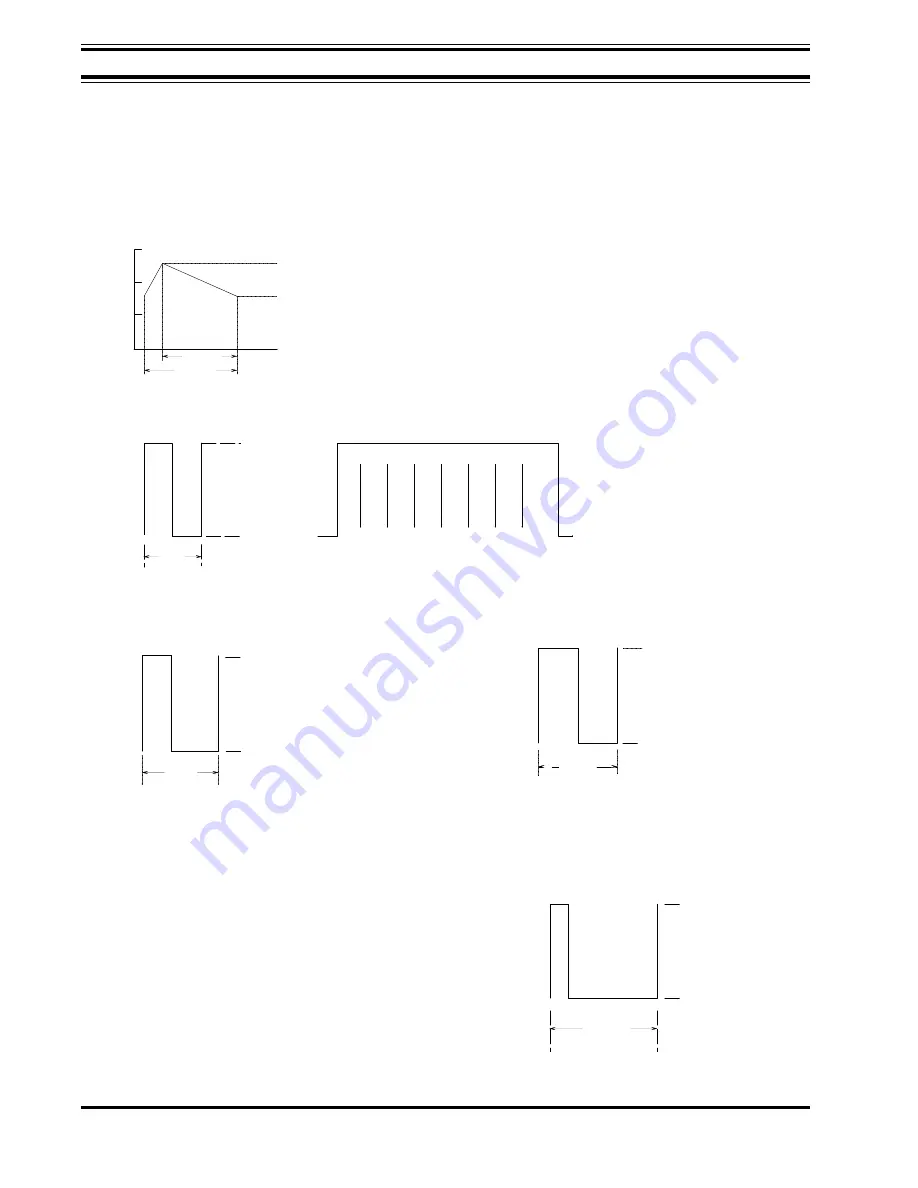
Service
Mini Med Series
0000061122
Waveforms & Voltages
0V
1V
2V
3V
1.121s
1.134s
0
1.7V
2.7V
1. Pin 4 of U2 on Logic Board
2. Pin 9 of U2 on Logic Board
11V
0V
15ms
1 Pulse
7 Pulse Bursts
3. Pin 5 of I.C. U2 on Logic Board
1.13s
11.25 V
0V
Note: Duty cycle = 34%
4. Pin 12 of I.C. U4 on Logic Board = 2.4VDC
5. Pin 13 of I.C. U4 on Logic Board = 0VDC
6. Pin 11 of I.C. U4 on Logic Board = 11.9VDC
7. Pin 5 of I.C. U1 on Logic Board = 11.38VDC
600ms
12 V
Note: Duty cycle = 50%
8. Pin 7 of I.C. U5 on Logic Board
9. Pin 18 of I.C U7 on Logic Board = 10 VDC
10. Pin 15 of I.C. U7 on Logic Board = 0VDC
550ms
Note: Duty cycle = 12%
Pulse present only while
Reset Pushbutton is
depressed.
0V
9.5V
0V
5-20
Summary of Contents for Mini-Medical Series
Page 4: ......
Page 10: ......
Page 12: ......
Page 14: ......
Page 16: ......
Page 26: ...Introduction Mini Med Series 0000061122 ...
Page 28: ......
Page 30: ......
Page 44: ...Installation Mini Med Series 0000061122 Notes 2 14 ...
Page 46: ......
Page 56: ......
Page 66: ......
Page 98: ......
Page 120: ...Parts Mini Med Series 0000061122 6 22 Notes ...
Page 122: ......
Page 129: ...Accessories Mini Med Series 0000061122 Notes 7 7 ...
Page 130: ......
Page 131: ......