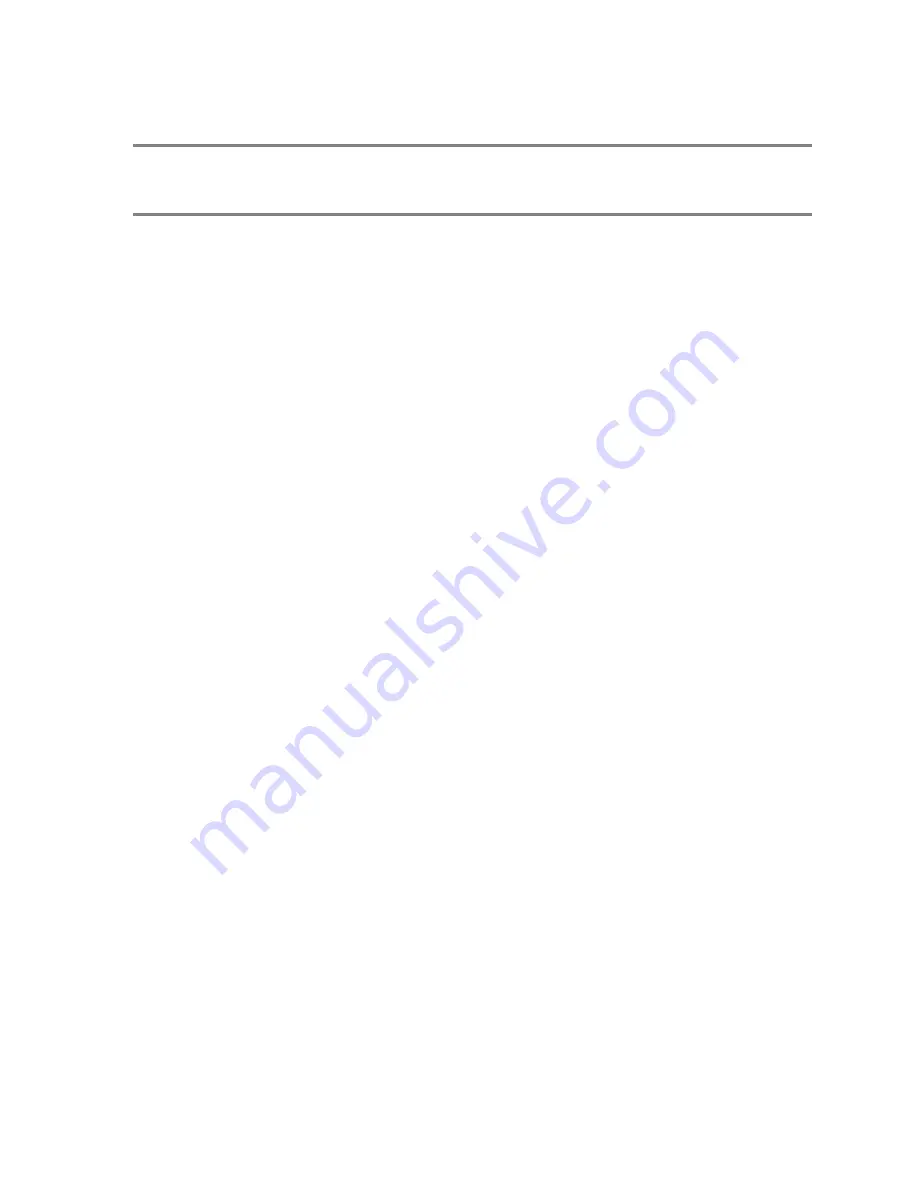
CTI 2572-A Installation and Operation Guide V1.3
113
APPENDIX F. Updating Firmware
Overview
The 2572-A stores all firmware in flash memory. This allows the firmware to be upgraded in the
field, eliminating the need to replace physical PROMS. There are two types of firmware used with the
2572-A, the application firmware and the boot loader firmware.
The application firmware performs all of the primary module functions, including the PLC server,
PLC client, and Web server tasks. When new features are added to the module, the application
firmware will change.
The bootloader is a small section of code that performs module startup functions (including DHCP)
and manages the firmware download functions. Because most of the bootloader functions are generic,
it may not change when new functions are added.
When you are upgrading the 2572-A module firmware, you must choose which type of firmware you
are downloading. During the download process, the firmware will be checked to ensure that it is the
correct type and that it is compatible with the version of the 2572-A hardware you are using.
Update Preparation
Obtain TFTP Server Software
The 2572-A module uses the Trivial File Transfer Protocol (TFTP) to copy the firmware files from a
hard drive to the module. The module will need network access to a TFTP server, which is a small
program that can run on your local PC.
TFTP servers are available for free download from several sources. One such source is Solar Winds,
a provider of network analysis software. Point your browser to:
http://support.solarwinds.net/updates/SelectProgramFree.cfm#
to access the download page. Once
you have installed the TFTP software on your PC, start the TFTP server and set the TFTP root
directory. You will place the new firmware files in the directory.
Obtain New Firmware
2572-A firmware may be downloaded from the following URL:
ftp://www.controltechnology.com/public/Download/2572A/
The firmware is stored as a self extracting zip file. See the readme file in the download directory or
contact your CTI support representative for the name of the file to download. After downloading the
applicable file(s) to a folder on your hard drive, run the program. This will extract several files to the
target directory you select. Make sure these file are placed in the root directory of the TFTP server.
Summary of Contents for 2572-A
Page 8: ......
Page 16: ......
Page 28: ......
Page 32: ......
Page 60: ......
Page 84: ......
Page 96: ......
Page 104: ...CTI 2572 A Installation and Operation Guide 96 WX WY Quick Reference...
Page 112: ......
Page 116: ......
Page 126: ......
Page 130: ...CTI 2572 A Installation and Operation Guide 122 WX WY Quick Reference...