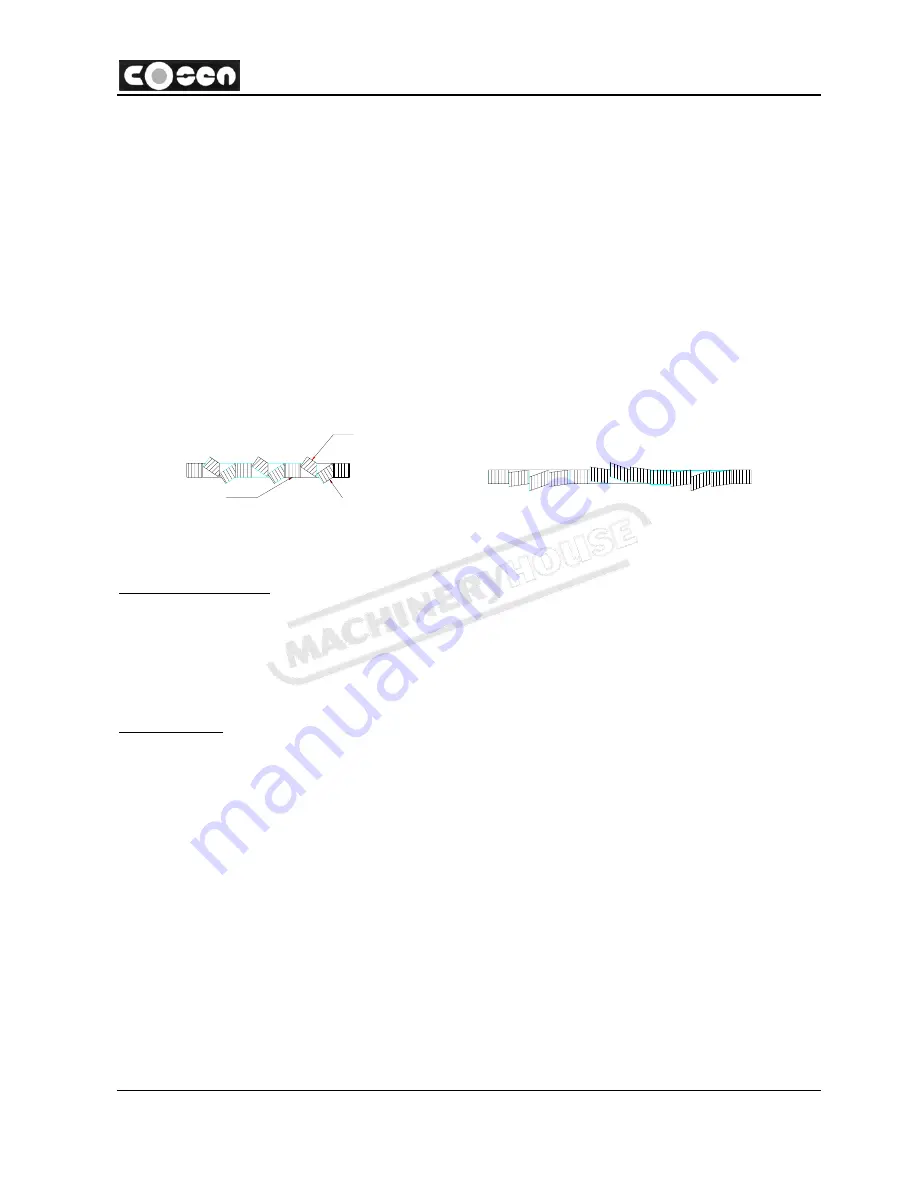
BAND SAW CUTTING - A PRACTICAL GUIDE
Section 7
7-2
It will be slower to cut tubing than to cut solids, because the blade must enter the material
twice, and because coolant will not follow the blade as well.
Tough or abrasive materials are much harder to cut than their machinability rating would
indicate.
Tooth spacing is determined by the hardness of the material and its thickness in cross section.
Tooth set prevents the blade from binding in the cut. It may be either a "regular set" (Also
called a "Raker Set" ) or a "Wavy Set".
The regular or raker set is most common and consists of a pattern of one tooth to the left. Set
to the right, to the left and one which is straight, or unset. This type of set is generally used
where the material to be cut is uniform in size and for contour cutting.
Wavy set has groups of teeth set alternately to right and left, forming a wave-like pattern.
This reduces the stress on each individual tooth, making it suitable for cutting thin material or
a variety of materials where blade changing is impractical. Wavy set is often used where
tooth breakage is a problem. This is shown in Fig. 7.1 as follows:
Right
Straight
Left
Regular (raker) Set
Way Set
Fig. 7.2 The saw set
Blade Speed and Feed:
Blade speed is generally limited by vibration and the ability to keep the blade sufficiently cool to
avoid dulling the teeth. A blade which is running fast and taking a very light cut will dull quickly
because the tips of the teeth will overheat from the rubbing action. If, however, we force the
blade teeth deeper into the material, the blade will be less sensitive to heat, because the teeth are
cutting more and rubbing less.
Blade selection:
There are five types of blade material generally used:
•
Hard-back
carbon
•
Semi-high
speed
•
High
speed
•
Carbon
•
Electron-welded
blade
In most high speed production cutting either the semi-high speed or the electron-welded band are
used. Electron welded blade is the best blade. But it is also the most expensive. To construct the
electron-welded blade, M-2 tool steel is welded to the blade back. Therefore the blade is capable
of very high surface speed. The semi-high speed blade is used more in structural because it is
capable of taking a great deal more abuse. The hard-back carbon blade's teeth does not have red-
hardness but if the blade is run slowly it can be very economical. We do not recommend carbon
blades because the back of the blade is not sufficiently strong to stand adequate tension and
because it has poor resistance to heat and abrasion. Usually, the coarse hook tooth blade will give
better results, but accurate feed control is a must with a coarse tooth blade.
Page 75
Instruction Manual for AH-250H (B040)
04/12/2014
Summary of Contents for AH-250H
Page 7: ...Section 1 SAFETY RULES Page 7 Instruction Manual for AH 250H B040 04 12 2014 ...
Page 13: ...Section 2 GENERAL INFORMATION Page 13 Instruction Manual for AH 250H B040 04 12 2014 ...
Page 21: ...GENERAL INFORMATION Section 2 2 8 Page 21 Instruction Manual for AH 250H B040 04 12 2014 ...
Page 22: ...Section 3 MOVING INSTALLATION Page 22 Instruction Manual for AH 250H B040 04 12 2014 ...
Page 33: ...Section 4 OPERATION INSTRUCTION Page 33 Instruction Manual for AH 250H B040 04 12 2014 ...
Page 56: ...Section 5 ELECTRICAL SYSTEM Page 56 Instruction Manual for AH 250H B040 04 12 2014 ...
Page 69: ...Section 6 HYDRAULIC SYSTEM Page 69 Instruction Manual for AH 250H B040 04 12 2014 ...
Page 79: ...Section 8 MAINTENANCE SERVICE Page 79 Instruction Manual for AH 250H B040 04 12 2014 ...
Page 84: ...Page 84 Instruction Manual for AH 250H B040 04 12 2014 ...
Page 85: ...Section 9 SYSTEM TROUBLE SHOOTING Page 85 Instruction Manual for AH 250H B040 04 12 2014 ...
Page 93: ...Section 10 PART LIST Page 93 Instruction Manual for AH 250H B040 04 12 2014 ...