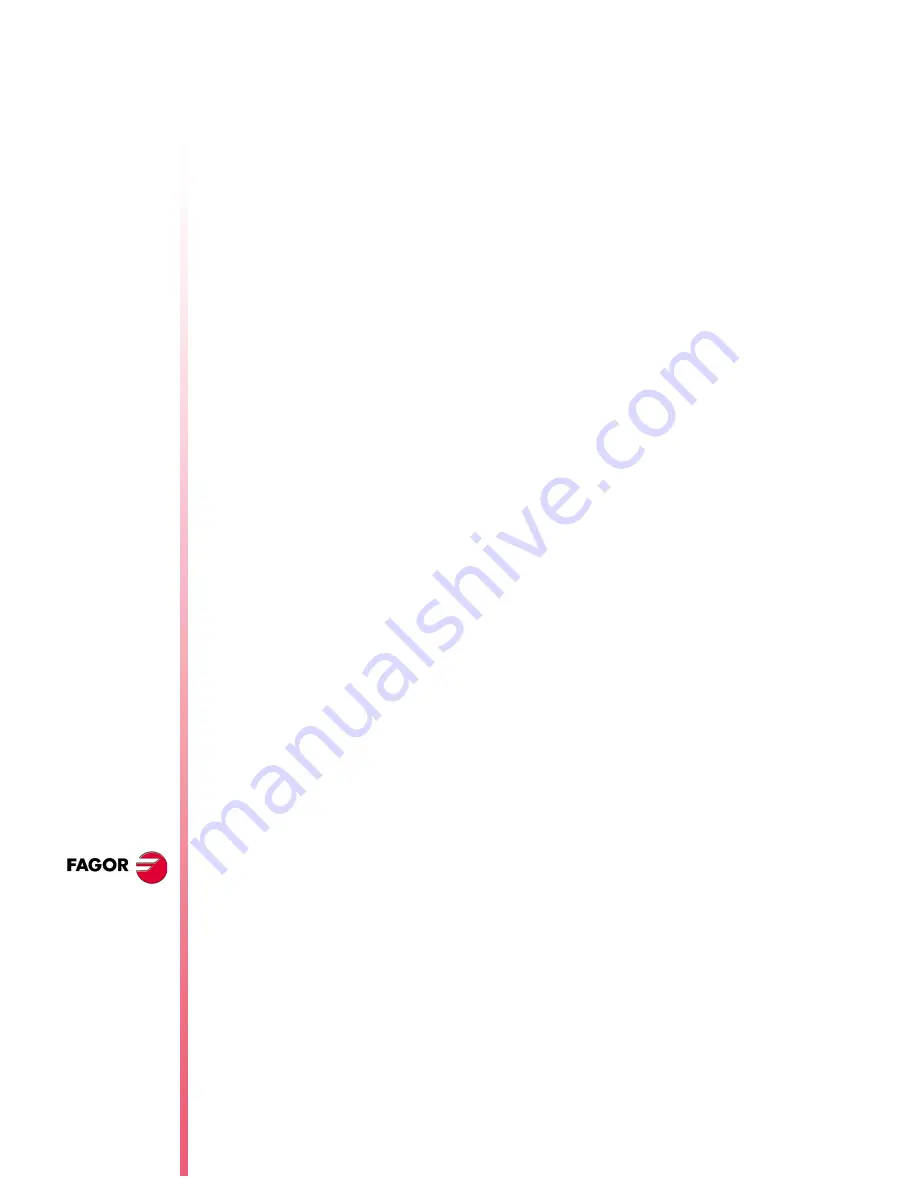
Page 26 of 48
80
40 CNC
Oscilloscope
function
N
EW
F
EATURES
(S
OFT
M: 7.
XX
)
If the measuring difference does not exceed the maximum allowed
or tool life monitoring is not available:
•
It updates global arithmetic parameter P298, P299 and the length
and radius wear values of the tool offset selected in the tool offset
table.
If the dimension of each cutting edge was requested, parameter "N",
the lengths are assigned to global arithmetic parameters P271 and
on, and the radii to global arithmetic parameters P251 and on.
32 Oscilloscope function
The oscilloscope function is a help tool to adjust the CNC and the
drives.
It is possible to represent 4 previously selected variables and
manipulate CNC machine parameters and variables. When using
Fagor Sercos drives, it is also possible to set the parameters of the
drive.
When requesting information (variable or parameter) of a drive that
is not connected via Sercos or when having an old software version,
the message "Variable does not exist" will be displayed.
Changing the machine parameters of the CNC and the drive
requires a password.
How to operate
To access the Oscilloscope mode, select:
Op Mode - Diagnosis - Adjustements - Scope
Define the variables to be analyzed, the trigger conditions and the
machine parameters of the CNC or the drive to be modified.
Execute a part-program moving the axis or axes to be adjusted.
Capture data and then analyze it.
Once data capture has ended, or has been interrupted, it is possible
to analyze the signals and modify the parameters that have been
previously selected, in order to improve the machining conditions.
Capture data, analyze it and modify the parameters again until
achieving the best machining conditions.
Suggestions
Execute endless repetitive movements.
After adjusting the axis separately, readjust the interpolating axes
together.
It is up to the user to judge what the best adjustment is, the
oscilloscope function is an assistance tool.
Operation
To enter or modify a data on the screens, it must be selected and it
must have the editing focus.
P298 = measured radius - theoretical radius (R)
P299 = measured length - theoretical length (L)
R
= theoretical radius (it maintains the previous value).
I
= measured radius - theoretical radius (R) [New wear value]
L
= theoretical length (it maintains the previous value).
K
= measured length - theoretical length (L) [New wear value]
Summary of Contents for 8040 MC CNC
Page 1: ...REF 0307 SOFT M 7 XX SOFT M 7 1X 8040 CNC NEW FEATURES...
Page 2: ...Page 2 of 2 8040 CNC NEW FEATURES SOFT M 7 XX SOFT M 7 1X...
Page 45: ...User notes NEW FEATURES SOFT M 7 XX Page 41 of 48 8040 CNC...
Page 46: ...User notes NEW FEATURES SOFT M 7 XX Page 42 of 48 8040 CNC...
Page 52: ...User notes NEW FEATURES SOFT M 7 1X Page 48 of 48 8040 CNC...
Page 53: ...Operating Manual MC option Ref 0204 ing...
Page 143: ...Self teaching Manual MC option Ref 0112 ing...
Page 147: ...Chapter 1 Theory on CNC machines...
Page 156: ...Chapter 2 Theory on tools...
Page 164: ...Chapter 3 Hands on training...
Page 186: ...Chapter 4 Automatic Operations...
Page 201: ...Chapter 5 Summary of work cycles...
Page 220: ...Chapter 6 Conversational part programs...
Page 235: ...Appendix I Programming example...
Page 237: ...Self teaching Manual Appendix I Page 3 MC Model Programming example Step 1 Surface milling 1...
Page 239: ...Self teaching Manual Appendix I Page 5 MC Model Programming example Step 3 Rectangular boss 3...
Page 240: ...Self teaching Manual Appendix I Page 6 MC Model Programming example Step 4 Circular pocket 4...