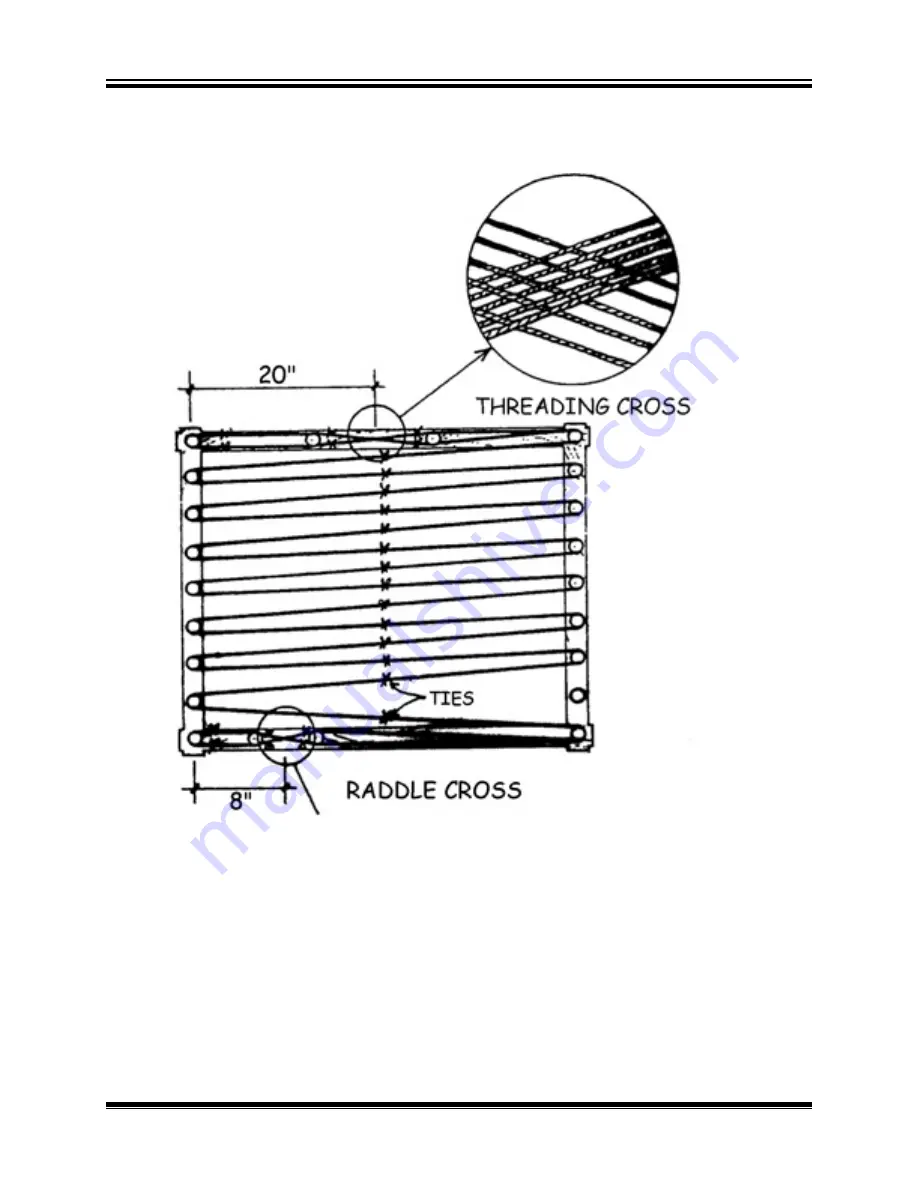
Weaving Instructions
K-Series Loom User Manual
Page | 84
Warping The Plain Beam
1)
The Threading Cross (each thread crosses the next thread in
opposite directions; all are secured in a single loop).
Figure 86 - Warping Board with Two Crosses
2)
The Raddle Cross (warp threads are tied in groups, depending on
how many ends will be put in each section of the raddle).
Securing The Crosses
Before removing the warp from the board or the reel, secure the crosses.
Use four ties to secure each cross, in addition to the tie at the cross axis.
These ties go on each side of both pegs holding the cross.