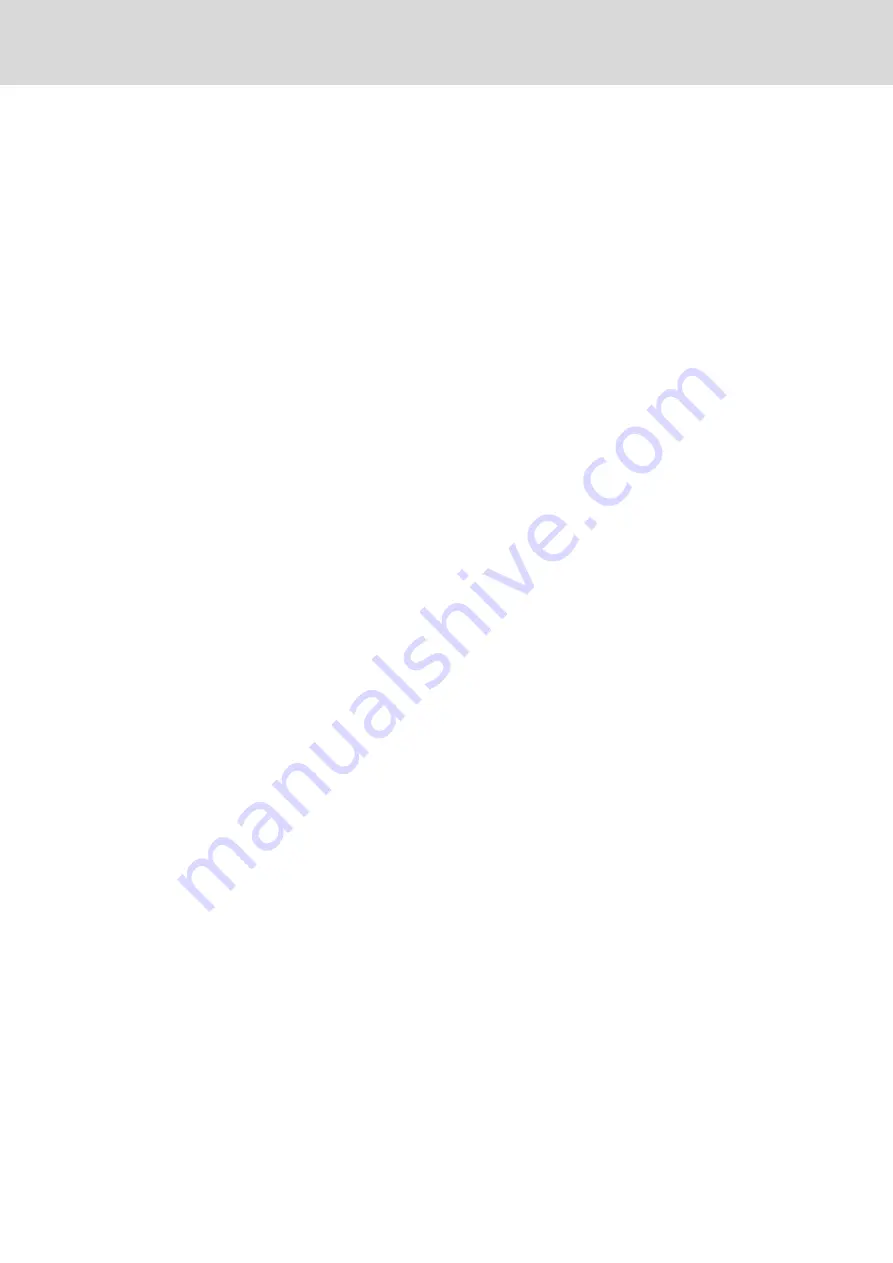
Travel velocity..................................................... 27
Traverse path length........................................... 97
Type codes......................................................... 63
Type designation MCP...................................... 153
Type designation MCS...................................... 154
Type plates............................................... 153, 154
V
Velocity......................................................... 9, 131
Velocity resolution..................................... 127, 128
Vertical axes....................................................... 77
Vertical axis....................................................... 119
Vibrations.......................................................... 110
Voltage constant................................................. 27
W
Warning temperature.......................................... 29
Warnings........................................................... 155
Weight compensation....................................... 119
Winding............................................................... 64
Winding inductivity.............................................. 27
Winding protection.............................................. 90
Winding resistance.............................................. 27
Winding temperature................................. 104, 107
Wire designation................................................. 83
Wire end ferrules................................................. 84
DOK-MOTOR*-MCL********-PR05-EN-P
Bosch Rexroth AG
191/193
Rexroth IndraDyn L Ironless Linear Motors MCL
Index
Summary of Contents for DOK-MOTOR-MCL Series
Page 14: ...Bosch Rexroth AG DOK MOTOR MCL PR05 EN P 12 193 Rexroth IndraDyn L Ironless Linear Motors MCL ...
Page 48: ...Bosch Rexroth AG DOK MOTOR MCL PR05 EN P 46 193 Rexroth IndraDyn L Ironless Linear Motors MCL ...
Page 64: ...Bosch Rexroth AG DOK MOTOR MCL PR05 EN P 62 193 Rexroth IndraDyn L Ironless Linear Motors MCL ...
Page 78: ...Bosch Rexroth AG DOK MOTOR MCL PR05 EN P 76 193 Rexroth IndraDyn L Ironless Linear Motors MCL ...
Page 84: ...Bosch Rexroth AG DOK MOTOR MCL PR05 EN P 82 193 Rexroth IndraDyn L Ironless Linear Motors MCL ...
Page 98: ...Bosch Rexroth AG DOK MOTOR MCL PR05 EN P 96 193 Rexroth IndraDyn L Ironless Linear Motors MCL ...