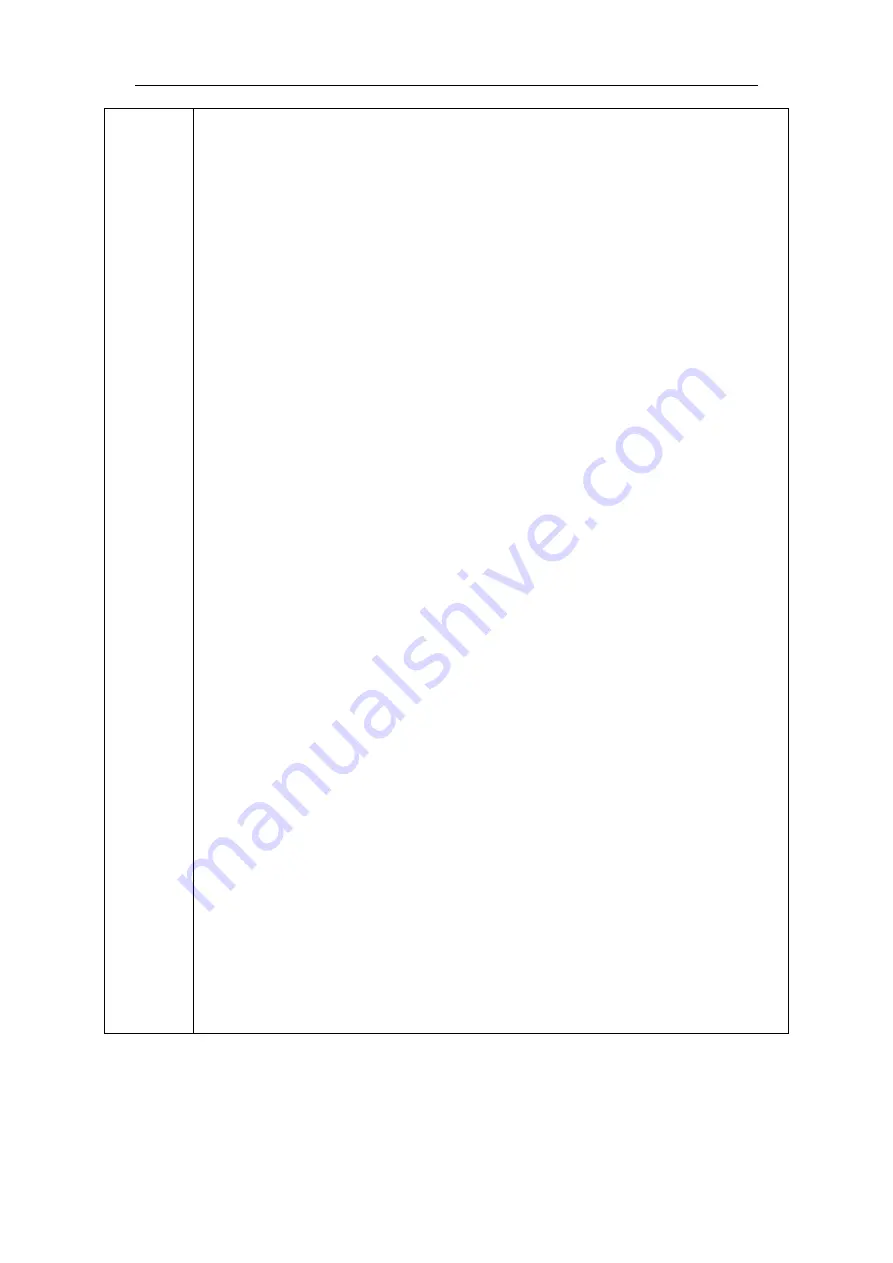
Electrical Operation and Maintenance Manual for ER15-1400 Industrial Robot
12
Therefore, please be cautious do not touch any hot part.
13. Please support the robot arm with proper lifting device before removing any servo
motor of joint axis. The removal causes fail of the brake mechanism of the axis.
Without reliable support, the arm falls. Please be aware same dangers occur if you
press any axis brake release switch on the control cabinet.
14. The robot must remain the same posture before and after the maintenance. Please
record posture data before the replacement of parts.
15. Check and record the location, connector number, installation method, and set data
of the printed circuit board or cable at the beginning of the replacement process, so
they can be recovered properly. The locking mechanism of the connector must be
locked tightly after it is inserted. Never touch the pins of the connector.
16. If compressed air or water is supplied, please cut off the supply source and release
the remaining pressure in pipelines before repair.
17. Please confirm all the protective devices function properly after check and
maintenance.
18. EFFORT will not be liable for any change or modification without authorization.
19. Numerous back-up batteries are built in the robot arm and control cabinet. Misuse
will cause burn, overheat, explosion, eruption, leak, etc. Therefore, the following
protocols must be strictly followed.
•
Only use batteries specified by EFORT;
•
Do not recharge, dismantle, change, or heat batteries;
•
Do not throw batteries in water or fire;
•
Never use surface-damaged batteries the inside of which may be short circuited.
•
Do not use metals, such as wires, to short-circuit the positive and negative
terminals of the battery. Do not discard used batteries in ground garbage that will be
incinerated, landfilled, or dumped. Please pack them in a bag for disposal to prevent
them from being in contact with other metals. Please also handle them properly in
accordance with local regulations.
20. Make sure the emergency stop signal of the auxiliary axis and the emergency stop
circuit of the control cabinet are concatenated when auxiliary axes are added. Then
test the safety functions of the emergency stop circuit to ensure safety control logic.
21. When changing robot parts, be sure to confirm whether the replaced parts match
the original parts, and carefully check the schematic diagram to prevent the wrong
wiring. Otherwise, the components of the robot control cabinet and external
components may be damaged.