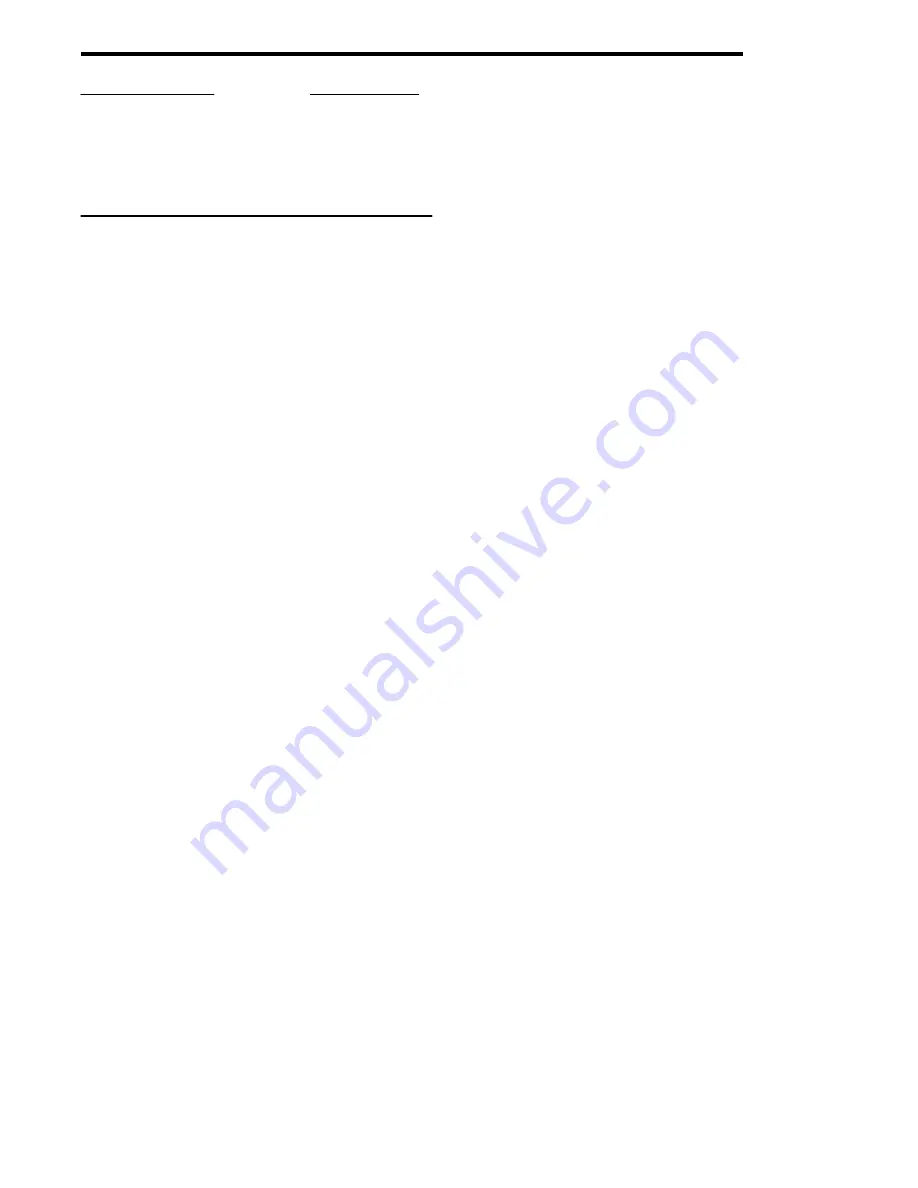
OPERATION
IMPORTANT
If there were 15 Rolls on the Pallet, and the Robotic
Arm action was stopped at the mid point of stacking
Rolls 16 to 20, after the sequence was re-started, and
Rolls 16 to 20 were manually placed on the pallet, it
would be necessary to go to ‘Step Sequence’, and
press the ‘Next’ Pad to add rolls 16 to 20 to the pallet.
If ‘forward travel’ was stopped, after the stacking sequ-
ence was stopped, it may be necessary to ‘manually’
adjust the number of Rolls on the Index Conveyor.
The Rolls will have to be manually re-positioned on the
Index Conveyor because the Index Conveyor will not
move
‘back’
when the Stacking Sequence is stopped.
After the Rolls are positioned correctly on the Index
Conveyor, return to the
‘Step Sequence Screen’
and
use the
‘Up’
and
‘Down Arrows’ Pads
to adjust the
number of Rolls on the Index Conveyor, indicated
‘Plus’
and
‘Minus’
on the Screen.
Use the
‘Up Arrow’ (Plus)
, and the
‘Down Arrow’
(Minus),
to adjust the number of Rolls shown on the
Screen Display, until they match the number of rolls on
the Index Conveyor.
When the number of Rolls on the Screen Display, the
Index Conveyor and the Pallet are the same, the
Stacking Sequence can be re-started.
Restarting the Stacking Sequence.
If the Roll Count was manually adjusted:
•
Press
Pad ‘1’ (OK),
to return to the
Inactive
Stacking Screen.
•
Press
Pad ‘1’ (Start),
to start the stacking
sequence and return to the
Active Stacking
Screen.
•
Resume cutting, and the Stacking Cycle will
continue.
If the Stacking Cycle was stopped after the Robotic Arm
had completed its cycle and returned to the ‘
Home
’
position, over the Index Conveyor:
•
Press
Pad ‘1’ (Start),
on the
Inactive
Stacking
Screen
, to start the Stacking
Sequence and return to the
Active Stacking
Screen.
Partial Pallet
If a ‘partial pallet’ is required, that is a pallet with less
Rolls than the selected stacking pattern, follow the
instructions below for the recommended procedure.
•
When the Rolls required for the ‘partial pallet’
are on the pallet, ‘stop the forward’ travel of
the harvester.
•
Press and
‘Hold’ Pad ‘5’,
for
‘Full Pallet’
Screen, and then proceed normal operation.
Suggestions for better ‘Stacking’.
Brouwer incorporates the latest technology for mobile
equipment, in the electronics and hydraulic systems on
its harvesters, to ensure that the customer has reliable
and user friendly automatic machines.
The operation of the Robomax Harvester is straight-
forward, however, variations in sod rolls and in the local
field conditions, require that the operator is aware at all
times of such variations.
The following suggestions will help the operator to
‘stack’ consistent pallets of sod.
•
The ‘integrity’ of a stacked pallet of sod de-
pends on the consistency and quality of the
sod rolls. Poor quality rolls result in pallets with
low integrity. It is important that the operator
maintains roll consistency and grades the rolls
as they are harvested. Inferior rolls should be
‘ejected’ before the Robotic Arm transfers rolls
to the Index Conveyor.
•
Roll size,(diameter), and their vertical stacking
position on the pallet are related. To stack a
pallet correctly, The Gripper Head should
come ‘down’ to just touch the rolls on the Index
Conveyor, before the Gripper Fingers ‘close’
and grab the rolls. This pick-up height is
adjusted by selecting the correct roll size on
the display screen.
•
Selecting a ‘too small’ roll size commands the
Robotic Arm to compress the rolls as they are
picked from the Index Conveyor and
transferred to the pallet.
Compression of the rolls when being stacked
results in increased cycle times and reduced
efficiency.
•
Selecting ‘too large’ roll size results in the rolls
being ‘dropped’ onto the pallet. This leads to
pallets with less than the desired integrity.
Adjustments can be made to the ‘stacking posi-
tions’. To determine if adjustment is necessary:
•
Harvest at least five pallets of sod, noting the
specific stacking position that may require
adjusting. If the five pallets show the same
stacking inconsistency, stacking position
adjustment is necessary.
Consult your Brouwer Dealer, or the Factory,
for advice on this procedure.
3-09
Summary of Contents for RoboMax
Page 2: ......
Page 4: ......
Page 6: ......
Page 8: ......
Page 17: ......
Page 18: ......
Page 19: ...D001 222 ...
Page 20: ......
Page 22: ......
Page 32: ......
Page 34: ......
Page 44: ......
Page 46: ......
Page 62: ...This page left blank 4 16 ...
Page 63: ......
Page 64: ......
Page 66: ......
Page 76: ......
Page 78: ......