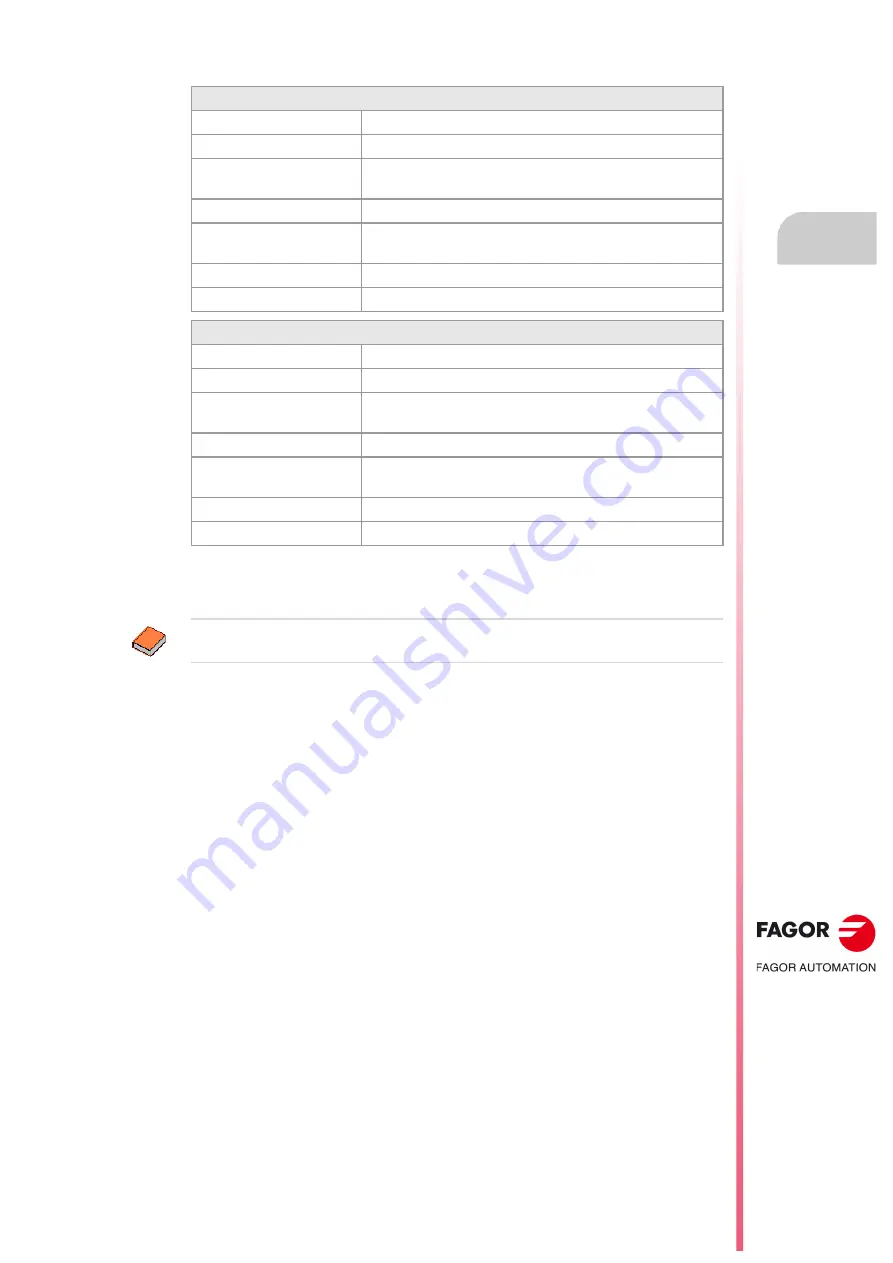
Hardware configuration.
CNC 8070
CEN
T
RAL UNIT + MONITOR (Q7-A
PLATFORM).
6.
Conn
ecti
ons.
·129·
(R
EF
: 1911)
Bus configuration.
Element connection.
Use an inline topology. Join the B64 connector of the CNC to the X1(IN) connector of the
first header. Connect the other of headers, joining the X2 (OUT) connector of one header
with the X1 (IN) connector of the following one. Do not connect the X2(OUT) connector of
the last header.
In order to ensure proper performance, the connection cable must be inserted all the way
into the connectors so they're latched. This ensures that the cable is properly latched and
does not come off due to vibration.
Module identification.
The node number for each header is not defined on this bus. The node number is assigned
by the configurator on the basis of its designed topology.
Transmission speed.
The transmission speed is 100 MHz. Use a cable having the recommended characteristics
to ensure this speed.
Activate the bus on the CNC.
Activate the bus on the CNC using the machine parameter ETHERCATBUS.
Configuring the EtherCAT bus.
Fagor supplies the configurator “KPA EtherCAT Studio” (by Koening-pa GmbH) under
license, which can operate both online and offline, to define the bus topology and create the
ENI file containing the bus device information. This file must be copied to the folder
../Mtb/Data of the CNC with the name "fagor_ethercatConfFile.xml". This file also uses the
"Fagor EtherCAT Mapper" program for determining the resources available in the bus.
ECAT-CABLE cable
Type.
Industrial Cat 6A shielded 8-wire Ethernet cable (twisted pairs).
Diameter.
6.3 mm - 6.9 mm.
Flexibility.
Minimum static bending radius 4 x diameter.
Minimum dynamic bending radius 8 x diameter.
Covering.
PVC. Polyvinyl chloride.
Temperature.
Work: -20 ºC / 80 ºC (-4 ºF / 176 ºF).
Storage: -20 ºC / 80 ºC (-4 ºF / 176 ºF).
Color.
Yellow, RAL 1021.
Minimum/maximum length.
1 m (3.2 ft) / 7 m (23 ft).
ECAT-CABLE-FLEX cable
Type.
Industrial Cat 6A shielded 8-wire Ethernet cable (twisted pairs).
Diameter.
6.3 mm - 6.9 mm.
Flexibility.
Minimum static bending radius 4 x diameter.
Minimum dynamic bending radius 8 x diameter.
Covering.
PUR. Polyurethane.
Temperature.
Work: -40 ºC / 80 ºC (-40 ºF / 176 ºF).
Storage: -40 ºC / 80 ºC (-40 ºF / 176 ºF).
Color.
Yellow, RAL 1021.
Minimum/maximum length.
10 m (32.8 ft) / 100 m (328 ft).
Refer to the installation manual for further information on installing and using the EtherCAT configurator
and mapper.
Summary of Contents for CNC 8070
Page 1: ...Ref 1911 8070 CNC Hardware configuration...
Page 8: ...BLANK PAGE 8...
Page 14: ...BLANK PAGE 14...
Page 18: ...BLANK PAGE 18...
Page 22: ...BLANK PAGE 22...
Page 24: ...BLANK PAGE 24...
Page 26: ...BLANK PAGE 26...
Page 28: ...Hardware configuration CNC 8070 1 PREVIOUS INFORMATION 28 REF 1911...
Page 94: ...Hardware configuration CNC 8070 6 CENTRAL UNIT MONITOR Q7 A PLATFORM 94 REF 1911 C70 15AT...
Page 273: ...Hardware configuration CNC 8070 273 User notes REF 1911...
Page 274: ...Hardware configuration CNC 8070 274 User notes REF 1911...
Page 275: ...Hardware configuration CNC 8070 275 User notes REF 1911...