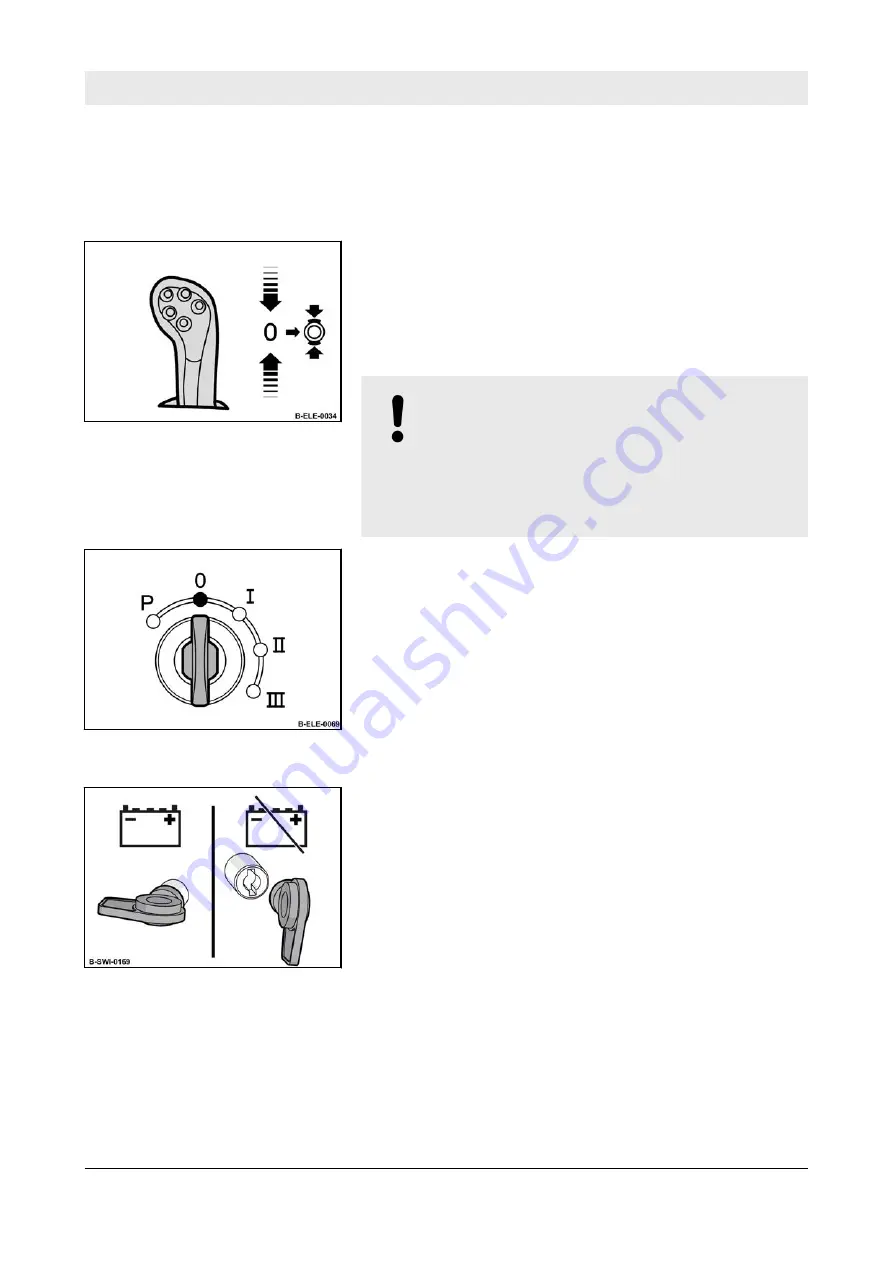
6.7
Park the machine in secured condition.
1.
Drive the machine onto level and firm
ground.
2.
To stop the machine return the travel lever
to middle position and shift it to the right to
lock (parking brake position).
ð
The parking brake warning lamp lights
up.
NOTICE!
Danger of engine damage!
– Do not shut down the engine all
of a sudden from full load speed,
but let it idle for about 2 minutes.
3.
Turn the ignition key to position “0” and pull
it out.
4.
Open and secure the engine hood
Chapter 8.2.1 „Open and secure the
.
5.
Turn the main battery switch counter-clock-
wise and pull it out.
6.
Close the engine hood and lock it if neces-
sary.
Fig. 78
Fig. 79
Fig. 80
Operation – Park the machine in secured condition.
BW 213 D-5
115
Summary of Contents for BOMAG BW 213 D-5
Page 2: ...2...
Page 9: ...1 Introduction Introduction BW 213 D 5 9...
Page 14: ...Introduction Machine type plate and engine type plate BW 213 D 5 14...
Page 15: ...2 Technical data Technical data BW 213 D 5 15...
Page 20: ...Technical data Noise and vibration data BW 213 D 5 20...
Page 21: ...3 Concerning your safety Concerning your safety BW 213 D 5 21...
Page 63: ...4 Display and control elements Display and control elements BW 213 D 5 63...
Page 82: ...Display and control elements Outside of machine BW 213 D 5 82...
Page 83: ...5 Tests before taking into operation Tests before taking into operation BW 213 D 5 83...
Page 95: ...6 Operation Operation BW 213 D 5 95...
Page 124: ...Operation Emergency procedures BW 213 D 5 124...
Page 125: ...7 Loading transporting the machine Loading transporting the machine BW 213 D 5 125...
Page 133: ...8 Maintenance Maintenance BW 213 D 5 133...
Page 207: ...9 Trouble shooting Trouble shooting BW 213 D 5 207...
Page 217: ...10 Waste disposal Waste disposal BW 213 D 5 217...
Page 219: ...11 List of special tools List of special tools BW 213 D 5 219...
Page 220: ...Belt tension tester BOMAG No 079 947 09 Fig List of special tools BW 213 D 5 220...
Page 221: ......
Page 222: ......