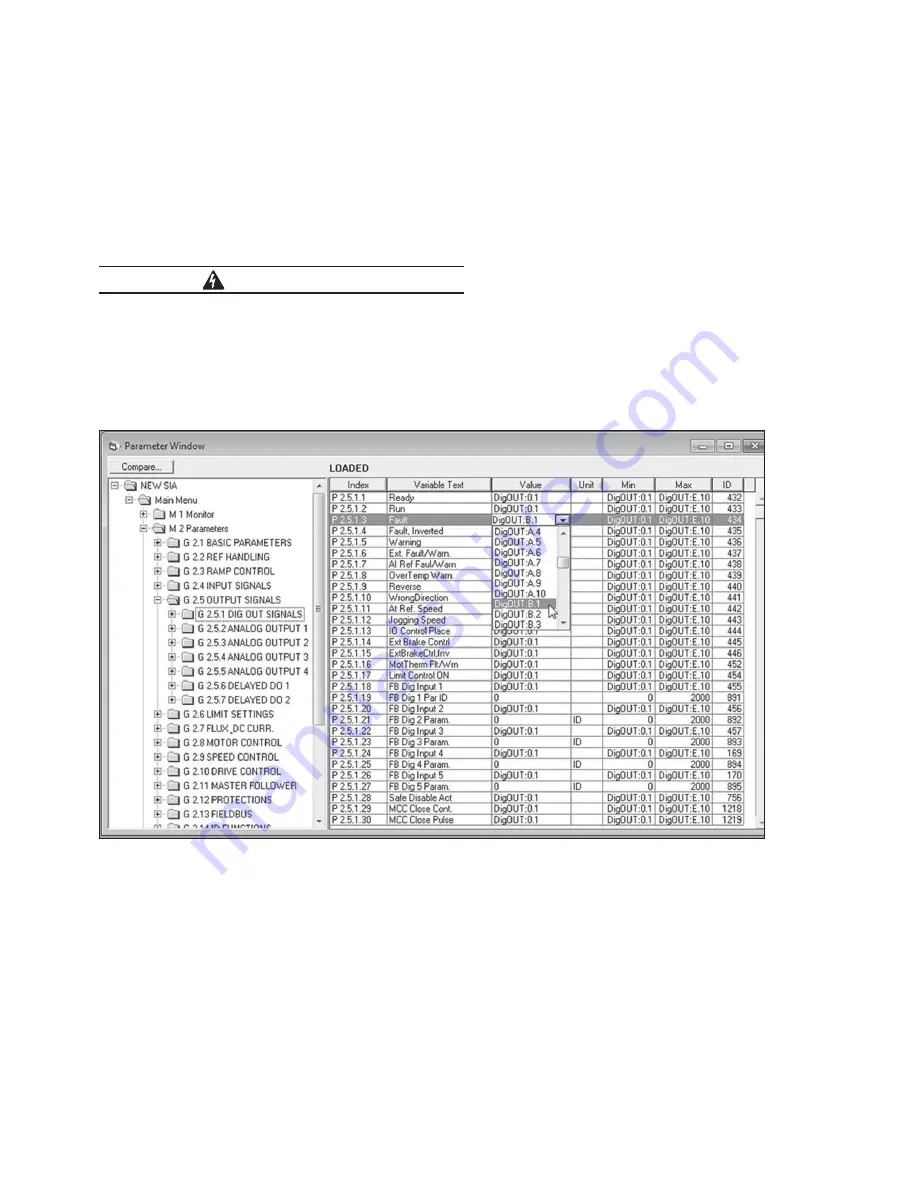
4
“Terminal to Function” (TTF) programming principle
SPX ADVANCED APPLICATION MANUAL
SVCH0203—October 2017 www.eaton.com
2.2 Defining a terminal for a certain function
with 9000xDrive programming tool
If you use the 9000xDrive Programming Tool for
parametrizing you will have to establish the connection
between the function and input/output in the same way as
with the control panel. Just pick the address code from the
drop-down menu in the Value column (see below Figure 1).
WARNING
Be ABSOLUTELY sure not to connect two functions
to one and same output in order to avoid function
overruns and to ensure flawless operation .
otee:
N
The inputs, unlike the outputs, cannot be changed in
RUN state.
2.3 Defining unused inputs/outputs
All unused inputs and outputs must be given the board slot
value 0 and the value 1 also for the terminal number. The
value 0.1 is also the default value for most of the functions.
However, if you want to use the values of a digital input
signal for e.g. testing purposes only, you can set the board
slot value to 0 and the terminal number to any number
between 2…10 to place the input to a TRUE state. In other
words, the value 1 corresponds to ‘open contact’ and values
2 to 10 to ‘closed contact’.
In case of Analog inputs, giving the value 1 for the terminal
number corresponds to 0% signal level, value 2 corresponds
to 20%, value 3 to 30% and so on. Giving value 10 for the
terminal number corresponds to 100% signal level.
Figure 1 . Screenshot of 9000xDrive programming tool; Entering the address code