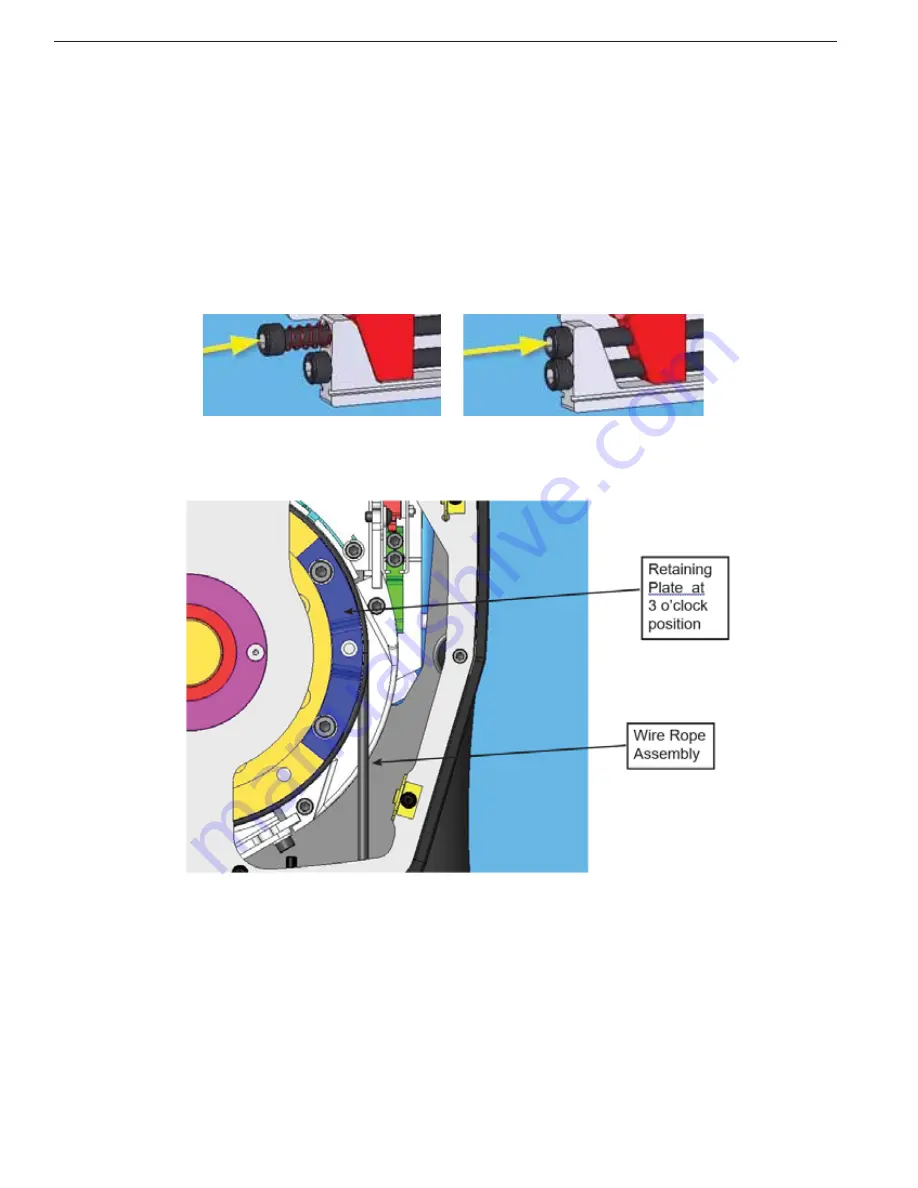
Wire Rope Replacement Adjustment for the Lower Limit Switch
In order to determine whether this adjustment needs to be performed you must push the upper allen head screw in
until it bottoms out against the body of the Limit Switch Assembly as illustrated in
diagram 4
below. While continu-
ing to press the upper screw, press the Jog Down Button until the drum stops and the Wire Rope Retaining Plate
is approximately at the 2-3 o’clock position as shown in
diagram 5
below. If the drum does not reach this position
when it stops, turn the upper allen head screw 1/2 turn counterclockwise with a 5 mm allen wrench. Jog the wire
rope up one full turn and repeat the process all over again.
Caution
: If the wire rope retaining plate rotates past the 4 o’clock position, release the Jog Down Button
immediately
or internal damage may occur. Press the Jog Up Button until the drum makes one full rotation and
adjust the Lower Limit Switch by turning the upper allen head screw one full turn clockwise.
Diagram 3
Diagram 4
G-Force® & Easy Arm Q2 - iQ2 Service Manual
Gorbel Inc.
Revised 5/21
8 - 2