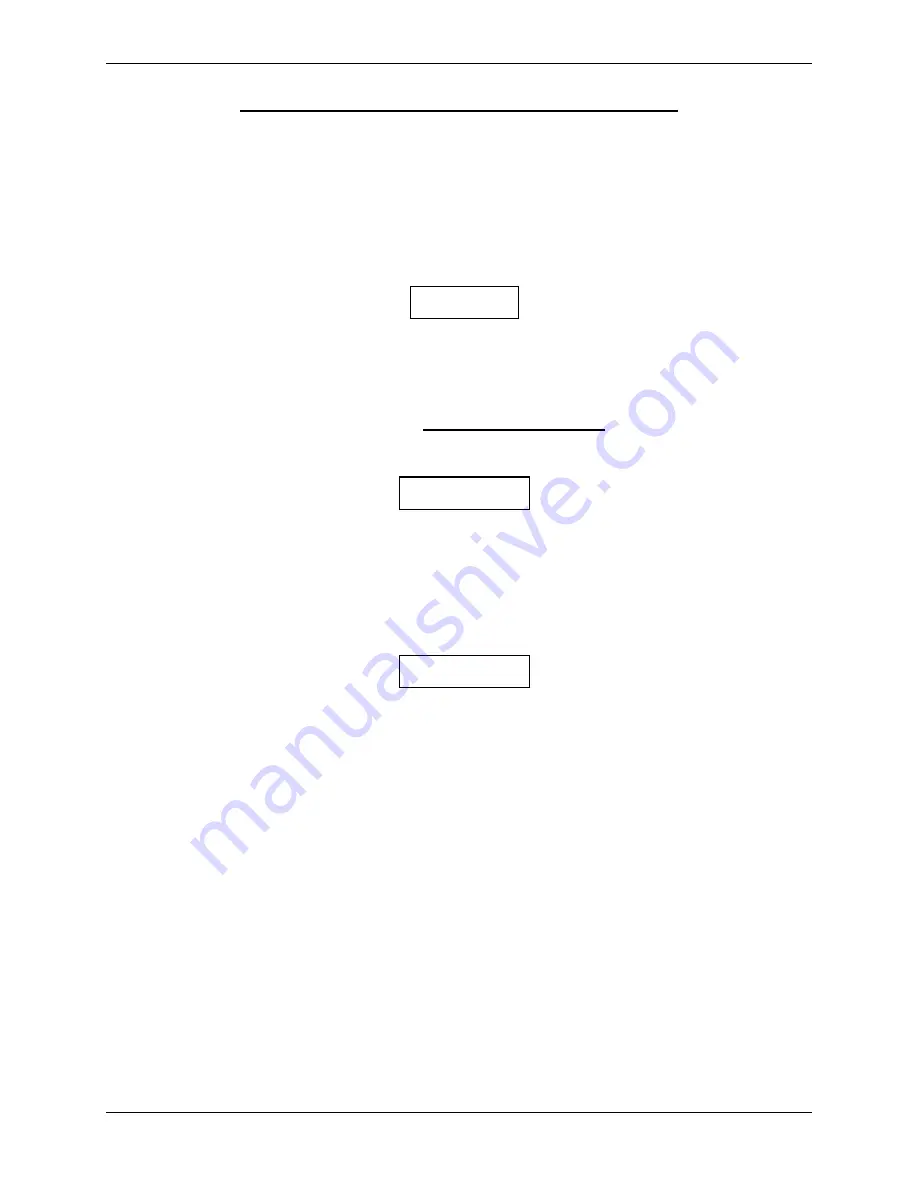
G1000 NXi System Maintenance Manual
Page ii
King Air 300 Series
Revision 1
190-00716-N1
INFORMATION SUBJECT TO EXPORT CONTROL LAWS
This document may contain information which is subject to the Export Administration
Regulations (“EAR”) issued by the United States Department of Commerce (15 CFR, Chapter
VII Subchapter C) and which may not be exported, released or disclosed to foreign nationals
inside or outside the United States without first obtaining an export license. The preceding
statement is required to be included on any and all reproductions in whole or in part of this
manual.
This product, its packaging, and its components contain chemicals known to the State of
California to cause cancer, birth defects, or reproductive harm. This Notice is being provided in
accordance with California's Proposition 65. If you have any questions or would like additional
information, please refer to our web site at www.garmin.com/prop65.
The GDU lens is coated with a special anti-reflective coating that is very sensitive to skin oils,
waxes and abrasive cleaners. CLEANERS CONTAINING AMMONIA WILL HARM THE ANTI-
REFLECTIVE COATING. It is very important to clean the lens using a clean, lint-free cloth and
an eyeglass lens cleaner that is specified as safe for anti-reflective coatings.
All G1000 screen shots used in this document are current at the time of publication. Screen
shots are intended to provide visual reference only. All information depicted in screen shots,
including software file names, versions and part numbers, is subject to change and may not be
up to date.
CAUTION
WARNING
IMPORTANT
Summary of Contents for G1000 NXi
Page 112: ......