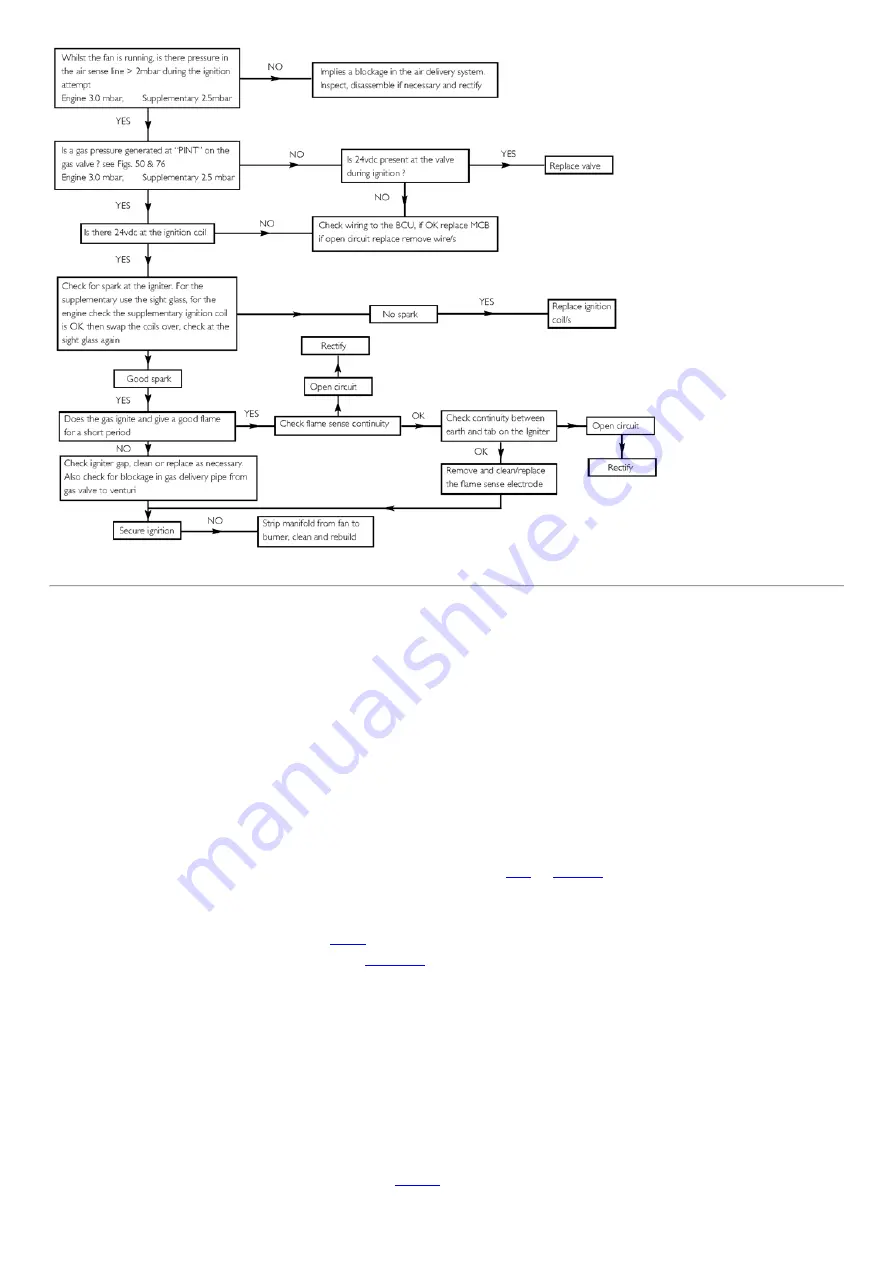
page 84
Section F Burner control and power monitoring
Error codes 263, 264, 394, 395, 422 and 423 are due to communication problems between the main board and the burner control units. If the error does not auto reset power
down, if the error persists replace the PCB.
Error codes 253, 254, 265, 309, 310 and 311 are concerned with grid connection and power monitoring and will require a new PCB if the error persists.
Section G Fan calibration and speed
Check electrical connections to the fan and back to the 14 way connector on the main PCB. Error 267, auto reset power down, if problem persists replace the fan. Error 266,
perform a service reset. If the problem persists replace the fan.
Section H Spool valve calibration
Check electrical connections to the spool valve motor and back to the 14 way connector on the main PCB.
Perform a service reset. If the problem persists down power first then service reset. If the problem persists release the motor from its mounting by undoing the 3 screws and
check to see if the error will reset. If the motor runs free of the spool valve the spool valve may be jammed, if there is no movement replace the spool valve.
Section I Water flow
Error 400: Reverse flow conditions, the return temperature has been less than the boiler flow for 3 minutes. Check the pump flow direction.
On initial commissioning of the appliance check that the flow and return pipes to the system are as in
and
Error 164 shows that the minimum flow rate of 4 l/min has not been achieved after 12 seconds, if after a further 4 minutes the flow switch has still not been closed error 274 will
be displayed. As error 164 is an auto reset if at any time within the 4 minutes the flow switch is closed the appliance operation will be restored. The most likely reason for this
error is air in the system, it is therefore important to purge the system thoroughly. A permanent 164 error indicates that the switch is stuck open.
If the return temperature sensor has not been connected see
Ensure the 3 transit brackets have been removed.
If the pump is not running, check for 230v at Pump Live Check Fuse
Error 428 shows that the flow sensor has not detected 7 L/min, the engine burner will be prevented from running and the appliance will continue to run on the supplementary
only. Check that the automatic by pass has been set up correctly.
Error 270, 278 and 421 are caused by either a rapid rise in temperature or excessive temperature differential across the heat exchanger; either very low flow close to 4 L/min or
air in the system is indicated. Check the wiring back to the main PCB. In either case Check the pump/speed setting and that any isolation valves are open; ensure the system is
purged of air and that there is an adequate bypass.
Section J
Error 284 the water cooled seal thermostat has operated a condition that indicates that the flexible seal connecting the engine to the engine burner is damage or is not in
place. If this not the case check the wiring for continuity back to the 24 way 'milligrid' connector via the 6 way Molex connection see pages 48 and 50. If an open circuit persists
back to either of the thermostats they should be replaced.
Section K
Errors 286 and 289 indicate that the engine has overheated. The engine will take some time to cool down so performing a service reset may not be successful straight away use
one of the thermocouples mounted next to the flow switch to ascertain the stirling head temperature. If the engine appears not to have over heated or the error will not reset check
the engine thermostat circuits through the 6 way Molex connection. See also
.
Section L
Summary of Contents for ECOGEN 24/1.0
Page 69: ...Fig 77 Fig 78 Fig 79 page 69 16 0 Schematic Wiring 16 1 Burner Control Units BCU Connections...
Page 70: ...page 70 16 2 Milligrid 24 way Connector...
Page 71: ...page 71 16 3 14 way Connector...
Page 72: ...page 72 16 4 Engine Circuit...
Page 73: ...page 73 16 5 Power Monitoring 24Vdc Power Supply...
Page 74: ...page 74 16 6 External Connections External Wiring...
Page 85: ...page 87...
Page 86: ...page 88...
Page 87: ...page 89 Section P...
Page 88: ...page 90...
Page 89: ...page 91 Section Q Engine developing less than 950W after 15 minutes running at maximum rate...
Page 91: ...page 93 page 94 page 95 page 96 MICRO CHP SYSTEM COMMISSIONING CHECKLIST...
Page 92: ...page 97...