeriesStrainer...
Page 21: ...Page 20 SmartFOAM Figure 9 SmartFOAM 3 3 5 0 6 5 Dual Tank with ADTandIn lineStrainer...
Page 22: ...Page 21 SmartFOAM Figure 10 SmartFOAM 3 3 5 0 6 5 Dual Tank with ADTandFSSeriesStrainer...
Page 40: ...Page 39 SmartFOAM Figure 18 Typical 4 Inch Check Valve Installation Midship Pump...
Page 51: ...Page 50 SmartFOAM Figure 33 ADT Option Air Hose Connections Part 2...
Page 68: ...Page 67 SmartFOAM NOTES...
Page 80: ...79 Page 79 SmartFOAM NOTES...