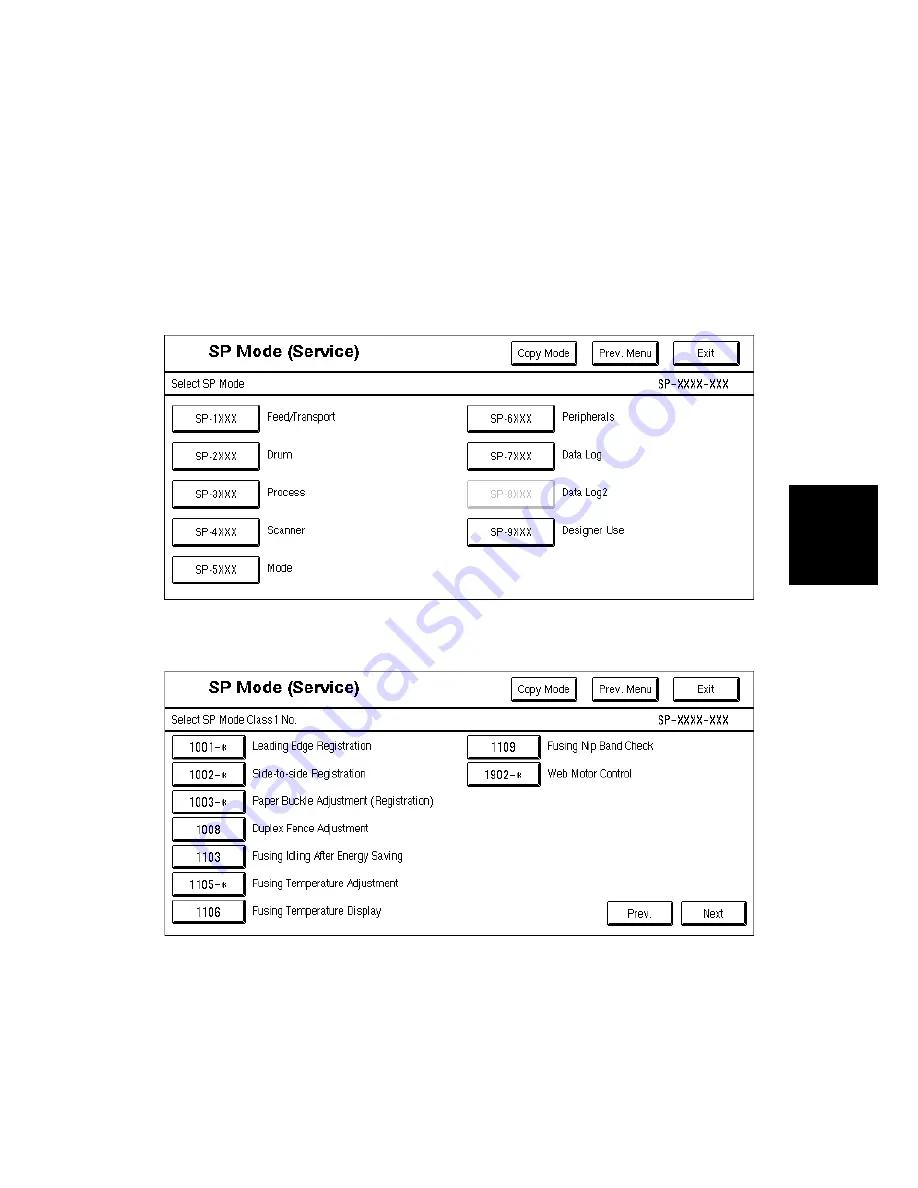
Rev. 9/2001
SERVICE PROGRAM MODE
SM
4-9
A294/A295
Serv
ic
e
Ta
b
le
s
Selecting the Program Number
Program numbers are composed of two or three levels.
There are two ways to select the program number.
Ten-key Pad
Input the required program number.
Touch Panel
1) Touch the 1st level program.
2) Touch the 2nd level program.
NOTE:
A “*” mark indicates that there are 3rd level programs.
3) Touch the 3rd level program.
A294M002.PCX
A294M003.PCX
CÓPIA NÃO CONTROLADA
CÓPIA NÃO CONTROLADA
Summary of Contents for A294
Page 2: ...C PIA N O CONTROLADA C PIA N O CONTROLADA...
Page 3: ...A294 A295 SERVICE MANUAL RICOH GROUP COMPANIES C PIA N O CONTROLADA C PIA N O CONTROLADA...
Page 4: ...C PIA N O CONTROLADA C PIA N O CONTROLADA...
Page 5: ...A294 A295 SERVICE MANUAL 000902MIU C PIA N O CONTROLADA C PIA N O CONTROLADA...
Page 6: ...C PIA N O CONTROLADA C PIA N O CONTROLADA...
Page 8: ...C PIA N O CONTROLADA C PIA N O CONTROLADA...
Page 10: ...C PIA N O CONTROLADA C PIA N O CONTROLADA...
Page 12: ...C PIA N O CONTROLADA C PIA N O CONTROLADA...
Page 26: ...C PIA N O CONTROLADA C PIA N O CONTROLADA...
Page 27: ...OVERALL INFORMATION C PIA N O CONTROLADA C PIA N O CONTROLADA...
Page 28: ...C PIA N O CONTROLADA C PIA N O CONTROLADA...
Page 49: ...DETAILED DESCRIPTIONS C PIA N O CONTROLADA C PIA N O CONTROLADA...
Page 50: ...C PIA N O CONTROLADA C PIA N O CONTROLADA...
Page 180: ...C PIA N O CONTROLADA C PIA N O CONTROLADA...
Page 181: ...INSTALLATION C PIA N O CONTROLADA C PIA N O CONTROLADA...
Page 182: ...C PIA N O CONTROLADA C PIA N O CONTROLADA...
Page 221: ...SERVICE TABLES C PIA N O CONTROLADA C PIA N O CONTROLADA...
Page 222: ...C PIA N O CONTROLADA C PIA N O CONTROLADA...
Page 230: ...SERVICE PROGRAM MODE Rev 9 2001 SM 4 8 A294 A295 C PIA N O CONTROLADA C PIA N O CONTROLADA...
Page 323: ...PREVENTIVE MAINTENANCE C PIA N O CONTROLADA C PIA N O CONTROLADA...
Page 324: ...C PIA N O CONTROLADA C PIA N O CONTROLADA...
Page 329: ...REPLACEMENT AND ADJUSTMENT C PIA N O CONTROLADA C PIA N O CONTROLADA...
Page 330: ...C PIA N O CONTROLADA C PIA N O CONTROLADA...
Page 457: ...TROUBLESHOOTING C PIA N O CONTROLADA C PIA N O CONTROLADA...
Page 458: ...C PIA N O CONTROLADA C PIA N O CONTROLADA...
Page 516: ...C PIA N O CONTROLADA C PIA N O CONTROLADA...
Page 517: ...3 000 SHEET FINISHER B302 C PIA N O CONTROLADA C PIA N O CONTROLADA...
Page 518: ...C PIA N O CONTROLADA C PIA N O CONTROLADA...
Page 554: ...C PIA N O CONTROLADA C PIA N O CONTROLADA...
Page 555: ...LARGE CAPACITY TRAY B303 C PIA N O CONTROLADA C PIA N O CONTROLADA...
Page 556: ...C PIA N O CONTROLADA C PIA N O CONTROLADA...
Page 578: ...C PIA N O CONTROLADA C PIA N O CONTROLADA...
Page 579: ...A3 DLT TRAY KIT B331 C PIA N O CONTROLADA C PIA N O CONTROLADA...
Page 580: ...C PIA N O CONTROLADA C PIA N O CONTROLADA...
Page 585: ...DIFFERENCES FROM THE A294 I A295 I MODELS C PIA N O CONTROLADA C PIA N O CONTROLADA...