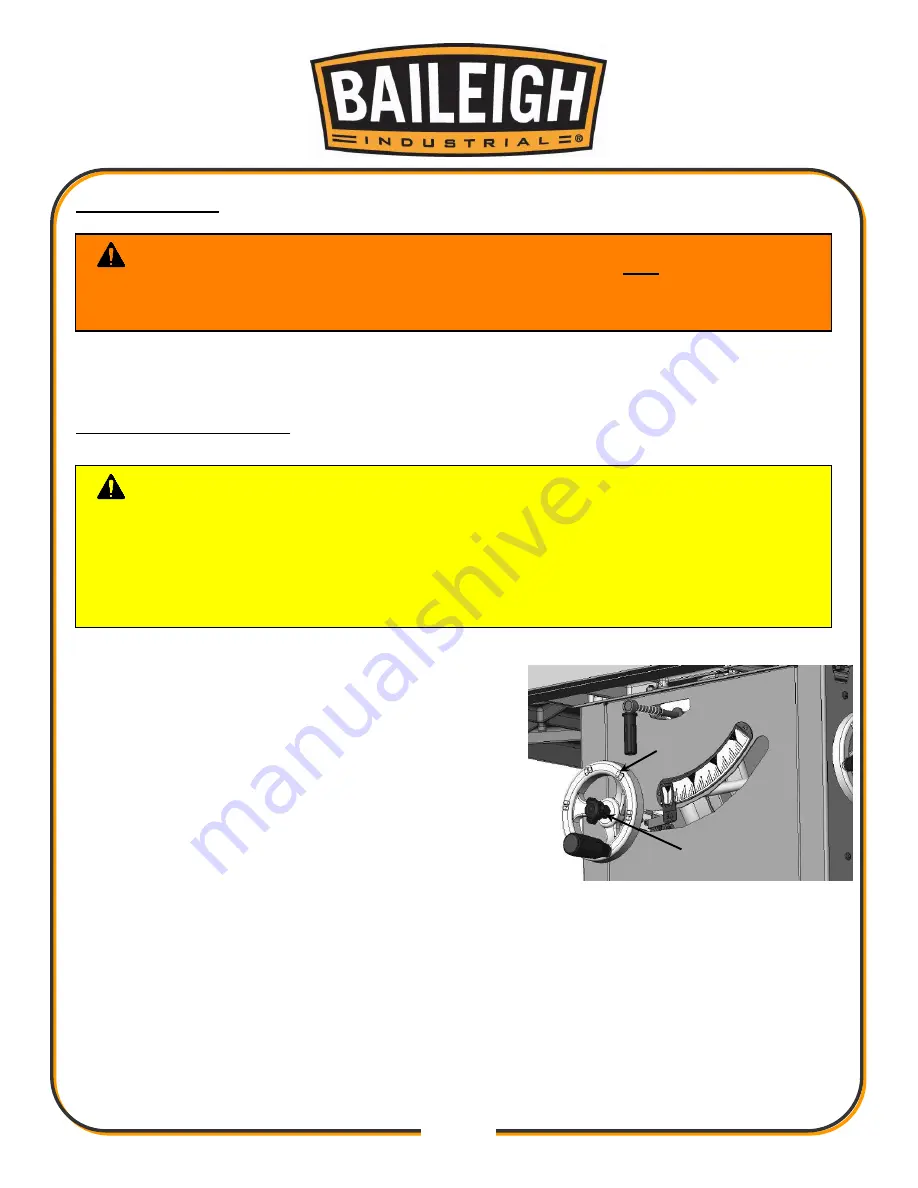
52
52
ADJUSTMENT
Before operation, the machine should be carefully adjusted for best performance.
Blade Height Adjustment
The blade height adjustment handwheel is located on
the front of the saw and there is a lock knob on the
handwheel that allows you to lock the wheel and
secure the blade at the desired height.
To raise or lower the blade:
1. Loosen the blade height lock knob by turning
counter clockwise.
2. To raise the blade: Turn the handwheel clockwise.
To lower the blade: Turn the handwheel counter
clockwise.
3. With the blade set to the desired height, tighten the lock knob by turning clockwise to lock
the blade.
WARNING:
Make sure the electrical disconnect is OFF before working on
the machine.
Always follow proper safety precautions when working on or around any machinery.
CAUTION:
To limit your exposure to the blade and maximize the
effectiveness of the anti-kickback pawls (when using the riving style splitter & blade
guard), never take more blade height than is required to complete the cut. When
setting the blade height for through-cuts (cuts all the way through the thickness of a
board) set the height of the blade to roughly 1/4" higher than the thickness of the
board.
Summary of Contents for TS-1248P
Page 4: ...52 Saw Body Parts List A B 94...
Page 81: ...77 77 ELECTRICAL DIAGRAM...
Page 82: ...78 78 ELECTRICAL CONNECTIONS...
Page 83: ...79 79 BLADE GUARD MITER AND ACCESSORIES PARTS DIAGRAM A A...
Page 86: ...82 82 FENCE PARTS DIAGRAM...
Page 89: ...85 85 52 EXTENSION TABLE AND RAILS PARTS DIAGRAM...
Page 91: ...87 87 SAW BODY PARTS DIAGRAM A...
Page 92: ...88 88 SAW BODY PARTS DIAGRAM B...
Page 103: ...99 99 NOTES...