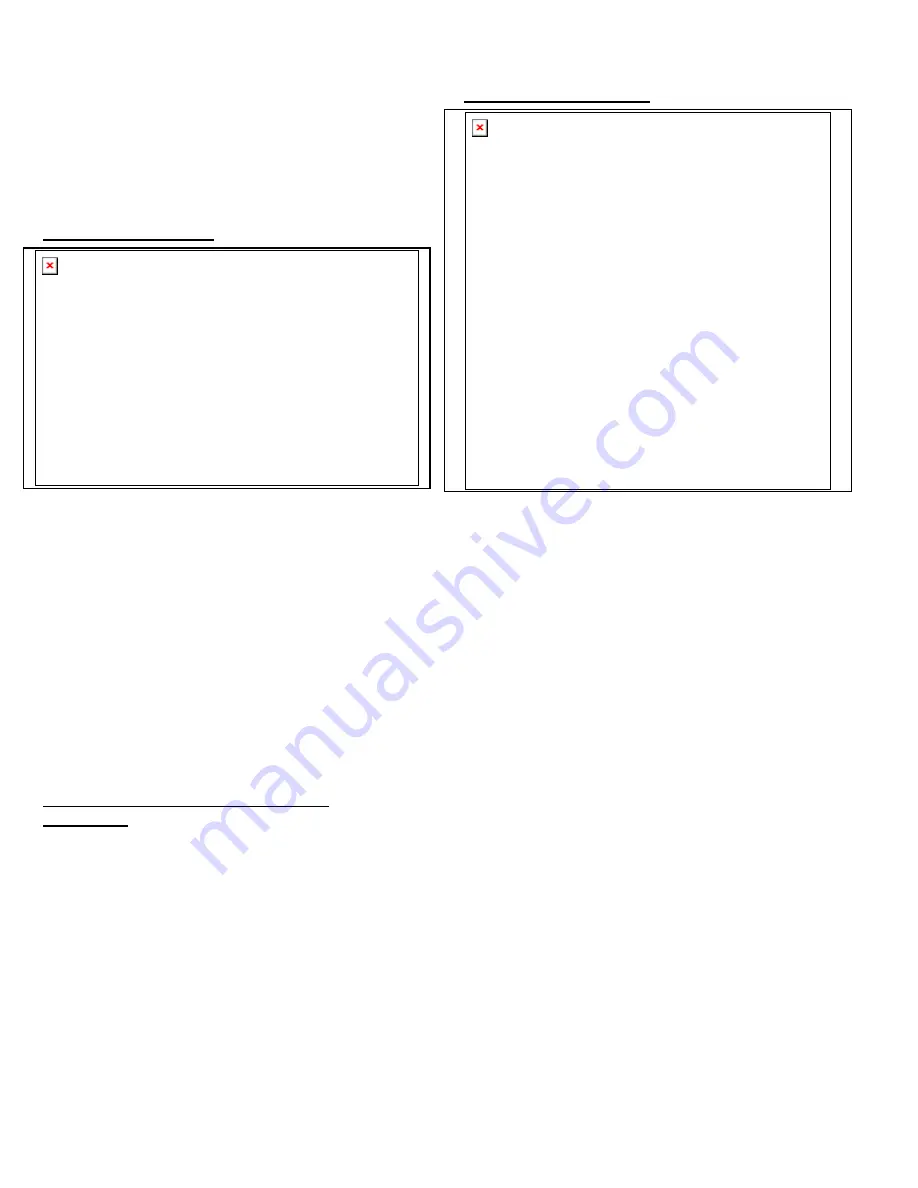
SECTION B -PARTS PREPARATION-
52
Unfortunately, the best wheel boxes (listed on page 27) are
rarely available. If your wheelboxes do not match the
specifications on page 19, the crankshaft in the wiper
motor may be modified to compensate. See
Stroke
Changes
below.
For
electrical
testing
, see the electrical troubleshooting
guide.
CONNECTING TUBES
b\wiper3
Undo the large nut and remove the cable tube/wheelbox
assembly from the motor.
Remove the wheelbox backing plates and remove the
tubes from the wheelboxes.
Using a tubing cutter or hacksaw, cut off approximately 2
3
/
4
" from one end of the original tube between the right
wheelbox and the motor. Save the nut and the piece of
tubing. Use the short tube for the guide at the end of the
second wheelbox.
Slide the nut onto tube shorter tube supplied (the one with
just one end flared).
Flare
the end of the tube with the nut. Slide the drive
cable through the tube. If the cable is tight at the new
flare, use a
1
/
4
" drill bit to "clean" the inside of the tube.
CHECKING THE WHEELBOX/CABLE
FUNCTION
Because of manufacturing variations, it’s a good practice
to check for the correct mesh between the cable, gear and
the wheelbox housing.
MOTOR PREPARATION
If you are sure that the wiper motor functions correctly and
don't want to disassemble the wiper motor itself, skip steps
4 through 8.
Take out the 4 screws holding the
cover
to the gearbox,
and remove the cover.
Remove the
circlip
and
washer
from the connecting rod
big end, and remove the connecting rod. Note the bottom
washer.
Remove the circlip and washer from the back side of the
crankshaft, and push out the crankshaft from the housing.
Retain all the parts! Note the
thrust washer
on the inside
of the crankpin.
Mark
the relative position of the round motor housing to
the aluminum gear reduction housing. Remove the two
long screws holding the motor housing to the frame.
Separate the two (with gentle soft hammer taps if
necessary). Do not lose the felt washer and thrust washer
in the bearing cup at the bottom of the housing.
Inspect the
brushes
for wear or sticking, the commutator
for excess wear and arcing, and the lower bearing. Clean
the parts with a solvent if necessary. Work the brushes in
and out to insure free motion.
Install the
armature
carefully into the gear housing until it
contacts the sides of the brushes. Using a hook shaped
wire or other appropriate tool, retract each brush in turn so
that the commutator can slide past the edges of both
brushes and continue into the gear case
Put 1 or 2 drops of oil in the lower bearing of the armature
housing.
Excess
oil will contaminate the brushes later on.
Install the
armature housing
, aligning the marks on the
housing and the frame. Reinstall the long retaining
screws.
Summary of Contents for 427 ROADSTER
Page 4: ...SECTION A PARTS NEEDED 4...
Page 13: ...SECTION A PARTS NEEDED 13...
Page 55: ...55 SECTION C CHASSIS PREPARATION Assembling the chassis and preparation for paint...
Page 56: ...56...
Page 70: ...70 SECTION E BODY PREPARATION...
Page 73: ...SECTION E BODY PREPARATION 73...
Page 76: ...SECTION E BODY PREPARATION 76 ebod stripe...
Page 95: ...95 SECTION F SUSPENSION ASSEMBLY...
Page 107: ...107 SECTION G BODY INTERIOR...
Page 117: ...SECTION G BODY INTERIOR 117 eint tunnel...
Page 142: ...142 SECTION H FINAL OPERATIONS...