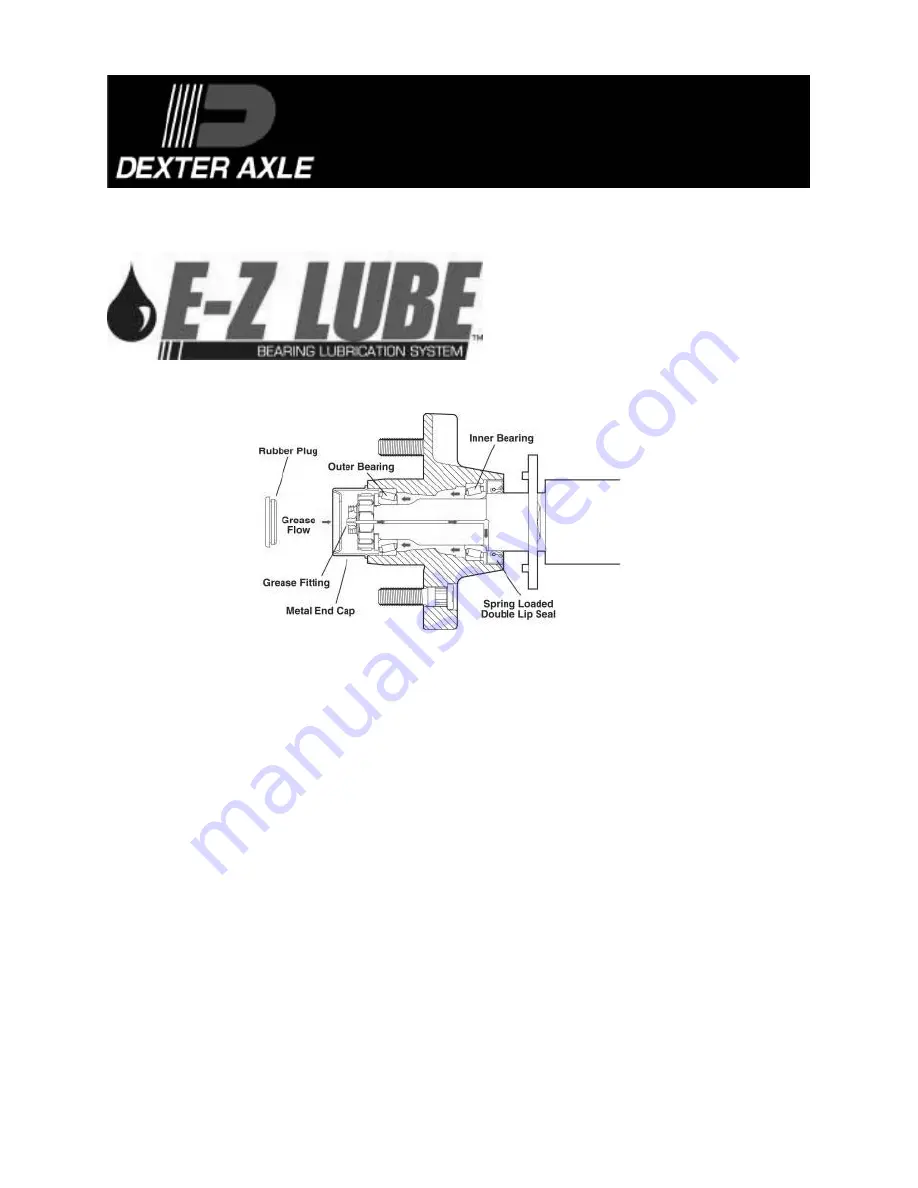
Axles equipped with Dexter's E-Z Lube feature can be periodically lubricated without removing
the hubs from the axle. This feature consists of axle spindles that have been specially drilled and
assembled with grease fittings in their ends. When grease is pumped into the fitting, it is
channeled to the inner bearing and then flows back to the outer bearing and eventually back out
the grease cap hole.
1. Remove the rubber plug from the end of the grease cap.
2. Place a standard grease gun onto the grease fitting located in the end of the
spindle. Make sure the grease gun nozzle is fully engaged on the fitting.
3. Pump grease into the grease fitting. The old, displaced grease will begin to flow
back out the cap around the grease gun nozzle.
4. When the new, clean grease is observed, remove the grease gun, wipe off any
excess, and replace the rubber plug in the cap.
The E-Z Lube feature is designed to allow immersion in water. Axles not equipped with E-Z
Lube are not designed for immersion and bearings should be repacked after each immersion. If
hubs are removed from an axle with an E-Z Lube feature, it is imperative that the seals be
replaced before bearing lubrication. Otherwise, the chance of grease getting on brake linings is
greatly increased.
NOTE: The convenient lubrication provisions of the E-Z Lube must not replace periodic inspection of the
bearings.
Summary of Contents for 1712
Page 2: ......
Page 4: ......
Page 5: ...12 CHIPPER SAFETY ALERT ...
Page 6: ......
Page 7: ...12 CHIPPER SAFETY ALERT ...
Page 8: ......
Page 9: ...12 CHIPPER SAFETY ALERT ...
Page 10: ......
Page 11: ...12 CHIPPER SAFETY ALERT ...
Page 12: ......
Page 13: ...12 CHIPPER SAFETY ALERT ...
Page 14: ......
Page 15: ...12 CHIPPER SAFETY ALERT ...
Page 16: ......
Page 17: ...12 CHIPPER SAFETY ALERT ...
Page 18: ......
Page 20: ......
Page 22: ......
Page 24: ......
Page 26: ......
Page 91: ...12 CHIPPER STEIN MFG PTO CLUTCH Depending on engine selection 65 ...
Page 153: ......
Page 156: ......
Page 158: ......
Page 159: ...CONTACT STEIN MANUFACTURING FOR PARTS ...
Page 160: ...CONTACT STEIN MANUFACTURING FOR PARTS ...
Page 161: ...WINCH INFORMATION ...
Page 162: ...WINCH INFORMATION ...
Page 163: ...WINCH INFORMATION ...
Page 164: ......