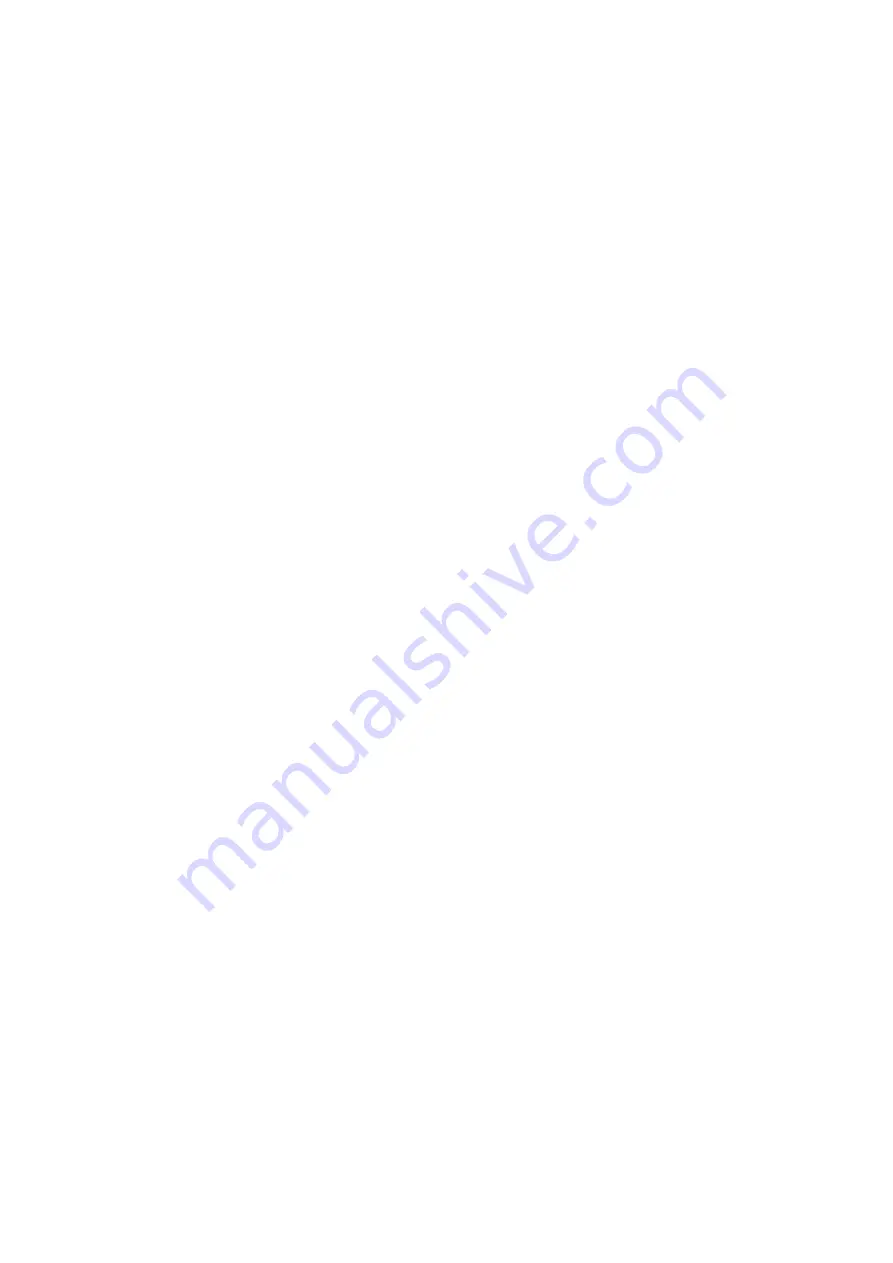
Health and Safety Information
Read all of the instructions in this booklet - including all the WARNINGS and CAUTIONS
- before using this product. If there is any instruction which you do not understand, DO
NOT USE THE PRODUCT.
Safety Signs
WARNING
Indicates a potentially hazardous situation which, if not avoided, could result in death or
personal injury.
CAUTION
Indicates a potentially hazardous situation which, if not avoided, could result in minor or
moderate injury to the user or users, or result in damage to the product or to property.
NOTE
Indicates a potentially hazardous situation which, if not avoided, could result in damage or the loss of
data.
Signs and Symbols used on equipment and Documentation
Caution, risk of electric shock.
Caution, attention to possibility of risk of damage to the product, process or surroundings. Refer
to instruction manual.
Caution, hot surface.
Protective Conductor Terminal.
Observe precautions for handling electrostatic discharge sensitive devices.
Equipment Operation
Use of this instrument in a manner not specified by Land Instruments International may be hazardous.
Read and understand the user documentation supplied before installing and operating the equipment.
The safety of any system incorporating this equipment is the responsibility of the assembler.
Protective Clothing, Face and Eye Protection
It is possible that this equipment is to be installed on, or near to, machinery or equipment operating at
high temperatures and high pressures. Suitable protective clothing, along with face and eye protection
must be worn. Refer to the health and safety guidelines for the machinery/equipment before installing
this product. If in doubt, contact Land Instruments International.
Electrical Power Supply
Before working on the electrical connections, all of the electrical power lines to the equipment must
be isolated. All the electrical cables and signal cables must be connected exactly as indicated in these
operating instructions. If in doubt, contact Land Instruments International.
Storage
The instrument should be stored in its packaging, in a dry sheltered area.
Unpacking
Check all packages for external signs of damage. Check the contents against the packing note.
Lifting Instructions
Where items are too heavy to be lifted manually, use suitably rated lifting equipment. Refer to the
Technical Specification for weights. All lifting should be done as stated in local regulations.
IMPORTANT INFORMATION - PLEASE READ
Contact Us
UK - Dronfield
Land Instruments International
Tel: +44 (0) 1246 417691
Email: [email protected]
Web: www.landinst.com
USA - Pittsburgh
AMETEK Land, Inc.
Tel: +1 412 826 4444
Email: [email protected]
Web: www.ametek-land.com
China
AMETEK Land
China Service
Tel:
+86 21 5868 5111 ext 122
Email: [email protected]
Web: www.landinst.com
India
AMETEK Land
India Service
Tel: +91 - 80 67823240
Email: [email protected]
Web: www.landinst.com
For further details on all AMETEK Land offices, distributors and representatives, please visit
our websites.
Return of Damaged Goods
IMPORTANT If any item has been damaged in transit, this should be reported to the carrier and to the
supplier immediately. Damage caused in transit is the responsibility of the carrier not the supplier.
DO NOT RETURN a damaged instrument to the sender as the carrier will not then consider a claim. Save
the packing with the damaged article for inspection by the carrier.
Return of Goods for Repair
If you need to return goods for repair please contact our Customer Service Department. They will be able
to advise you on the correct returns procedure.
Any item returned to Land Instruments International should be adequately packaged to prevent damage
during transit.
You must include a written report of the problem together with your own name and contact information,
address, telephone number, email address etc.
Design and Manufacturing Standards
The Quality Management System of Land Instruments International is approved to BS EN ISO 9001 for
the design, manufacture and on-site servicing of combustion, environmental monitoring and non-contact
temperature measuring instrumentation.
Registered ISO 9001 Management System approvals apply in the USA
UK Calibration Laboratory: UKAS 0034
USA Calibration Laboratory: ANAB Accredited ISO/IEC 17025
National Accreditation Board for Testing and Calibration Laboratories
approvals apply in India.
Operation of radio transmitters, telephones or other electrical/electronic devices in close proximity
to the equipment while the enclosure doors of the instrument or its peripherals are open, may cause
interference and possible failure where the radiated emissions exceed the EMC directive.
The protection provided by this product may be invalidated if alterations or additions are made to the
structural, electrical, mechanical or pneumatic parts of this system. Such changes may also invalidate the
standard terms of warranty.
Copyright
This manual is provided as an aid to owners of Land Instruments International’s products and contains
information proprietary to Land Instruments International. This manual may not, in whole or part, be
copied, or reproduced without the expressed written consent of Land Instruments International Ltd.
Copyright © 2017 Land Instruments International.
MARCOM0311, Issue 8, 07 September 2017
Summary of Contents for 4500 MKIII
Page 4: ...Opacity and Dust Monitor User Guide Model 4500 MkIII Preface Blank...
Page 6: ...INTRODUCTION A...
Page 29: ...A 23 Model 4500 MkIII Opacity and Dust Monitor User Guide A4 3 Mounting the AFU APS I O...
Page 41: ...GETTING STARTED B...
Page 42: ...Opacity and Dust Monitor User Guide Model 4500 MkIII Preface Blank...
Page 76: ...THEORY OF OPERATION AND APPLICATION C...
Page 86: ...SYSTEM SPECIFICATION D...
Page 91: ...MAINTENANCE E...
Page 108: ...CHANGING THE INSTALLATION PATHLENGTH F...
Page 113: ...INSTRUMENT RECORD SHEETS G...
Page 114: ...Blank...
Page 117: ...OPTIONAL I O MODULES FOR AFU H...
Page 118: ...Blank...
Page 124: ...LONG PATHLENGTH OPTION App 1...
Page 126: ...Opacity and Dust Monitor User Guide Model 4500 MkIII App 1 2...