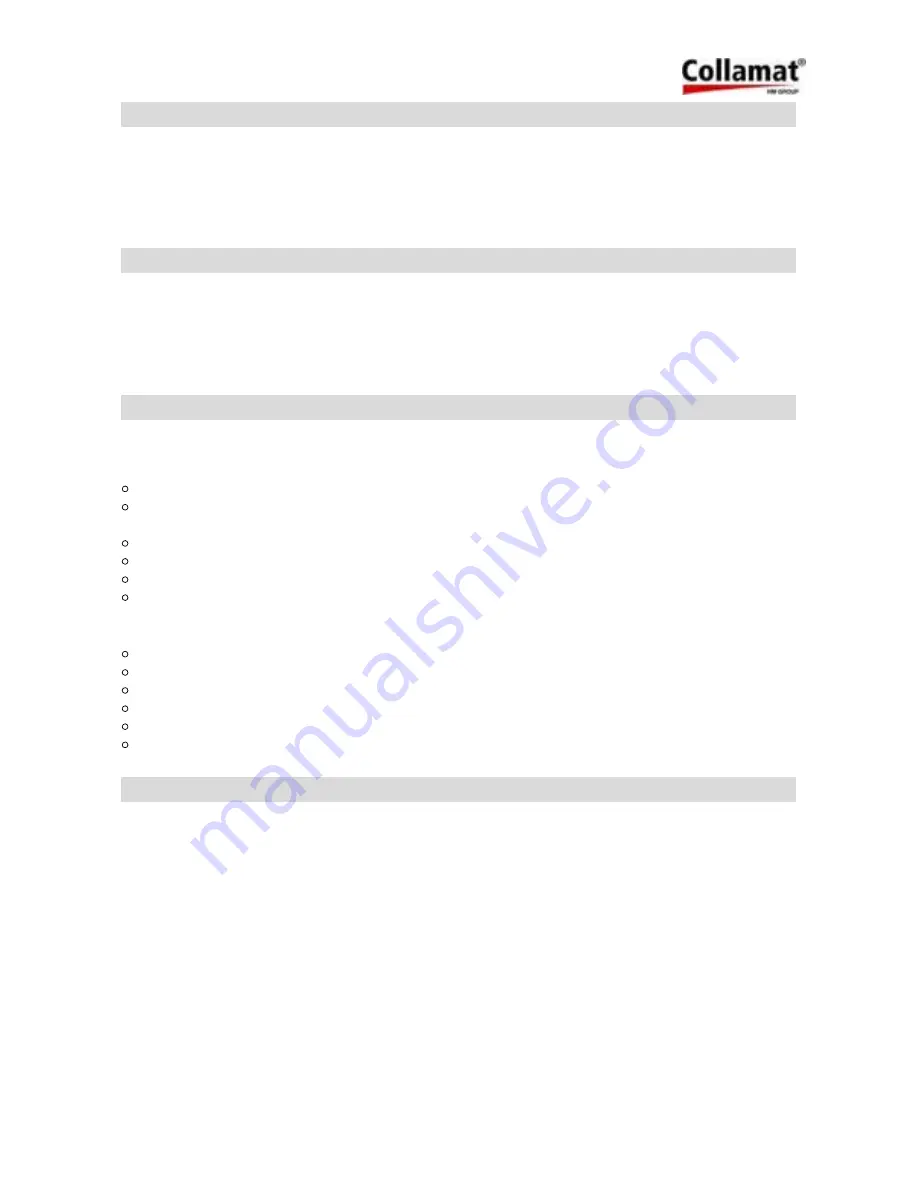
Error #7 No LSC-adjust
Cause:
Adjustment of label scanner not possible. The scanner is defective or it is scanned on label in-
stead of gap, or the backing paper is not transparent enough.
Solution:
Shift gap under label scanner and adjust it again. Possibly exchange defective scanner.
Error #8 Nonstopmode
Cause:
One of the labellers has an error. The nonstop mode does not function correctly. The error can
be triggered by all error messages.
Solution:
Eliminate the error on the labeller.
Nonstop reset at both monitors
.
Error #9 Label too long
Cause:
A leading label edge could not be scanned within the entered label length. The cause of this er-
ror can be as follows:
Missing labels on the paper web
Slippage of the traction unit or loss of steps of the stepper motor due to hits on the paper
web or too high frictional force
Value of label length is entered too short
Predispensing greater than label length
Value of label length shorter than suppression of label scanning
Error of label scanning
Solution:
The following items may be helpful:
Enter in general double or three times the value of the label length
Correct predispensing
Adjust suppression of label scanning
Check label scanner and possibly clean it
Use unwinder with double dancer roller
Reduce friction force of entire paper web
Error #10 LSC Counter
Cause:
When braking the label, a gap was detected during predispensing. This happens in the case of
transparent or very reflective labels.
Solution:
Adjustment of suppression of label scanner
Optimizing the positioning of label scanner
Optimizing the label scanner sensitivity
5999.530-01F 07.04.2006 WM
47
Summary of Contents for Etiprint Inline
Page 65: ...Etiprint Inline Manufacturer s declaration Register A Manufacturer s declaration...
Page 66: ...Etiprint Inline Manufacturer s declaration 66...
Page 68: ...Etiprint Inline Manufacturer s declaration 68...
Page 69: ...Etiprint Inline Replacement parts Wear parts Register B Replacement parts Wear parts...
Page 70: ...Etiprint Inline Replacement parts Wear parts 70...
Page 74: ...Etiprint Inline Replacement parts Wear parts 74 Draw mechanism spare parts cont...
Page 78: ...Etiprint Inline Electric circuit drawing with printer type SATO...
Page 79: ......
Page 80: ......
Page 82: ...Etiprint Inline Electric circuit drawing with printer type ZEBRA...
Page 84: ......
Page 86: ...Etiprint Inline Collamat 8600 9100 Monitor Operating instructions...
Page 87: ...Collamat 8600 9100 Operating instructions Monitor 5999 530 01F...
Page 144: ...Etiprint Inline Collamat 8600 9100 Monitor Technical Manual...
Page 145: ...Collamat 8600 Technical handbook 5999 545 01G...
Page 188: ......