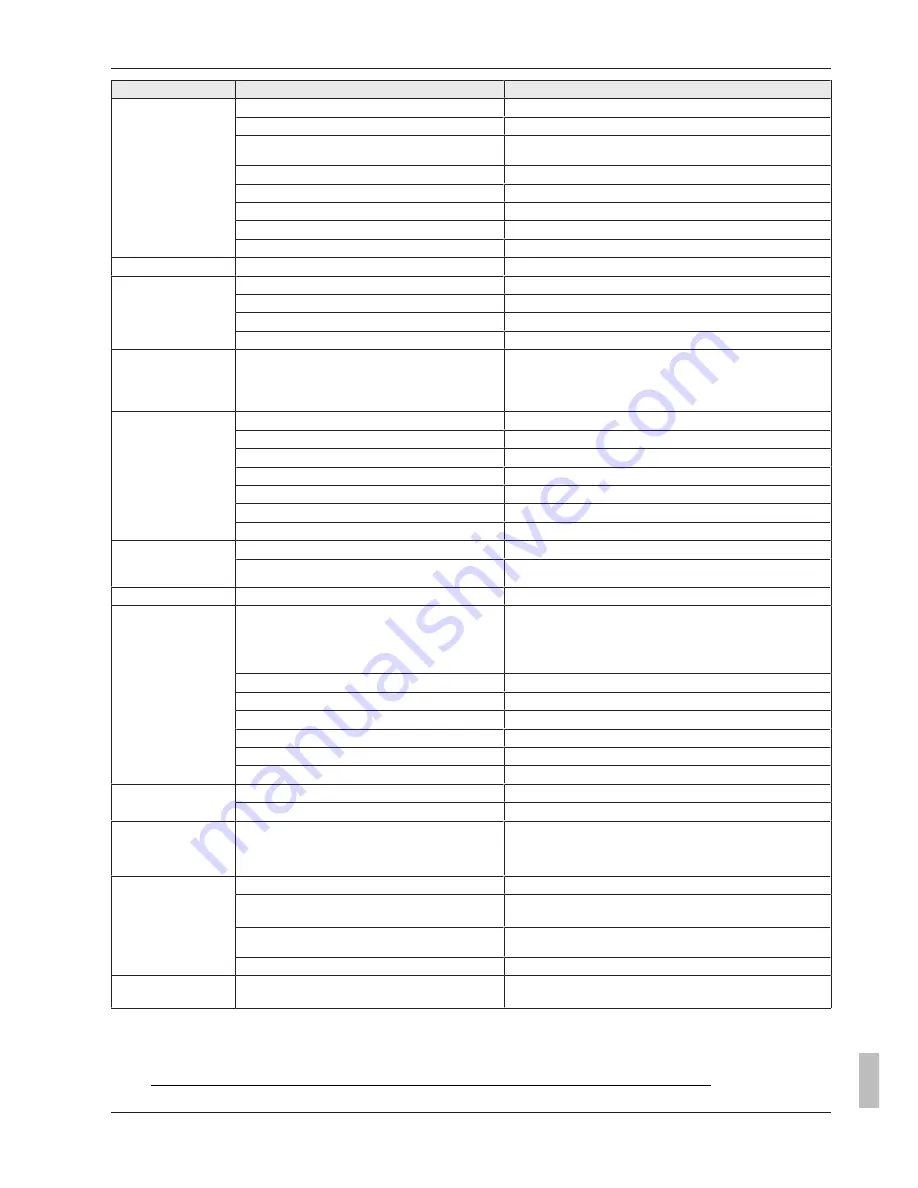
10
Faults and malfunctions
Installation and operating instructions
51
Daikin/ROTEX A2 F
Oil condensing boiler A2 F
008.1546499_02 – 04/2018 – EN
Malfunction
Possible cause
Possible solution
No ignition
Ignition electrodes short circuited
▪ Check the ignition electrodes, adjust or replace as required.
Distance of ignition electrodes too large
▪ Check the ignition electrodes and adjust as required.
Ignition electrodes contaminated or humid
▪ Clean the ignition electrodes and check the oil nozzle burner
settings.
Ignition electrodes burnt out
▪ Replace the ignition electrodes.
Insulating body cracked
▪ Replace the ignition electrodes.
Ignition transformer defective
▪ Replace the ignition transformer.
Ignition cable defective, sparking
▪ Replace the ignition cable and determine the cause.
Automatic firing unit faulty
▪ Replace the firing unit.
Loud operating noises
Bearing damage on the burner fan
▪ See "Loudly whistling mechanical noise" fault.
Loudly whistling mech-
anical noise
Burner blower bearing defective
▪ Replace the burner blower.
Oil pump is suctioning air
▪ Check the bolting
Vacuum in the oil line too high
▪ Clean the filter, open the valves fully.
Oil pump defective
▪ Change the oil pump
Disturbing circulation
noises
Pump pressure too high
Badly balanced heat distribution system
▪ Throttle maximum pump output (reduce the setting of the
[Max Perform Pump] parameter gradually – not below 65%).
(9)
▪ Carry out hydraulic balancing.
Oil pump does not
pump any oil
Shut-off valve on the oil filter or in suction line closed ▪ Open the check valve.
Gearbox oil pump damaged
▪ Change the oil pump
Suction valve has leakage
▪ Clean/change the suction valve.
Oil line has leakage (pump sucks air)
▪ Check and seal the screw connection.
Filter clogged
▪ Clean the filter.
Filter not leakproof
▪ Replace the filter.
Oil pump power insufficient
▪ Replace the oil pump.
Oil atomisation not uni-
form - heavy soot de-
position in flame tube
Oil nozzle loose, clogged or worn
▪ Check/tighten/change the oil nozzle.
Oil nozzle spraying angle is wrong
▪ Replace the oil nozzle.
No oil passage
Oil nozzle clogged
▪ Replace the oil nozzle.
Mixer device has thick
oil layer or heavy car-
bon deposition
Insufficient air supply
▪ Check the supply air line for blockage.
▪ Use the supply air line with a larger cross-section.
▪ Room air-dependent operation: Check the supply air opening
(min. 150 cm
2
non-wearing supply air opening).
Air supply line contaminated/clogged
▪ Clean the air supply line.
Flue gas conduit of the LAS has leakage
▪ Seal the flue gas conduit, replace the gasket.
Burner setting wrong.
▪ Check/correct the burner setting.
Oil nozzle incorrectly dimensioned
▪ Check/change the nozzle type.
Combustion air quantity wrong
▪ Measure the blower pressure, correct the burner setting.
Air in suction line (leakage)
▪ Seal the suction line.
Solenoid valve on the
oil pump does not open
Coil defective
▪ Change the coil
Automatic firing unit faulty
▪ Replace the firing unit.
Flame monitoring does
not respond
Flame monitoring cable defective or bad plug con-
nection
▪ Replace the flame monitoring cable.
▪ Check plug connection X2 on the firing unit.
▪ Check the 3-pin plug connection on the ignition transformer.
STB switch-off
Water throughput too low due to air inclusion
▪ Vent the system.
Water flow too low due to valves closing too quickly
in the entire heating network
▪ Use slow closing or timed valves; install an overflow valve if
necessary.
Pump down
▪ Check the mains and PWM control signal connection, replace
the pump if necessary.
Water throughput too low due to air inclusion
▪ Vent the system.
Flue gas temperature
sensor switch-off
Flue gas temperature too high
▪ Clean the boiler.
Tab. 10-1
Possible faults on the A2 F
(9)
see "RoCon BF" controller documentation