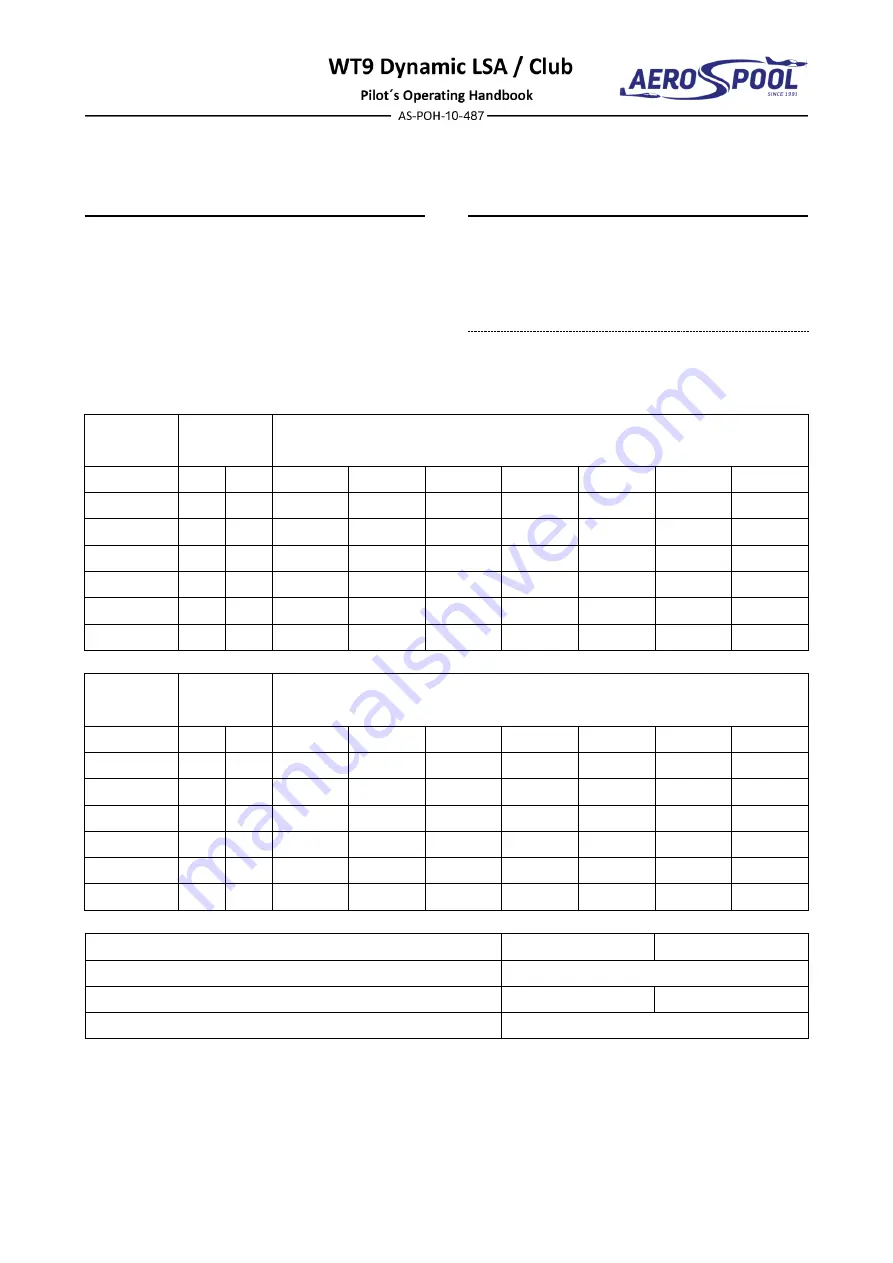
Initial issue
EASA Approved
Page 5-9
5.5
Rate of Climb
Associated conditions:
Example:
Weight
600 kg / 1323 lb
Pressure altitude
6000 ft
CG
Most FWD at MTOW
Outside air temperature
-7
°C
Flaps
FLAPS 0
(0°)
Engine power
Max. takeoff
Climb speed
124 IAS / 67 KIAS
Rate of climb
846 fpm (4.3 m/s)
Pressure
altitude
Climb speed
Rate of climb
(fpm)
ft
IAS KIAS ISA -
30°C
ISA -
20°C
ISA -
10°C
ISA
ISA +
10°C
ISA +
20°C
ISA +
30°C
SL
127
69
1211
1166
1124
1085
1049
1015
983
2000
126
68
1135
1092
1052
1015
980
948
918
4000
125
67
1027
987
951
917
885
856
828
6000
124
67
914
879
846
815
787
760
735
8000
123
66
746
717
689
664
640
619
598
10000
122
66
563
540
519
500
482
465
450
Pressure
altitude
Climb speed
Rate of climb
(m/s)
ft
IAS KIAS ISA -
30°C
ISA -
20°C
ISA -
10°C
ISA
ISA + 10°C
ISA + 20°C
ISA + 3
0°C
SL
127
69
6.2
5.9
5.7
5.5
5.3
5.2
5.0
2000
126
68
5.8
5.5
5.3
5.2
5.0
4.8
4.7
4000
125
67
5.2
5.0
4.8
4.7
4.5
4.3
4.2
6000
124
67
4.6
4.5
4.3
4.1
4.0
3.9
3.7
8000
123
66
3.8
3.6
3.5
3.4
3.3
3.1
3.0
10000
122
66
2.9
2.7
2.6
2.5
2.4
2.4
2.3
Best angle of climb airspeed V
X
(at SL)
100 IAS
54 KIAS
Rate of climb at V
X
(at SL)
985 fpm (5.0 m/s)
Best rate of climb airspeed V
Y
(at SL)
127 IAS
69 KIAS
Rate of climb at V
Y
(at SL)
1085 fpm (5.5 m/s)
Summary of Contents for WT9 Dynamic LSA / Club
Page 2: ...This page is left blank intentionally...
Page 4: ...Page B Initial issue This page is left blank intentionally...
Page 8: ...Page F Initial issue Chapter Page Date Chapter Page Date...
Page 10: ...Page H Initial issue This page is left blank intentionally...
Page 20: ...Page 1 4 Initial issue Three View Drawing Fig 1 1 Three view drawing...
Page 94: ...Page 4 28 Initial issue This page is left blank intentionally...
Page 109: ...Initial issue EASA Approved Page 5 15 Fig 5 2 Crosswind U S Standard Units...
Page 110: ...Page 5 16 EASA Approved Initial issue This page is left blank intentionally...
Page 119: ...Initial issue EASA Approved Page 6 9 Fig 6 2 Operating Weight CG limit Metric Units...
Page 120: ...Page 6 10 EASA Approved Initial issue Fig 6 3 Operating Weight CG limit U S Standard Units...
Page 134: ...Page 6 24 EASA Approved Initial issue This page is left blank intentionally...
Page 148: ...Page 7 14 Initial issue Fig 7 5 Arrangement screen 1 Fig 7 6 Arrangement screen 2...
Page 149: ...Initial issue Page 7 15 Fig 7 7 Arrangement screen 3 Fig 7 8 Arrangement screen 4...
Page 150: ...Page 7 16 Initial issue Fig 7 9 Arrangement screen 5 Fig 7 10 Arrangement screen 6...
Page 162: ...Page 7 28 Initial issue Fig 7 16 Arrangement screen 1 Fig 7 17 Arrangement screen 2...
Page 163: ...Initial issue Page 7 29 Fig 7 18 Arrangement screen 3 Fig 7 19 Arrangement screen 4...
Page 164: ...Page 7 30 Initial issue Fig 7 20 Arrangement screen 5 Fig 7 21 Arrangement screen 6...
Page 165: ...Initial issue Page 7 31 Fig 7 22 Arrangement screen 7 Fig 7 23 Arrangement screen 8...
Page 178: ...Page 7 44 Initial issue This page is left blank intentionally...
Page 188: ...Page 8 10 Initial issue Fig 8 5 Fuel draining...
Page 198: ...Page 8 20 Initial issue This page is left blank intentionally...
Page 204: ...Page 9 6 Initial issue This page is left blank intentionally...