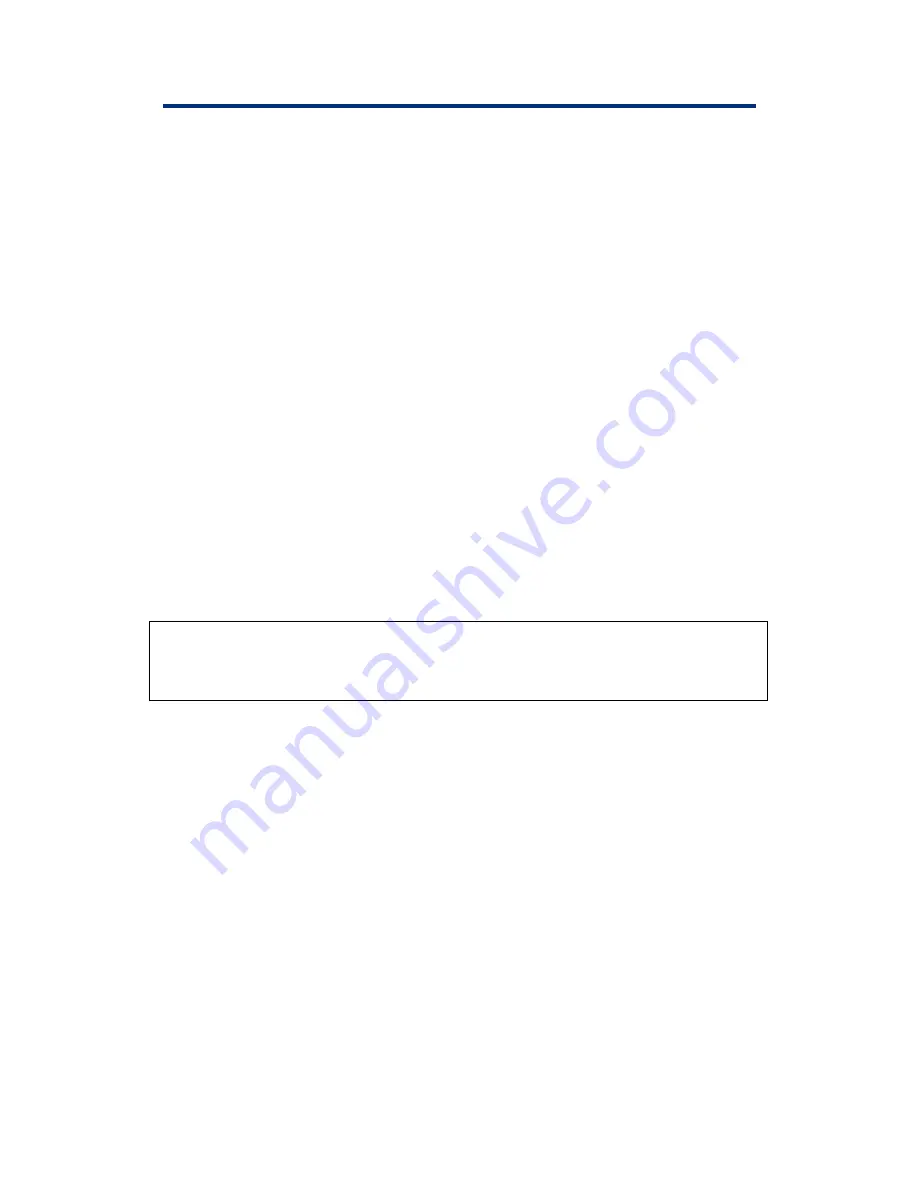
TCi Operator Manual
105
Errors in effusivity and conductivity measurements have four significant sources: variations in the
tested material, quality of contact between sensor and tested material, errors from equipment and
errors from calibration (offset only).
9.7.2 Material
Variations in tested material will change the heat transfer characteristics. A good example is
humidity content in powders. Water has much higher effusivity than most powders, and therefore
change in humidity content will drastically change the measured effusivity and conductivity.
Another example is material variation due to ambient temperature. Material variation is not
treated as a measurement error, but rather as the measured characteristic. The user should be
attentive to material variations when considering measured results.
9.7.3 Contact
The quality of contact between the sensor surface and the tested material is critical to having
accurate and repeatable measurements. Powders, liquids and creams usually create a good
contact with the sensor, but it is not always the case with solids.
As indicated earlier, all solids (except for foams) require a contact agent. Water is a good material
and is used between 5
C and 70
C. It normally would create a uniform thin layer, and given its
relative high conductivity, its contribution to variation will be small. The user must be careful to
avoid any air bubbles, as those affect the heat transfer between the sensor and tested material.
Contact agents other than water may vary more, and some errors in the range of a few
percentage points may be expected, specifically at low temperature where the viscosity
increases. The software corrects for the contact quality of the recommended contact agents
(mentioned earlier as CF) whenever they are used.
Note: the surface of the tested material must be smooth. Rough surface finish will create an
affective thick layer of contact agent, and will add to the total error budget.
9.7.4 Equipment
Equipment errors may originate from variations in the current source due to changes in
environment temperature, short term and long term drifts, change in sensor resistance (and
hence supplied power) during the transient measurement and change in sensor resistance (and
hence supplied power) due to initial sensor temperature. Additional errors may come from the
voltage measurement circuitry.
To evaluate the error from the change in sensor resistance during a transient, assume a ~1
degree Celsius change in sensor temperature (~1.0 s transient) for the range of materials used
with the system. The platinum wire of the sensor has a TCR of 0.0037
C
-1
. During the transient,
the sensor resistance changes 0.37%, and the power supplied to the sensor changes by the
same amount. However, since the calibration of the sensor is performed in exactly the same
manner as the measurement of the tested material, this error is calibrated out for most practical
cases, leaving a very small residual error of less than 0.1%.
As mentioned earlier, the power supplied to the sensor is automatically corrected at the beginning
of each sampling, to the extent of the precision of the current source. Additionally, offset errors
due to the effusivity of the sensor are corrected to a large extent, though at low and high
temperatures there will be larger offset error than at room temperature, where calibration is done.
Summary of Contents for TCi
Page 1: ...C Therm TCi Operator Manual TH130041 Rev H...
Page 2: ......
Page 6: ...TCi Operator Manual vi...
Page 53: ...TCi Operator Manual 47 Step 3 Click the Import button...