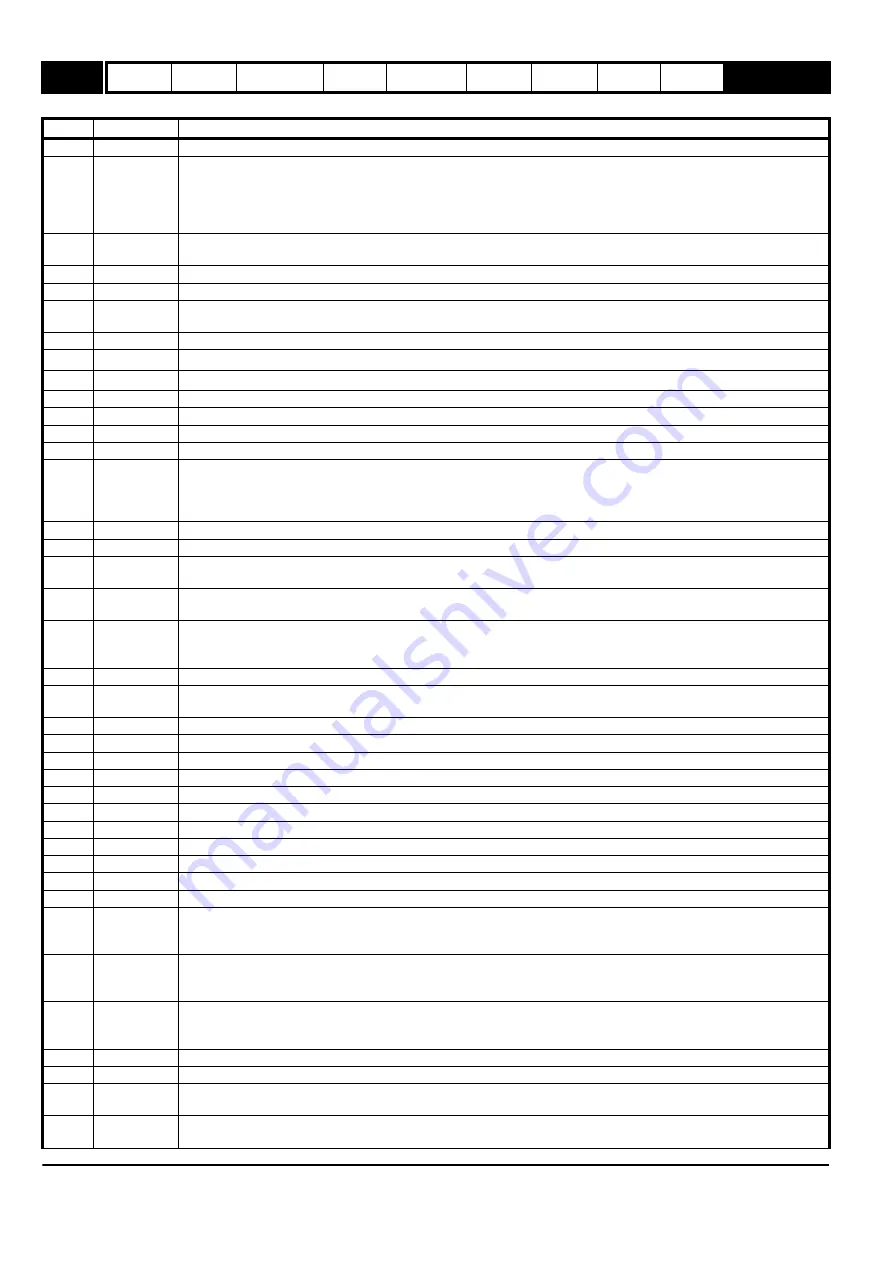
Menu 10
132
Commander SK Advanced User Guide
www.controltechniques.com Issue Number: 9
Table 10-17 Trip indications
No.
String
Cause of trip
1
UU***
DC bus under voltage - Low AC supply voltage. Low DC Bus voltage when drive supplied by external DC power supply.
2
OU
DC bus over voltage.
Drive voltage rating Instantaneous trip
200V 415V
400V 830V
Excessive inertia in the machine during deceleration. Deceleration rate is set too fast for inertia of machine.
3
OI.AC**
AC instantaneous over current. Insufficient ramp times. Phase to phase or phase to ground short circuit at the drive
output. Autotune required.
4
OI.br**
Braking resistor instantaneous current trip. Excessive current in braking resistor. Braking resistor value too small.
6
Et
7
O.SPd
Overspeed. Excessive motor speed (typically caused by the mechanical load driving the motor). The drive produces an
overspeed trip if the output frequency (Pr
5.01
) exceeds 1.2 x Maximum frequency and regenerating and in current limit.
18
tunE
Auto-tune stopped before completion (see Pr
19
It.br
I
2
t on braking resistor (see Pr
20
It.AC
I
2
t on drive output current (see Pr
21
O.ht1
Drive over-heat (IGBT junctions) based on thermal model (see Pr
22
O.ht2
Drive over-heat based on heatsink temperature (see Pr
24
th
Motor thermistor trip
26
O.Ld1*
+24V or Digital output overload
27
O.ht3
Drive over-heat based on thermal model (see Pr
The drive will attempt to stop the motor before tripping. If the motor does not stop in 10 seconds the drive trips
immediately. Thermal model looks at DC Bus ripple as well as output current. This is to protect the DC Bus stage from
overheating.
28
cL1
Analog input 1 current mode: current loss (see Pr
30
SCL
Serial comms timeout with external keypad on drives comms port
31
EEF
Internal drive EEPROM failure. All the parameters are set to default. The trip can only be removed by entering a load
default command (see Pr
32
PH
High input voltage phase imbalance or input phase loss. Normally a motor load of between 50 and 100% of drive rating is
required to trigger the trip. The drive will attempt to stop the motor before tripping. The drive looks at DC Bus ripple.
33
rS
Failure to measure stator resistance during auto-tune or when starting in open-loop voltage modes 0 or 3. This is either
because the resistance exceeds the maximum measurable value or no motor connected to drive (see Pr
35
CL.bt
Trip initiated from the control word (see Pr
40-89
t040 -
t089
User trips
90
t090
PLC ladder program attempted divide by zero
91
t091
PLC ladder program attempted access to non-existent parameter
92
t092
PLC ladder program attempted write to a read only parameter
94
t094
PLC ladder program attempted to write a value to a parameter which is out of range
95
t095
PLC ladder program virtual memory stack overflow
96
t096
PLC ladder program invalid operating system call
97
t097
PLC ladder program enabled with no LogicStick inserted or LogicStick removed
98
t098
PLC ladder program invalid instruction
99
t099
PLC ladder program invalid function block argument
100
Drive reset (see Pr
102
O.ht4
Power module rectifier over temperature. Check for supply imbalance. Increase acceleration/deceleration rates.
183
C.dAt
Data does not exist:
An attempt has been made to transfer data from a blank SmartStick or data block that does not exist or verify after write
fail.
185
C.Acc
SmartStick read/write fail:
The drive cannot communicate with the SmartStick either because it is faulty or is not installed in the drive. Removing a
stick during an access will cause this trip.
186
C.rtg
Rating change:
The parameters loaded to the drive from a SmartStick are for a drive of a different voltage or current rating. No rating
dependent parameters have been transferred.
189
O.cL
Overload on current loop input (analog input 1).
199
dESt
Destination parameter clash
200
SL.HF
Solutions Module hardware fault. This could occur because the module cannot be identified, or the module has not
indicated it is running within 5s of drive power-up, or an internal hardware fault has occurred in the module.
201
SL.tO
Solutions Module watchdog timeout. The module has started the watchdog system, but has not subsequently serviced the
watchdog within the timeout period.
Summary of Contents for 2202
Page 199: ......
Page 200: ...0472 0001 09 ...