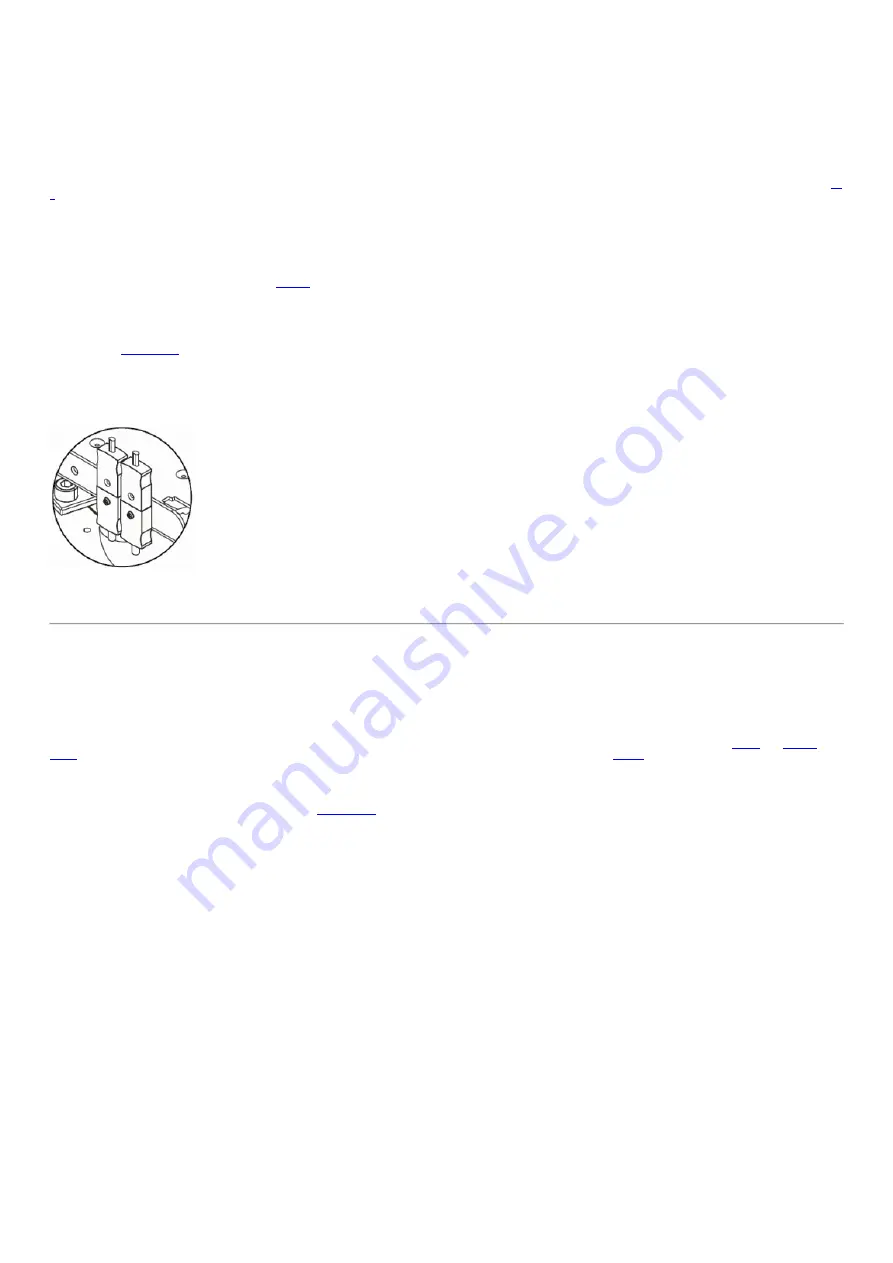
Errors 20, 40, 257 these errors relate to sensor sensors measuring the flow, return and ambient conditions of the appliance. The thermistors should measure 10k Ohms at 25 deg.
C. Check for either open or short circuit; acceptance limits are 32k ohms (0 deg. C) and 230 ohms (140 deg C). These components connect back to the 24 way 'milligrid'*
connector on the MCB.
Error 127 Legionella temperature. The Legionella temperature 65 deg C has not been achieved within the last 48 hours. This is advisory only the appliance will continue to
operate normally. If a large DHW demand coincides with the Legionella period it could stop the cylinder temperature from reaching 65 deg C. Any hour long period at this
temperature will remove the error code whether during a Legionella period or not.
Error 157 the over heat thermostat is normally closed; the opening temperature is 98 + 3 deg C. This is a user reset error but if no reset is possible a permanent open circuit is
implied check for this condition from the connections on the Burner control units (BCUs).
Error 258 this error implies an ambient sensor has over heated inside the appliance, the most likely cause is a faulty seal between the engine and the engine burner. Check the
integrity of the seal and the thermal insulation around both the engine burner and the supplementary heat exchanger. Check that the sensor is held in the correct position see
Error 259 this error implies a sensor on the main PCB has over heated; a user reset should clear the fault once the board has cooled. If the problem reoccurs in the absence of
other associated errors the board should be replaced.
Error 301 Engine Head has overheated if problem persists call for service.
Error 302, 303, 304, 396, 397, 398 and 399, these errors relate to the thermocouples used to monitor the head temperature of the Stirling engine. Check for continuity at the
connector mounted on engine support bracket see
and the milligrid* connection to the board. If the connections are good and a thermocouple is found to be open circuit
replace the thermocouple.
A User reset can only be made when the fault is rectified.
*Note: Continuity from the milligrid connector may be checked by carefully removing the connector and inserting a fine wire (a small resistor leg is ideal) into the corresponding
connection see
Section D
Errors 114 and 158, these errors are associated with looped connections on the 6 way connectors on the BCUs test for continuity in the loops, the main PCB will have to be
replaced if the problem persists.
Fig. AA
page 83
Section E Loss of flame or condensate drain blocked
Perform a user reset if the appliance will not relight, inspect the condensate trap for signs of blockage. If the trap is full remove the bottom connection to see if the water drains.
Rectify the trap/pipe work as necessary.
If the problem does not appear to be related to the condense trap follow the procedure below:
Check that the gas supply is at the correct supply pressure i.e. 2025 mbar, at the gas valve pressure test point and that the gas has been purged through.
Ensure that all joints in the gas train are sound that the silicon air sense tubes are connected from the venturis to the correct gas valve sensing port see
Check all the electrical connections: gas valves, igniters and flame sense for soundness and 'cross' connections. (The wiring harness and components have been designed to
limit the possibility of interconnecting the engine and supplementary ignition circuits, ensure all connections are made before starting any fault finding.)
Repeated 425 error, check and clean air straighteners as in
Do a user reset and check during the ignition cycle for:
NOTE: BCU refers to either of the two burner control units mounted on the main PCB (MCB)
Summary of Contents for ECOGEN 24/1.0
Page 69: ...Fig 77 Fig 78 Fig 79 page 69 16 0 Schematic Wiring 16 1 Burner Control Units BCU Connections...
Page 70: ...page 70 16 2 Milligrid 24 way Connector...
Page 71: ...page 71 16 3 14 way Connector...
Page 72: ...page 72 16 4 Engine Circuit...
Page 73: ...page 73 16 5 Power Monitoring 24Vdc Power Supply...
Page 74: ...page 74 16 6 External Connections External Wiring...
Page 85: ...page 87...
Page 86: ...page 88...
Page 87: ...page 89 Section P...
Page 88: ...page 90...
Page 89: ...page 91 Section Q Engine developing less than 950W after 15 minutes running at maximum rate...
Page 91: ...page 93 page 94 page 95 page 96 MICRO CHP SYSTEM COMMISSIONING CHECKLIST...
Page 92: ...page 97...