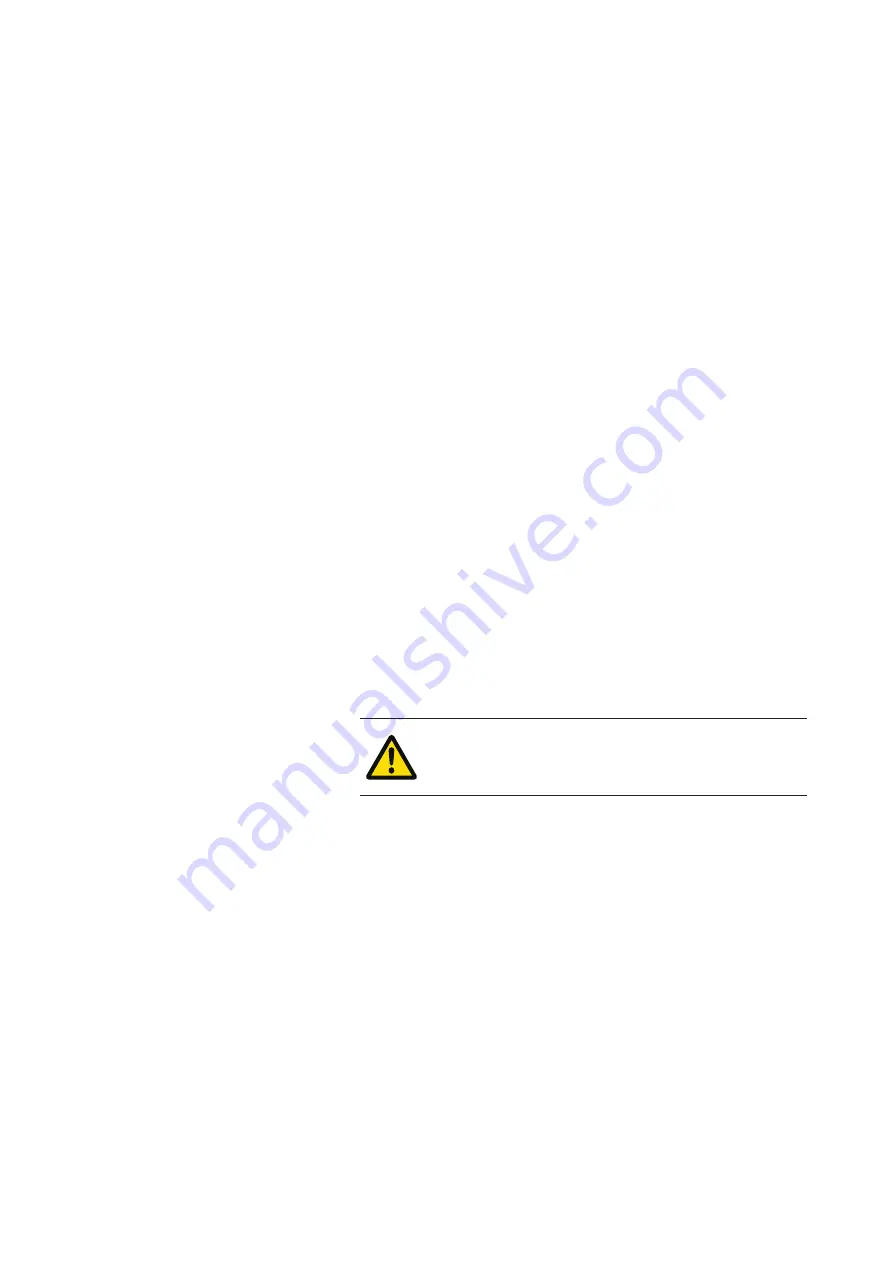
39
6.3.6 Checking door seals and chamber seals (2.5)
The inspection is done to check the seal on the door (the seal at
the bottom edge of the door) and the chamber seal (the seal that
runs along the front edge of the chamber). Failure to perform this
inspection can result in unwanted leakage of water and steam.
Check to make sure both seals are intact and have not become
loose from their tracks. For further instructions, see “10.1 Function
and leakage inspection”.
6.3.7 Checking fastening points for goods holder (2.6)
This inspection is done to ensure that the three fastening points for
the item holders on the inner door are secure. Failure to perform
this inspection may result in the item holder ending up in the wrong
position, with unsatisfactory cleaning as a result.
Check that all item holders that are used are properly attached at
the fastening points.
&KHFNLQJWKHRYHUÀRZFRQQHFWLRQ
This inspection is done to ensure that no water is leaking out from
WKHRYHUÀRZFRQQHFWLRQ7KHLQVSHFWLRQLVLPSRUWDQWWRSUHYHQW
leakage both during a normally functioning process and any major
leakage if the usual drain becomes clogged.
For further instructions, see “10.1 Function and leakage
inspection”.
6.3.9 Internal cleaning of the chamber (2.8)
WARNING!
Concentrated descalers in the steam generator or
steam boiler can be damaging for the machine.
This removes the coating that has formed in the chamber. If it is
not removed, additional dirt and debris can quickly build up in the
chamber. Cleaning is ideally carried out when testing by using a
descaler designed for washing machines.
6.3.10 Checking door and door springs (2.9)
Check that the spring brakes the door so that is closes gently.
Make sure that the door closes properly.
&KHFNWKDWWKHGRRUGRHVQRW¿WWRRFORVHWRWKHVHDOLQJIRUWKH
chamber at the upper edge when closing the door. This can result
in unnecessary wear and tear on the chamber seal. Adjust if
necessary.