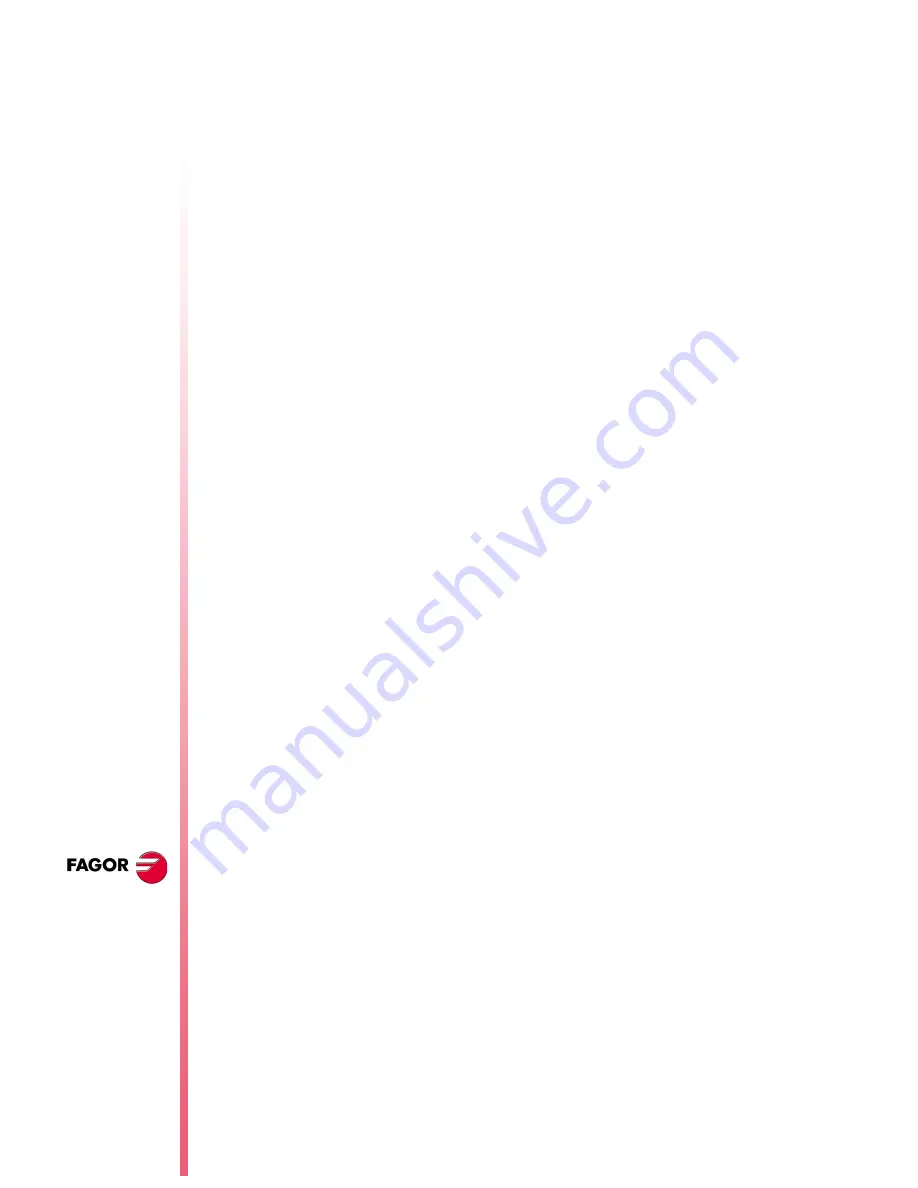
Page 46 of 48
80
40 CNC
New management
of the distance-
coded reference
mark (I0)
N
EW
F
EATURES
(S
OFT
M: 7.1
X
)
48
5
New management of the distance-coded reference mark (I0)
From this version on, the distance-coded I0 via SERCOS may be
managed using the input of the drive's second feedback.
•
The axis parameters to define the distance-coded I0 are at the
CNC.
We recommend to set axis parameter POSINREF=NO. Otherwise,
it generates a movement to the position defined by axis parameter
REFVALUE.
•
The parameters related to the counting of pulses (feedback) are
at the drive. At FAGOR drives, the parameters are:
The drive version must be V4.10 or V5.10 ( or greater).
6
Improved look ahead
Machining feedrate variations are now smoother thanks to filtered
acc/dec in short movements.
7
Leadscrew error compensation in both directions
Bidirectional leadscrew error compensation
From this version on, it is possible to define a different leadscrew
compensation for each moving direction.
This is defined in the leadscrew compensation tables. Each row of
the table contains the following data:
•
The position of the axis to be compensated.
•
The amount of error of the axis at that point. In the positive
direction.
•
The amount of error of the axis at that point. In the negative
direction.
For each axis position, define the amount of error to compensate in
both directions. If the error in the negative direction has a zero value
in all positions, it is assumed that the error defined for the positive
direction is valid for both directions.
Likewise, the compensation defined in a single direction or for both,
the compensation error at the reference point does not need to be
zero.
I0TYPE (P52)
I0CODI1 (P68)
I0CODI2 (P69)
ABSOFF (P53)
REFDIREC (P33) REFEED2 (P35)
AXISCHG (P16)
LOOPCHG (P26)
GP10
Feedback2Type
NP117
ResolutionOfFeedback2
NP118
ResolutionOfLinearFeedback
PP115.0
PositionFeedback2Type
Summary of Contents for 8040 MC CNC
Page 1: ...REF 0307 SOFT M 7 XX SOFT M 7 1X 8040 CNC NEW FEATURES...
Page 2: ...Page 2 of 2 8040 CNC NEW FEATURES SOFT M 7 XX SOFT M 7 1X...
Page 45: ...User notes NEW FEATURES SOFT M 7 XX Page 41 of 48 8040 CNC...
Page 46: ...User notes NEW FEATURES SOFT M 7 XX Page 42 of 48 8040 CNC...
Page 52: ...User notes NEW FEATURES SOFT M 7 1X Page 48 of 48 8040 CNC...
Page 53: ...Operating Manual MC option Ref 0204 ing...
Page 143: ...Self teaching Manual MC option Ref 0112 ing...
Page 147: ...Chapter 1 Theory on CNC machines...
Page 156: ...Chapter 2 Theory on tools...
Page 164: ...Chapter 3 Hands on training...
Page 186: ...Chapter 4 Automatic Operations...
Page 201: ...Chapter 5 Summary of work cycles...
Page 220: ...Chapter 6 Conversational part programs...
Page 235: ...Appendix I Programming example...
Page 237: ...Self teaching Manual Appendix I Page 3 MC Model Programming example Step 1 Surface milling 1...
Page 239: ...Self teaching Manual Appendix I Page 5 MC Model Programming example Step 3 Rectangular boss 3...
Page 240: ...Self teaching Manual Appendix I Page 6 MC Model Programming example Step 4 Circular pocket 4...