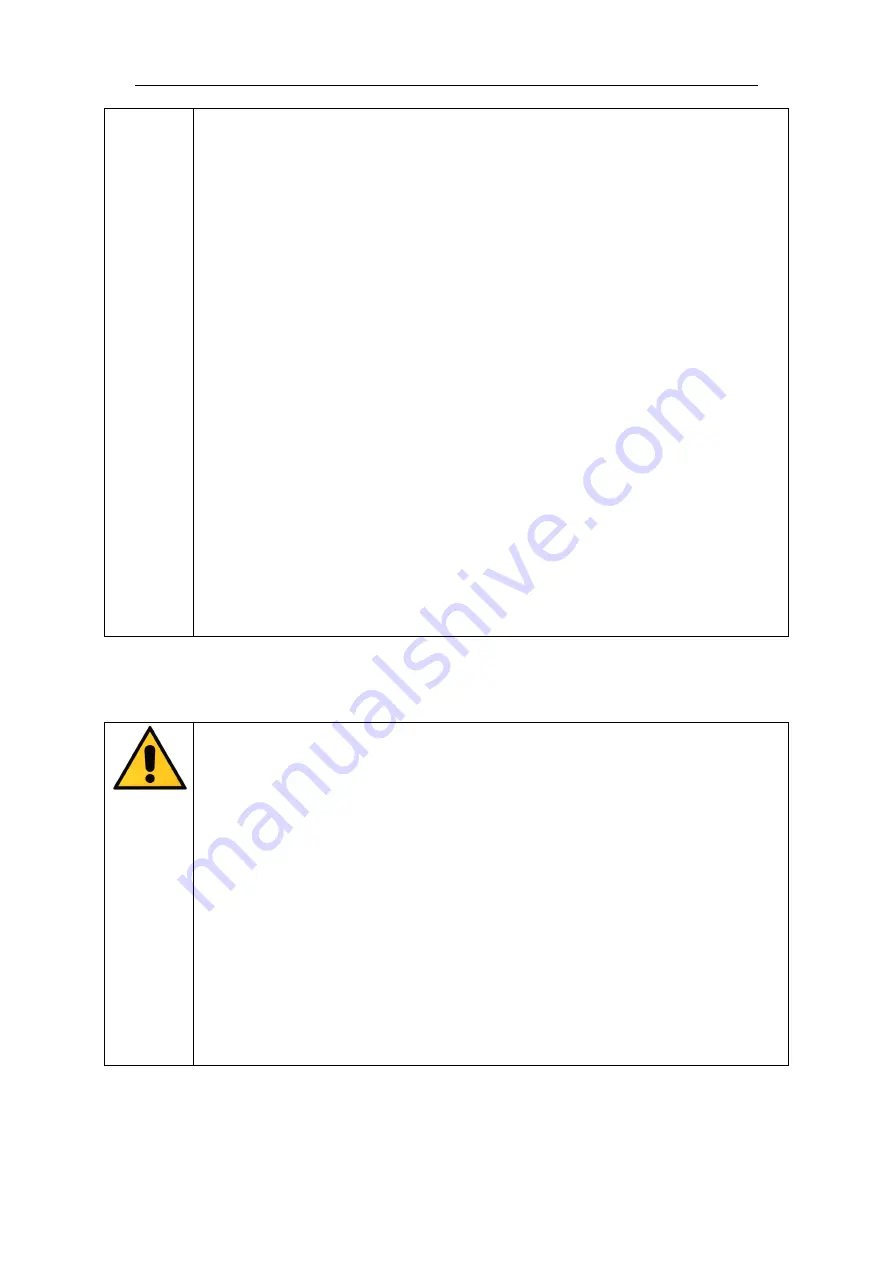
Electrical Operation and Maintenance Manual for ER15-1400 Industrial Robot
6
7. Before activating robot, please reconfirm the following conditions are met.
• Operators on site shall confirm the environment and be trained.
• The installation is correct and stable.
• All the connections in the control cabinet are correct. The power supply specifications
(power supply voltage, frequency, etc.) meet the requirements.
• All the application connections (water, compressed air, protective gas, etc.) are correct
and consistent with the specifications and models.
• The connections to peripheral devices are correct.
• In addition to the installation of software to limit motion, mechanical stop or switch
are also installed to limit robot's motion range.
• If robot is ceased by mechanical limit stop, please make sure the relevant parts are
checked or the invalid mechanical limit stop is replaced (if necessary).
• Safety measures are taken: protective devices, such as safety fences or alarm devices
and interlocking signals, are installed.
• Protective devices and interlock function properly, operators are required to receive
safety training and hold work license.
• Environmental conditions (temperature, humidity, light, noise, dust, etc.) meet the
requirements. In other words, they do not exceed the specifications set for the system
and the robot.
1.3.4 Safety in Robot Test Run
Danger
Errors concerning design, teaching, and working may exist in teaching program,
clamps, logic controllers, and other parts in robot test run. Therefore, safety awareness
must be further enhanced during test runs.
The following procedures need to be paid attention to during the test run:
1. Confirm whether the buttons, switches, and signals to stop the robot, such as the
emergency stop button and hold/run switch, operate properly. Accidents cannot be
prevented if robot cannot be stopped in case of dangerous situations.
2. Set the operating speed to low speed (about 5% to 10%) and confirm the teaching
action during robot test run. Check the operation repeatedly in 2 to 3 cycles. If
problems are detected, stop the robot immediately and make adjustment. Gradually
increase the speed (50%→70%→100%) after no problems are found. Then repeat the
action in 2 to 3 cycles each.