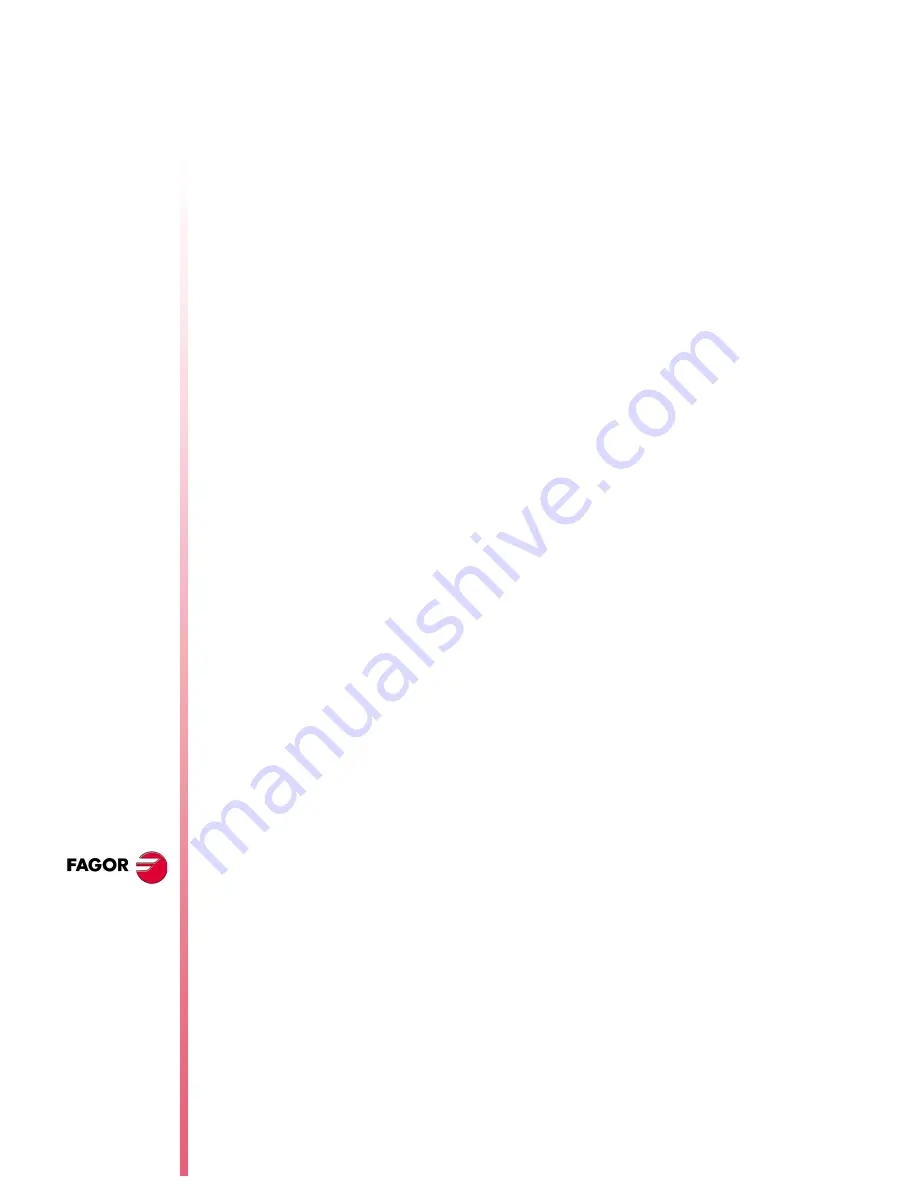
Page 32 of 48
80
40 CNC
Oscilloscope
function
N
EW
F
EATURES
(S
OFT
M: 7.
XX
)
Indicate the axis and the parameter number and the gear separated
by a dot. Examples: [X.CP1.0], [Y.CP20.2], [Z.SP1.1]
Save and load the configurations.
The system lets you save the current configuration into a program
type file in ASCII format. To do that, set general machine parameter
STPFILE with the number (other than 0) to be assigned to the
configuration file.
The configuration file may be treated like any other program, sent
out via DNC or even edited.
When saving or loading a configuration, the CNC first checks if the
file already exists in User RAM and if not, it will look for it in the
Memkey Card.
Several configurations may be saved in the configuration file. Each
configuration must be assigned a name of up to 40 characters.
The following softkeys are related to this feature.
Save
To save the current configuration, press the [Save] softkey and enter
the name to save it with up to 40 characters. If there is a previously
saved configuration with the same name, it will ask whether it must
be replaced or not.
Load
To load a previously saved configuration, press the [Load] softkey
and select it from the list on the screen. If the configuration makes
not sense (for example, because the CNC does not have an axis that
that configuration refers to), the CNC will warn the user and it will
only load the portion of the configuration read until that error came
up.
Delete
To delete one of the saved configurations, press the [Delete] softkey,
select it from the list on the screen and press [Enter].
Reset
Pressing the [Reset] softkey deletes or resets the current
configuration. There are no variables or parameters selected and the
rest of conditions (colors, trigger, etc.) assume the values assigned
by default.
32.2 Scale / Offsets
To change the amplitude of each signal, move them vertically or
adjust the time base for all of them.
The right side of the screen shows:
•
The vertical scale or amplitude by square for each signal (next to
the name of the variable)
•
The horizontal scale or time base (t/div) for all the signals.
To change the amplitude, use the [
Ï
] [
Ð
] keys to place the focus in
the "Scale" field of the desired variable. Then use the [
Í
] [
Î
] keys
or [page up] [page down] to select one of the permitted values or
press [X] for auto-scaling.
To move the signal vertically, use the [
Ï
] [
Ð
] keys to place the focus
in the "Offset" field of the desired variable. Then use the [
Í
] [
Î
]
keys or [page up] [page down] to move the signal or press one of
these keys:
[U]
To move it up as high as possible
[D]
To move it down as low as possible
Summary of Contents for 8040 MC CNC
Page 1: ...REF 0307 SOFT M 7 XX SOFT M 7 1X 8040 CNC NEW FEATURES...
Page 2: ...Page 2 of 2 8040 CNC NEW FEATURES SOFT M 7 XX SOFT M 7 1X...
Page 45: ...User notes NEW FEATURES SOFT M 7 XX Page 41 of 48 8040 CNC...
Page 46: ...User notes NEW FEATURES SOFT M 7 XX Page 42 of 48 8040 CNC...
Page 52: ...User notes NEW FEATURES SOFT M 7 1X Page 48 of 48 8040 CNC...
Page 53: ...Operating Manual MC option Ref 0204 ing...
Page 143: ...Self teaching Manual MC option Ref 0112 ing...
Page 147: ...Chapter 1 Theory on CNC machines...
Page 156: ...Chapter 2 Theory on tools...
Page 164: ...Chapter 3 Hands on training...
Page 186: ...Chapter 4 Automatic Operations...
Page 201: ...Chapter 5 Summary of work cycles...
Page 220: ...Chapter 6 Conversational part programs...
Page 235: ...Appendix I Programming example...
Page 237: ...Self teaching Manual Appendix I Page 3 MC Model Programming example Step 1 Surface milling 1...
Page 239: ...Self teaching Manual Appendix I Page 5 MC Model Programming example Step 3 Rectangular boss 3...
Page 240: ...Self teaching Manual Appendix I Page 6 MC Model Programming example Step 4 Circular pocket 4...