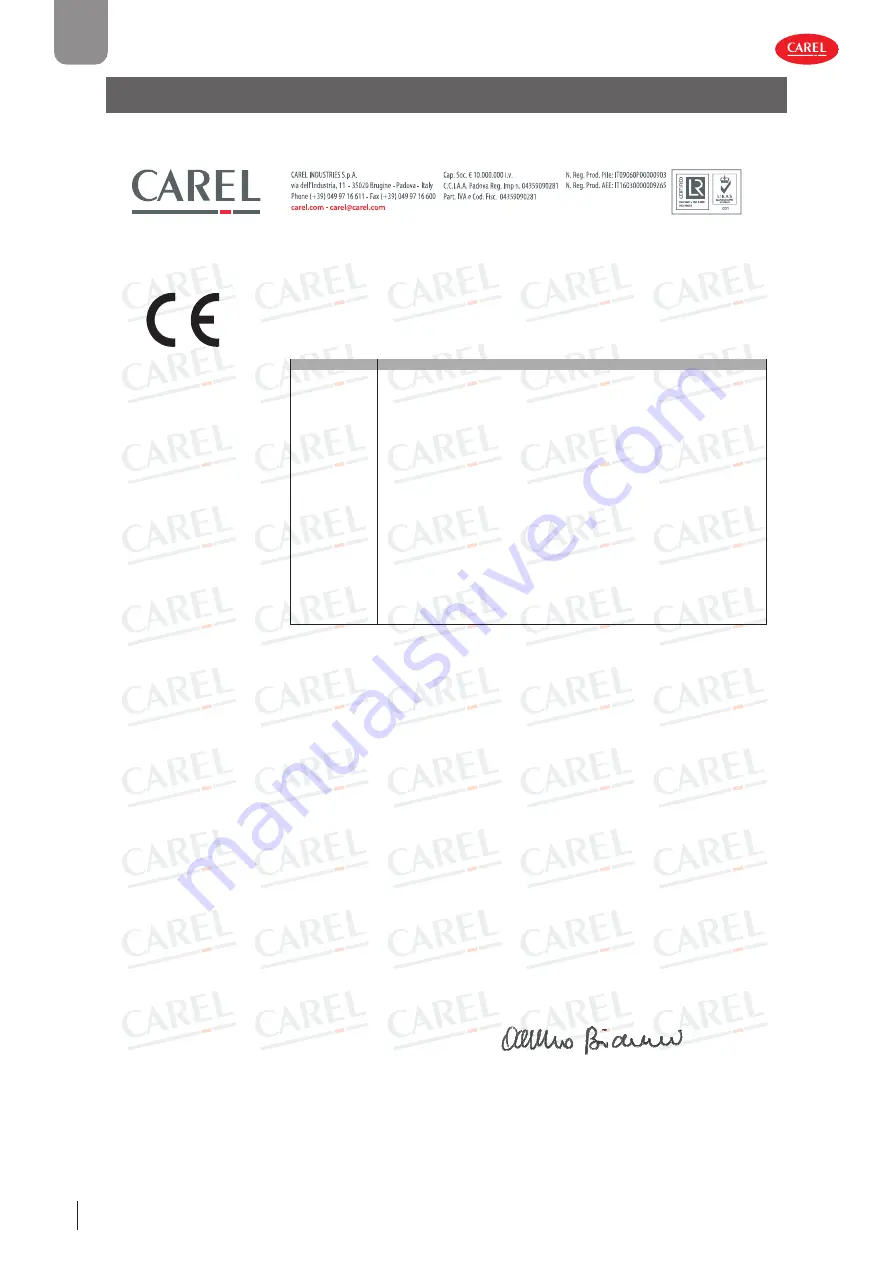
126
zϳϱϵͺϬϭͺh'ͺ;ĞǀŽůƵƚŝŽŶͿͺĚƚĚ͘ĚŽĐdž
(8'HFODUDWLRQRI&RQIRUPLW\
7KLVGHFODUDWLRQRIFRQIRUPLW\LVLVVXHGXQGHUWKHVROHUHVSRQVLELOLW\RIWKH
PDQXIDFWXUHU
&$5(/,QGXVWULHV6S$
9LDGHOO¶,QGXVWULD%UXJLQH3',WDO\
*D6WHDP*DVILUHGKXPLGLILHUV
&RGH
'HVFULSWLRQ
8*DDDE'FG
*D6WHDP(YROXWLRQ*DVILUHGKXPLGLILHUV
D
E
F
G
6WHDPSURGXFWLRQ
NJK
NJK
NJK
NJK
NJK
NJK
0RGHO
+
LQGRRU
<
RXWGRRU&WR&&WR&ZKHQXVHGLQFRQMXQFWLRQZLWK
KHDWHUNLW&DUHO8*.+.:639N:
6XSSO\YROWDJHIUHTXHQF\
+]
&XVWRPL]DWLRQRSWLRQV
VWDQGDUGYHUVLRQ
/HWWHUVQXPEHUV
FXVWRPL]DWLRQLGHQWLILFDWLRQ
7KHREMHFWRIWKHGHFODUDWLRQGHVFULEHGDERYHLVLQFRQIRUPLW\ZLWKWKHUHOHYDQW8QLRQ
KDUPRQLVDWLRQOHJLVODWLRQ
5HJXODWLRQ
(8
*$5
'LUHFWLYH
(8
/9'
'LUHFWLYH
(8
(0&'
*$5
(1$(1$
(0&
(1(1(&(1$
(1$(1(1
/9'
(1(1
7KHQRWLILHGERG\'9*:&(57*PE+-RVHI:LUPHU6WUDH%RQQ*HUPDQ\SHUIRUPHGDSURFHGXUHIRU
(8W\SHH[DPLQDWLRQRIWKHPRGHOVOLVWHGDERYHDQGLVVXHGWKHFHUWLILFDWH&(%0GDWHGYDOLG
WLOORQWKHEDVLVRIUHVXOWVRI(8UHSRUWRIH[DPLQDWLRQ*%7*%%DQG*%
%LVVXHGE\7895KHLQODQG
%UXJLQH
WK
)HEUXDU\
6LJQHGIRUDQGRQEHKDOIRI
&$5(/,1'8675,(66S$
,QJ$OEHUWR%LDQFKL
*URXS&KLHI5HVHDUFK 'HYHORSPHQW2IILFHU
ENG
conformity
g0300122EN rel. 1.0 - 01.12.2021
20. CONFORMITY