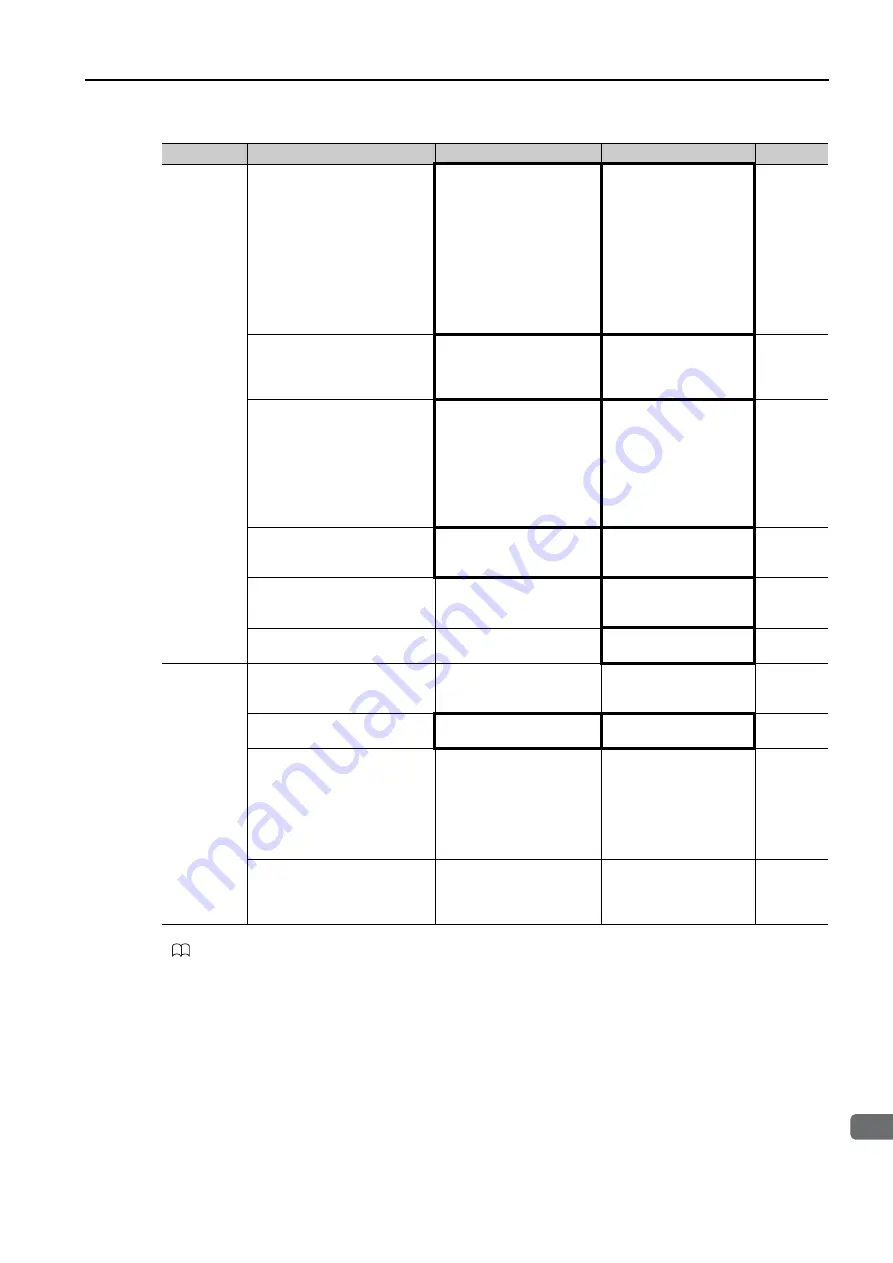
5.1 FT40 Specification
5.1.7 Troubleshooting Based on the Operation and Conditions of the Servomotor
5-57
5
Maintenance
*
Refer to the following manual for details.
Σ
-7-Series
Σ
-7S SERVOPACK with MECHATROLINK-III Communications References Product Manual
(Manual No.: SIEP S800001 28)
Position
Deviation
(without
Alarm)
The encoder was subjected
to excessive vibration or
shock.
Check to see if vibration
from the machine
occurred.
Check the Servomotor
installation (mounting sur-
face precision, securing
state, and alignment).
Check the linear encoder
installation (mounting sur-
face precision and secur-
ing method).
Reduce machine vibra-
tion. Or, improve the
mounting state of the
Servomotor or linear
encoder.
–
The coupling between the
machine and Servomotor is
not suitable.
Check to see if position
offset occurs at the cou-
pling between machine
and Servomotor.
Correctly secure the
coupling between the
machine and Servomo-
tor.
–
Noise interference occurred
because of incorrect I/O sig-
nal cable specifications.
Check the I/O signal
cables to see if they sat-
isfy specifications. Use a
shielded twisted-pair wire
cable or a screened
twisted-pair cable with
conductors of at least
0.12 mm
2
.
Use cables that satisfy
the specifications.
–
Noise interference occurred
because an I/O signal cable
is too long.
Check the lengths of the
I/O signal cables.
The I/O signal cables
must be no longer than
3 m.
–
An encoder fault occurred.
(The pulse count does not
change.)
–
Replace the Servomo-
tor or linear encoder.
–
A failure occurred in the SER-
VOPACK.
–
Replace the SERVO-
PACK.
–
Servomotor
Overheated
The surrounding air tempera-
ture is too high.
Measure the surrounding
air temperature around
the Servomotor.
Reduce the surround-
ing air temperature to
40
°
C or less.
–
The surface of the Servomo-
tor is dirty.
Visually check the surface
for dirt.
Clean dirt, dust, and oil
from the surface.
–
There is an overload on the
Servomotor.
Check the load status
with a monitor.
If the Servomotor is
overloaded, reduce the
load or replace the
Servo Drive with a
SERVOPACK and Ser-
vomotor with larger
capacities.
–
Polarity detection was not
performed correctly.
Check to see if electrical
angle 2 (electrical angle
from polarity origin) at any
position is between
±
10
°
.
Correct the settings for
the polarity detection-
related parameters.
–
Continued from previous page.
Problem
Possible Cause
Confirmation
Correction
Reference
Содержание SGD7S-R70A20A023F40B
Страница 52: ...3 7 Monitoring 3 23...