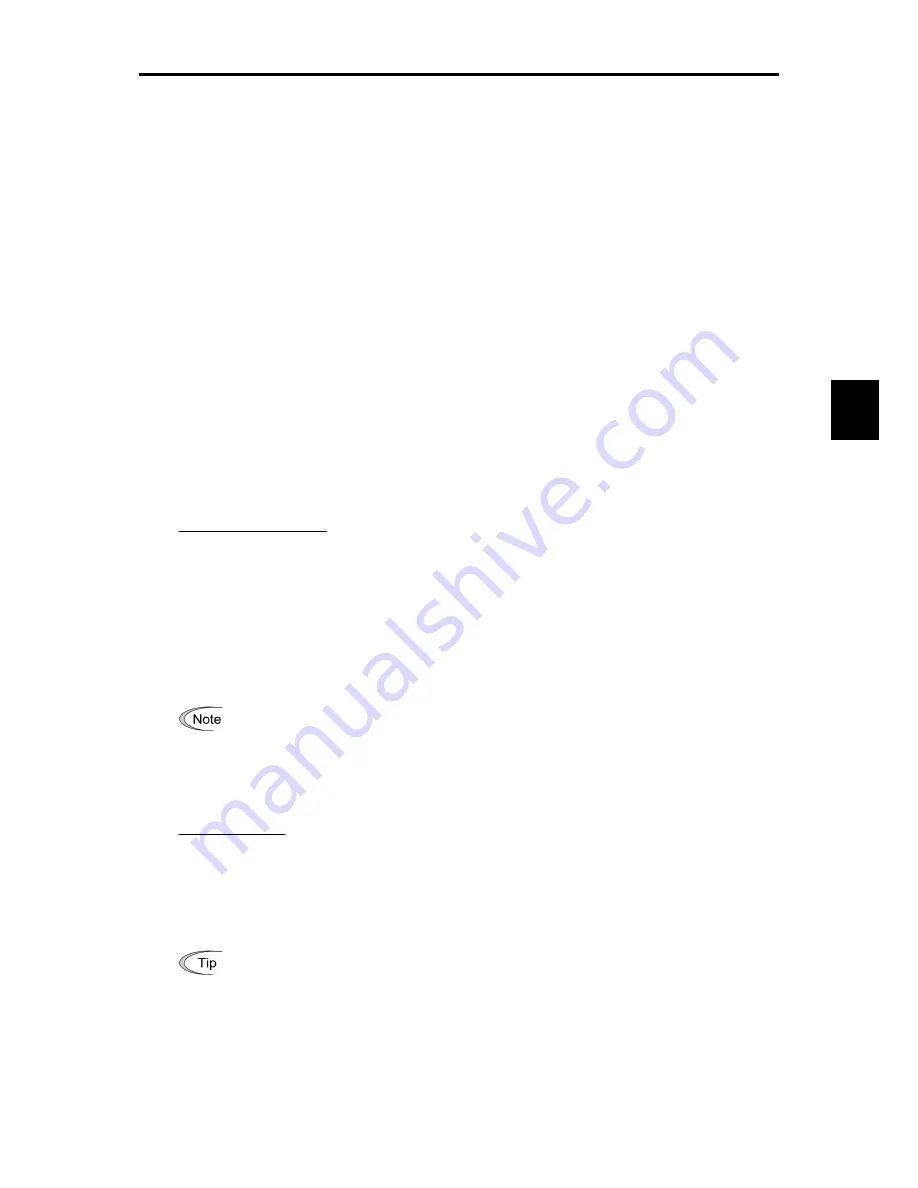
6.3 Peripheral Equipment
6-7
Chap. 6
SEL
ECT
ING P
E
R
IP
HE
RAL
EQ
UIPM
ENT
6.3 Peripheral Equipment
[ 1 ] Molded Case Circuit Breaker (MCCB), Earth Leakage Circuit Breaker
(ELCB) and Magnetic Contactor (MC)
[ 1.1 ] Functional Overview
■
MCCBs and ELCBs*
*With the exception of those exclusively designed for protection from ground faults
Molded Case Circuit Breakers (MCCBs) are designed to protect the power circuits between the
power supply and inverter's main circuit terminals (L1/R, L2/S and L3/T for three phase, or L1/L
and L2/N for single-phase power source) from overload or short-circuit, which in turn prevents
secondary accidents caused by the inverter malfunctioning.
Earth Leakage Circuit Breakers (ELCBs) function in the same way as MCCBs.
Built-in overcurrent/overload protective functions protect the inverter itself from failures related to
its input/output lines.
■
MCs
An MC can be used at both the power input and output sides of the inverter. At each side, the MC
works as described below. When inserted in the output circuit of the inverter, the MC can also
switch the motor drive power source between the inverter output and commercial power lines.
At the power source side
Insert an MC in the power source side of the inverter in order to:
(1) Forcibly cut off the inverter from the power source (generally, commercial/factory power lines)
with the protective function built into the inverter, or with the external signal input.
(2)
Stop the inverter operation in an emergency when the inverter cannot interpret the stop
command due to internal/external circuit failures.
(3) Cut off the inverter from the power source when the MCCB inserted in the power source side
cannot cut it off for maintenance or inspection purpose. For the purpose only, it is
recommended that you use an MC capable of turning the MC on/off manually.
When your system requires the motor(s) driven by the inverter to be started/stopped with
the MC, the frequency of the starting/stopping operation should be once or less per hour.
The more frequent the operation, the shorter operation life of the MC and capacitor/s used
in the DC link circuit due to thermal fatigue caused by the frequent charging of the current
flow. If this is not necessary, start/stop the motor with the terminal commands (FWD),
(REV) and/or (HLD), or with the keypad.
At the output side
Insert an MC in the power output side of the inverter in order to:
(1) Prevent externally turned-around current from being applied to the inverter power output
terminals (U, V, and W) unexpectedly. An MC should be used, for example, if a circuit that
switches the motor driving power source between the inverter output and commercial power
lines is connected to the inverter.
As application of high voltage external current to the inverter's secondary (output) circuits
may break the Insulated Gate Bipolar Transistors (IGBTs), MCs should be used in the
power control system circuits to switch the motor drive power source to the commercial
power lines after the motor has come to a complete stop. Also ensure that voltage is never
mistakenly applied to the inverter output terminals due to unexpected timer operation, or
similar.
(2) Drive more than one motor selectively by a single inverter.
(3) Selectively cut off the motor whose thermal overload relay or equivalent devices have been
activated.
Summary of Contents for frenic mini series
Page 1: ...USER S MANUAL Fuji Electric Co Ltd MEH446...
Page 2: ...Compact Inverter User s Manual...
Page 62: ...4 4 4 3 Drive Command Generator Figure 4 2 Drive Command Generator...
Page 66: ...4 8 Figure 4 3 d Terminal Command Decoder ORing with Link Commands Ignoring Link Commands...
Page 68: ...4 10 4 5 Digital Output Selector Figure 4 4 Digital Output Signal Selector...
Page 70: ...4 12 4 6 Analog Output FMA Selector Figure 4 5 Analog Output FMA Selector...
Page 74: ...4 16 4 8 PID Frequency Command Generator Figure 4 7 PID Frequency Command Generator...
Page 81: ...Part 3 Peripheral Equipment and Options Chapter 6 SELECTING PERIPHERAL EQUIPMENT...
Page 124: ...Part 5 Specifications Chapter 8 SPECIFICATIONS Chapter 9 FUNCTION CODES...
Page 134: ...8 3 Common Specifications 8 9 Chap 8 SPECIFICATIONS 8 3 Common Specifications...
Page 135: ...8 10...
Page 257: ...App H Replacement Information A 33 App FVR C11S vs FRENIC Mini...
Page 261: ...Glossary This glossary explains the technical terms that are frequently used in this manual...